IL PROGETTO AMAZING ESPLORA LA PRODUZIONE DI MATERIE PRIME A BASSE EMISSIONI CON MEMBRANE STAMPATE IN 3D
Un consorzio tedesco-olandese che abbraccia l’industria e la scienza sta cercando di rendere la produzione di plastica più sostenibile sviluppando e integrando membrane stampate in 3D nel processo di produzione.
Il progetto Additive Manufacturing for Zero-Emission Innovative Green Chemistry, o in breve AMAZING, svilupperà un processo a membrana per separare i sottoprodotti dal processo di produzione della plastica e renderli disponibili per un ulteriore utilizzo.
Aziende come l’azienda chimica BASF , la società di scienza dei materiali Dow e il gigante dell’energia Shell presteranno la loro esperienza al progetto, lavorando a fianco dell’Istituto di ricerca sull’energia e sul clima , l’ Istituto per la tecnologia dei processi sostenibili (ISPT), l’ Università di Twente e l’ Università tecnologica di Eindhoven .
Oltre a fornire vantaggi ambientali, i partner ritengono che i processi sviluppati nel progetto potrebbero comportare vantaggi economici significativi per l’industria europea.
Molte materie plastiche sono realizzate in etilene e propilene, che appartengono a un gruppo di idrocarburi insaturi chiamati olefine. Le materie prime per queste olefine sono gli alcani, come la benzina leggera e la nafta, che vengono scomposti in un processo termico noto come steam cracking che avviene all’interno di un reattore.
Durante questo processo, l’idrogeno viene rilasciato come sottoprodotto e deve essere laboriosamente separato per un ulteriore utilizzo. Il processo di steam cracking richiede temperature fino a 850 gradi centigradi che vengono generate attraverso la combustione di combustibili fossili, rendendo la produzione di olefine uno dei processi industriali più dispendiosi in termini di energia che genera grandi quantità di emissioni.
Il progetto AMAZING sta cercando di rendere la produzione di olefine più sostenibile sviluppando un processo basato su membrana che separa i prodotti dal processo di cracking durante la reazione e li rende disponibili per un ulteriore utilizzo. Per ridurre ulteriormente la quantità di emissioni prodotte dal processo, il reattore utilizzato nel progetto AMAZING sarà riscaldato con elettricità proveniente da energie rinnovabili.
Sulla base del numero di impianti di steam cracking attualmente in funzione, i partner del progetto stimano che il loro processo potrebbe potenzialmente far risparmiare circa 5,2 terawattora (TWh) di energia e 3.871 chilotoni (kt) di CO2 all’anno nella sola Germania. Successivamente, il processo sviluppato potrebbe fornire significativi risparmi sui costi per i sistemi azionati elettricamente rispetto ai sistemi riscaldati a combustibile.
I partner del progetto utilizzeranno la stampa 3D per creare e integrare una membrana ceramica nel reattore che consente la produzione di olefine e la separazione simultanea dell’idrogeno puro. La membrana stampata in 3D è progettata con una funzione catalitica che abbassa la temperatura di deidrogenazione degli alcani che consente la separazione dell’idrogeno dal gas prodotto.
Distribuendo la stampa 3D per creare la membrana, i partner possono adattare la sua superficie, microstruttura e composizione chimica in modo specifico per il processo di cracking. Varie proprietà delle membrane possono essere adattate e ottimizzate per migliorare l’efficienza all’interno del processo, ad esempio quanto bene la membrana trasporta l’idrogeno separato e quanto efficacemente supporta la separazione dell’idrogeno dagli alcani.
La stampa 3D consente inoltre di testare facilmente prototipi e componenti di membrana e, se la tecnologia si dimostra adatta per un uso su larga scala ed è economicamente fattibile, i partner ritengono che i moduli di membrana stampati in 3D potrebbero essere prodotti su scala commerciale in futuro.
