Il profilo dell’azienda
Fondata a Wecker, in Lussemburgo, Gilles Tooling GmbH è nota nel mondo delle due ruote per pedane regolabili, comandi arretrati e componenti high-end lavorati dal pieno. Da oltre vent’anni fornisce a team endurance e appassionati stradali pezzi che devono resistere a vibrazioni, urti e temperature del motorsport. Per restare competitiva con gamme sempre più personalizzate, la direzione ha deciso di portare in casa la fabbricazione additiva, integrandola nel reparto prototipi e in quello di produzione in lotti ridotti.
Perché passare all’additivo
La domanda di configurazioni su misura cresce: singoli piloti chiedono regolazioni millimetriche, mentre costruttori OEM pretendono campionature in pochi giorni. Con le macchine tradizionali il lead-time complessivo superava spesso le quattro settimane; oggi un’end-to-end con stampa 3D, finitura minima in CNC e anodizzazione si chiude in meno di cinque giorni, con un taglio dei costi di attrezzaggio stimato al 70 %.
Il parco macchine Markforged installato
Gilles Tooling ha scelto la gamma Markforged distribuita da Mark3D:
-
X7 per parti strutturali in Onyx rinforzato con fibra continua di carbonio;
-
Metal X System per staffe in acciaio 17-4 PH e inserti in Inconel 625;
-
Software Eiger per la gestione di codice, tracciabilità lotti e simulazione FEM integrata.
Le stampanti lavorano in cella a ciclo continuo, supervisionate da un solo operatore su tre turni. Il case-study ufficiale parla di circa 2 500 componenti/anno già spostati dal CNC al 3D ed evidenzia un funzionamento lights-out che abbatte i colli di bottiglia del weekend.
Dal concept alla pista: applicazioni concrete
-
Pedane FXR2-H01: testate per 1 000 km alla “DMV 1000 km Hockenheim”, hanno beneficiato di un ciclo design-test di appena nove giorni, contro i 30 del vecchio iter con utensili in alluminio.
-
Dime di saldatura sostitutive in Onyx FR con fibra vetro-HSHT, capaci di resistere a 170 °C in forno verniciatura.
-
Maschere di controllo con inserti magnetici per fare prove dimensionali al 100 % in linea, riducendo il tempo di setup da 45 a 10 minuti.
Oltre al reparto racing, il 3D copre ora anche linee aftermarket e produzioni OEM in tirature fra 30 e 150 pezzi, dove lo stampaggio a iniezione non risulterebbe economicamente sostenibile. LinkedInMark3D
Effetti su costi, logistica e sostenibilità
-
Riduzione stock: le varianti restano in digitale fino all’ordine, limando il magazzino grezzi del 35 %.
-
Iterazione rapida: fino a 12 versioni di un comando freno possono uscire in un’unica notte, permettendo ai collaudatori di scegliere la migliore già nella sessione successiva.
-
Semplificazione supply-chain: i supporti stampati localmente rimpiazzano distanziali torniti da fornitori esterni, con un risparmio di circa 120 € per elemento e la certezza di tracciabilità interna dei materiali.
Prossimi passi
L’azienda valuta l’ampliamento della cella con la nuova FX10 per volumi medi in poliammide rinforzata e sta testando Onyx ESD per componenti elettrificati dedicati alle moto ibride in sviluppo. È inoltre allo studio l’introduzione di sensori IoT direttamente co-stampati nelle pedane per acquisire dati di vibrazione in pista senza cablaggi esterni. Gilles Tooling punta così a un modello “design-to-data” dove il pezzo consegnato porta con sé gemello digitale e telemetria embedded.
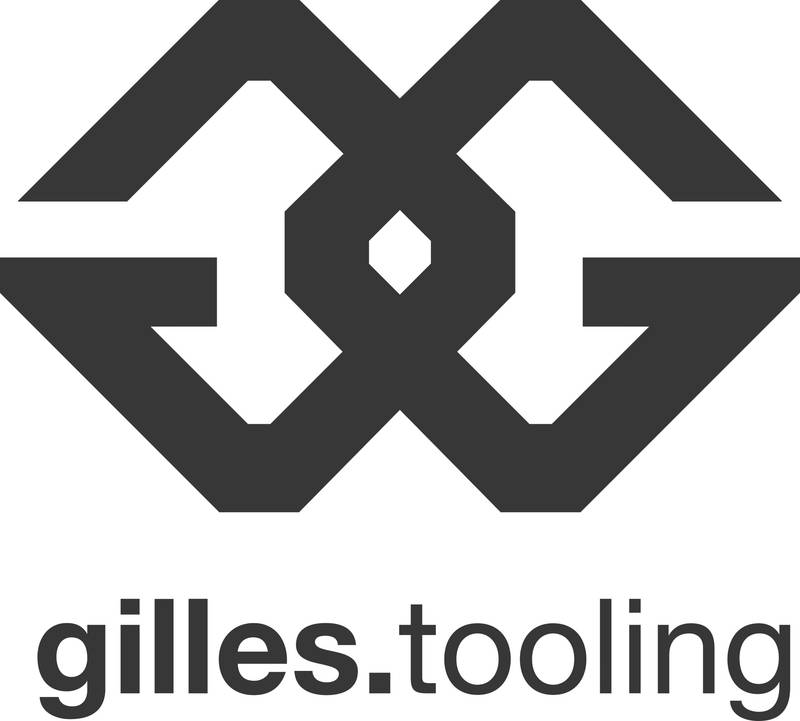