I sistemi di strutture spaziali, come i reticoli, sono strutture portanti efficienti che sono facili da adattare geometricamente e ben adattate per costruzioni senza colonne, a lungo spanning, come hangar e terminali, e nella creazione di geometrie a forma libera. Poiché queste strutture devono sopportare sia le forze di compressione che quelle di trazione, sono spesso costruite con materiali isotropici come l’alluminio e l’acciaio. Il cemento armato è un’altra opzione, ma anche con l’aiuto di avanzamenti più recenti, è meno comune a causa dei costi elevati e del “pesante” aspetto delle strutture in cemento.
I ricercatori Norman Hack, Hendrik Lindemann e Harald Kloft della Technical University Braunschweig hanno pubblicato un documento, intitolato ” Strutture spaziali modulari adattive per la stampa 3D a getto di cemento “, sul loro lavoro nello sviluppo di un “sistema modulare di costruzione digitale” per rendere leggere strutture spaziali leggere cemento armato.
L’abstract recita: “Per la progettazione e la fabbricazione, viene presentato un flusso di lavoro digitale, che include la razionalizzazione di una geometria a forma libera in moduli spaziali adattivi composti interamente da componenti planari. Per una fabbricazione rapida e precisa, questi componenti sono stampati in 3D utilizzando una nuova tecnologia di stampa in calcestruzzo 3D chiamata “Shotcrete 3D Printing”. La ricerca in corso è dimostrata da un prototipo iniziale in scala reale di un modulo spaziale esemplare. “
L’obiettivo era creare un “sistema di costruzione digitale integrativo per strutture spaziali modulari adattive”, utilizzando il cemento armato, che considera la logistica del cantiere, gli aspetti economici ed ecologici, i vincoli di fabbricazione, le proprietà dei materiali e le prestazioni strutturali.
“In considerazione di ciò, questo documento descrive un sistema di costruzione digitale e un flusso di lavoro digitale, in cui una geometria a mano libera viene prima razionalizzata in pannelli planari, in secondo luogo sviluppati in moduli spaziali e che possono essere fabbricati rapidamente e senza causare sprechi di costruzione con 3D tecnologia di stampa concreta “, hanno spiegato i ricercatori.
Diversi altri gruppi di ricerca hanno esaminato l’uso del cemento armato per la creazione di strutture reticolari geometricamente complesse e strutturalmente ottimizzate, tra cui:
Il padiglione Hedracrete, che ha esaminato le strutture poliedriche spazialmente complesse sviluppate sulla grafica statica 3D
Il progetto Opticut, che ha esplorato come rendere efficienti strutture topologicamente ottimizzate con il taglio di filo abrasivo robotizzato
XTree, che utilizzava quattro segmenti di calcestruzzo stampato in 3D per realizzare la cassaforma e la struttura di supporto temporanea per una colonna a traliccio
Il team di TU Braunschweig ha fatto riferimento a un altro progetto – quello di Pier Luigi Nervi, che ha sviluppato i ganci per aeromobili per l’Aeronautica Militare italiana basati su un sistema di traliccio di travi reticolari prefabbricate e spaziali. Ha creato un sistema di capriate in calcestruzzo prefabbricate planari che, una volta assemblate, formano una struttura a volta a forma di diamante. Quindi, le truss sono state unite monoliticamente colando il cemento nelle fessure.
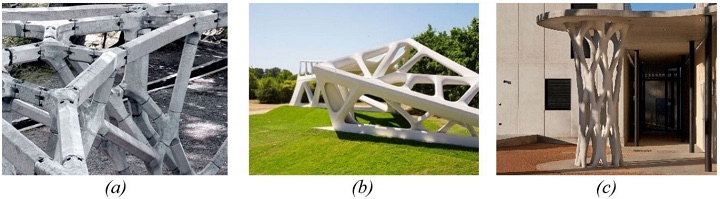
Questo metodo, che ha risparmiato tempo, peso e materiale Nervi, ha ispirato i ricercatori nei loro sforzi per creare un sistema strutturale spaziale con componenti identici.
Il loro concetto di sistema di costruzione si basa su un flusso di lavoro digitale che inizia con la razionalizzazione di una geometria a mano libera in moduli spaziali di componenti planari. Successivamente, questi moduli vengono aperti digitalmente in modo da generare percorsi di fabbricazione e i componenti vengono quindi stampati in 3D come elementi planari.