Oltre a migliorare l’efficienza energetica, il processo proposto produce anche idrogeno utilizzabile direttamente, che in precedenza era stato utilizzato solo termicamente come sottoprodotto del processo di cracking. Per raggiungere questo obiettivo, i partner creeranno una membrana a film sottile a conduzione mista (MIEC) che rimuove l’idrogeno in modo che possa essere utilizzato come vettore energetico o materia prima chimica.
I due processi proposti nel progetto mostrano anche promesse per applicazioni oltre la produzione di olefine, come l’uso di idrogeno generato in modo sostenibile in altri processi industriali o nel settore della mobilità per ridurre le emissioni e quindi sostenere le ambizioni climatiche neutre dell’Europa per il 2050.
Per dimostrare il potenziale tecnico delle loro membrane stampate in 3D e filmate, i partner del progetto implementeranno il loro reattore a membrana in un dimostratore per valutarne la fattibilità per un uso su larga scala.
Negli ultimi anni, le aziende si sono rivolte sempre più alla stampa 3D come forma di produzione più efficiente rispetto ai processi esistenti, sebbene vi siano varie conclusioni riguardo al suo impatto sull’ambiente .
Per quanto riguarda il settore delle energie rinnovabili, la società di produzione industriale Siemens ha precedentemente utilizzato la stampa 3D per accelerare la tecnologia delle turbine a gas all’avanguardia che consente il funzionamento di combustibili rinnovabili e più recentemente ha sviluppato una nuova catena di riparazione digitale per stampare in 3D nuove funzionalità su pale di turbine a gas prodotte convenzionalmente.
La progettazione e la produzione delle pale delle turbine è stata esplorata anche nel settore eolico da GE Research . Proprio il mese scorso, la società è stata incaricata di aumentare la competitività dell’energia eolica onshore e offshore attraverso la stampa 3D dal Dipartimento dell’Energia degli Stati Uniti , insieme a LM Wind Power , Oak Ridge National Laboratory e National Renewable Energy Laboratory .
Nel settore nucleare, le parti stampate in 3D sviluppate dal Dipartimento dell’Energia dell’ORNL potrebbero essere testate nei reattori nucleari attualmente in funzione questa primavera. Secondo quanto riferito, le staffe di assemblaggio del combustibile di ORNL saranno i primi componenti relativi alla sicurezza stampati in 3D ad essere installati in una centrale nucleare.
ORNL sta guidando il programma dimostrativo Transformational Challenge Reactor (TCR), che prevede lo sviluppo di un nucleo di un reattore nucleare utilizzando la stampa 3D al fine di ridurre i costi di produzione e i tempi di consegna, migliorando la sicurezza.
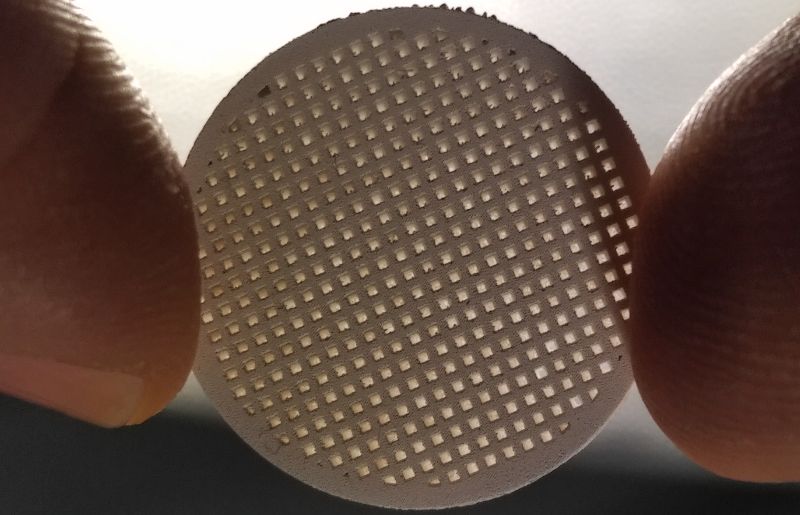