L’arte di creare pezzi unici di qualità industriale trova il suo alleato ideale nella stampa 3D. Tuttavia, per ottenere superfici impeccabili e strutture perfettamente dritte, spesso è necessario combinare la stampa 3D con la lavorazione CNC. In questa impresa, KraussMaffei dimostra di essere un pioniere, portando insieme le competenze delle sue sedi di Parsdorf (specializzata nella produzione additiva) e Harderberg/Georgsmarienhütte (specializzata nella produzione di utensili), offrendo ai clienti un servizio completo.
Il punto di partenza di questa avventura è la potente stampante di grandi dimensioni powerPrint, che è in grado di produrre componenti con dimensioni fino a 2 x 2,5 x 2 metri. I clienti possono scegliere di acquistare direttamente una stampante di questo tipo o di usufruire del servizio di stampa su richiesta offerto da KraussMaffei. In quest’ultimo caso, l’azienda gestisce l’intero progetto, dalla preparazione dei dati all’interfacciamento perfetto.
Inizialmente, quando i clienti hanno chiesto questo servizio, Ender Murat Ferat, ingegnere di progetto della produzione additiva presso la sede di Parsdorf, non aveva considerato immediatamente i suoi colleghi produttori di utensili di Harderberg. Tuttavia, l’efficienza e la preservazione del know-how hanno presto spinto verso una collaborazione interna più efficace.
Il team di Harderberg era già esperto nella fresatura della plastica, utilizzando principalmente ureolo, un poliuretano saturo con riempitivi o resina epossidica, per creare prototipi e modelli di rivestimenti in pelle per l’industria automobilistica. Tuttavia, con l’introduzione del PETG riciclato con il 30% di rinforzo in fibra di vetro per la stampa 3D, sono emersi nuovi orizzonti.
La fresatura della plastica richiede macchinari diversi rispetto alla lavorazione del metallo, con una maggiore asportazione di materiale. Sono necessarie macchine altamente dinamiche per ottenere velocità di taglio elevate e tempi di produzione rapidi. Gli utensili devono essere estremamente affilati, e durante i test con il PET rinforzato con fibra di vetro è emerso che le frese con punta diamantata erano necessarie per resistere al materiale abrasivo, riducendo notevolmente l’usura.
Un aspetto cruciale è la levigatura completa della tipica struttura a strati della produzione additiva, che è stata raggiunta. Ender Murat Ferat dimostra la finezza delle superfici con piastre campione. Sebbene abbiano raggiunto una profondità di rugosità di RZ 12, Thorsten Richter, capo squadra del reparto di fresatura di Harderberg, afferma che è possibile ottenere superfici ancora più lisce con un po’ più di tempo.
Un progetto che ha dimostrato il potenziale della collaborazione tra le sedi di Parsdorf e Harderberg è stato la realizzazione di uno stampo in sabbia per cuscini di pressione. Questo procedimento coinvolge la creazione di uno stampo negativo per la formatura di uno stampo in sabbia, che successivamente trattiene il metallo liquido. Questo stampo in sabbia viene distrutto durante la sformatura, mentre il corpo 3D fresato può essere riutilizzato. In passato, si utilizzava principalmente l’ureolo per questo scopo, ma ora il PETG riciclato con rinforzo in fibra di vetro offre vantaggi significativi. Inoltre, la stampa 3D offre una soluzione economica rispetto all’ureolo, anche se il PETG ha un costo base più elevato.
Questa collaborazione tra produzione additiva e costruzione di utensili offre vantaggi notevoli ad entrambe le parti, permettendo a KraussMaffei di offrire ai clienti una soluzione completa con finiture impeccabili. Inoltre, i clienti che utilizzavano precedentemente modelli in ureolo ora possono beneficiare del PETG GF30 più resistente alla rottura.
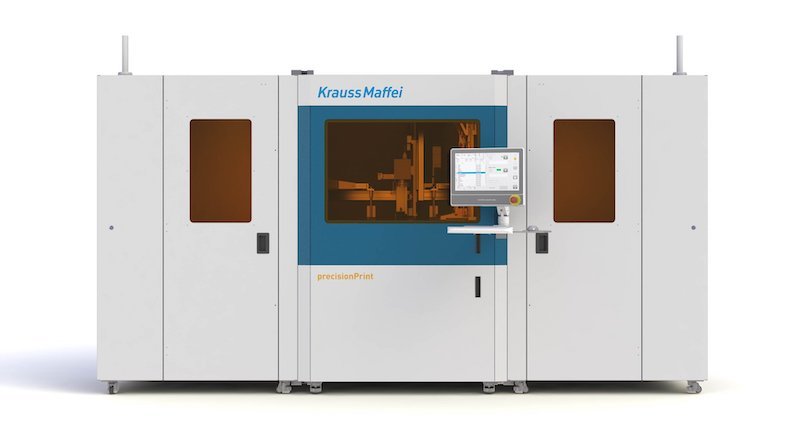