Poiché tutti gli elementi della struttura dovevano essere planari, il flusso di lavoro necessario per razionalizzare “una data superficie NURBS libera in moduli spaziali” di componenti planari quadrilaterali. Nell’ultima fase, i quadrilateri planari vengono trasferiti in una struttura reticolare spaziale adattata a una specifica condizione di carico. Quindi, le coordinate e la velocità dell’utensile sono tradotte in codice G che può essere utilizzato con Siemens Sinumeric.
L’installazione robotizzata è stata completata presso il Digital Building Fabrication Laboratory dell’università: una struttura di fabbricazione robotizzata che utilizza metodi di produzione sia additivi che sottrattivi per produrre strutture su larga scala. Il team ha installato una piastra in legno planare nell’area di lavoro, quindi ha caricato i dati di fabbricazione per ciascun componente del modulo, prima di avviare il processo di miscelazione del calcestruzzo.
I ricercatori hanno utilizzato la loro nuova tecnologia di stampa 3D Shotcrete (SC3DP), che non solo estrude il materiale ma lo spruzza anche con la pressione per costruire una struttura 3D. Questo metodo offre un’adesione dello strato superiore, può integrare rinforzi e offre “il potenziale per spruzzare contro superfici verticali e sporgenze”.
Ciascuno dei tre componenti del modulo è stato stampato in 3D separatamente. Dopo che i primi due strati furono stampati, 8 strisce da 100 cm da una griglia di rinforzo in fibra di carbonio furono posizionate sopra, e lo strato finale fu stampato e spruzzato per incorporarlo.
Dopo la post-elaborazione verde e due giorni di stagionatura, gli elementi planari da 60 kg sono stati staccati dalla piastra di base. Il prototipo finale 2,2 x 1,5 x 1 m, stampato in soli 25 minuti con 12 minuti di irrorazione e otto minuti di post-elaborazione, fa parte di una struttura più grande che è stata assemblata in soli cinque minuti.
“L’irrorazione ha comportato una buona compattazione, è stata rapida e ha offerto un controllo costante dell’altezza. Tuttavia, le procedure di avvio e di arresto del processo di irrorazione non sono ancora precisamente controllate, il che richiede di estendere il punto iniziale e finale del contorno “, hanno scritto i ricercatori. “Per quanto riguarda il rinforzo, è diventato evidente che l’utilizzo di strisce pretagliate di stuoie in fibra di carbonio è una misura efficace per ridurre lo spessore strutturale degli elementi. Tuttavia, il posizionamento manuale non si è dimostrato sufficientemente preciso, causando conflitti di collisione durante il taglio dei bordi durante la post-elaborazione … A causa del peso ridotto dei componenti, il montaggio era possibile solo con tre persone. Poiché nessun meccanismo di connessione è stato integrato in questo primo prototipo, sono state utilizzate cinghie di ancoraggio per connettere i componenti. “
I ricercatori hanno concluso che sono necessarie ulteriori indagini, come lo sviluppo ulteriore del flusso di lavoro computazionale e la fabbricazione dei moduli. Il prossimo passo sarà “realizzare strutture spaziali più grandi” realizzate con diversi moduli ed eseguire un test strutturale.
Hangar prefabbricati dell’Aeronautica militare, Pier Luigi Nervi, Orvieto, 1939: (a) vista interna del guscio reticolare prima del fasciame; (b) travi prefabbricate in traliccio durante l’assemblaggio; (c) dettaglio del giunto prima del lancio. Geometria finale: (a) Struttura planare e strutturalmente adattata con parti più spesse contrassegnate in arancione e membri più sottili in blu; (b) vista dall’alto della struttura e moduli srotolati digitalmente. Generazione del modulo: (a) superficie iniziale suddivisa in quadrilateri a doppia curvatura con colori che indicano la doppia curvatura; (b) griglia quadrilatera planarizzata con doppie superfici curve che forniscono profondità strutturale (c) griglia quadrilatera planarizzata con struttura spaziale planare, il singolo colore indica planarità. Fabbricazione: (a) irrorazione degli elementi; (b) tagliare i bordi nello stato verde del calcestruzzo; (c) levigare il bordo della superficie squadrata. Esempi contemporanei per strutture spaziali in cemento armato: (a), Hedracrete; (b) Opticut; (c) Colonna XTree di Aix-en-Provence.Esempi contemporanei per strutture spaziali in cemento armato: (a), Hedracrete; (b) Opticut; (c) Colonna XTree di Aix-en-Provence. Assemblaggio di un modulo: (a) assemblaggio con tre persone; (b) elemento assemblato; (c) posizionamento utilizzando una gru.