Le ultime tecnologie, prospettive e tendenze del mercato AM nel 2023 (intervista con il Dr.-Ing. Vincent Morrison, CEO di AIM3D GmbH, Rostock, Germania)
Dr. Morrison, quale è la sua previsione per il futuro della stampa 3D e dell’industria AM nel 2023?
L’industria della stampa 3D sta continuando a svilupparsi in modo molto dinamico. Ciò è dovuto alla concorrenza tra diversi processi di stampa 3D e ai progressi tecnici nell’ingegneria delle macchine e dei processi. In generale, ciò conferma che la maturità industriale della stampa 3D rispetto alle strategie di produzione convenzionali (fusione o fresatura) continua a crescere. I criteri di questa “concorrenza” sono la velocità di costruzione, le dimensioni delle parti e l’efficienza economica dei costi unitari. Questi fattori definiscono le decisioni di investimento dei clienti.
Per questi motivi, ci sono molti approcci interessanti e nuovi per la produzione di componenti nel segmento di mercato della produzione in serie di piccole e medie dimensioni (fino a 100.000 parti/anno). Ciò si applica sia alla stampa 3D di metalli e polimeri che alle applicazioni in ceramica.
Per gli utenti di attrezzature di stampa 3D, ciò porta a una maggiore domanda di macchine più produttive e materiali più economici, poiché il throughput delle macchine deve aumentare al fine di ridurre il costo per parte. La pressione competitiva determinata dai costi unitari sta spingendo i fornitori di servizi di stampa 3D a guardare alla generazione più recente di macchine e sistemi. Ciò si applica in particolare alle future decisioni di investimento.
Può parlare di strategie AM che si stanno consolidando nell’industria oggi?
Dopo più di 20 anni di sviluppo, la stampa 3D è passata da una strategia di prototipazione rapida a una strategia di produzione in serie di piccole e medie dimensioni. Le ragioni sono principalmente l’aumento delle velocità di costruzione e il miglioramento della precisione. Queste velocità di costruzione combinati con la precisione hanno come risultato un continuo aumento della competitività rispetto ai processi convenzionali. La stampa 3D ora integra lo spettro dei processi consolidati.
Molti fornitori di primo e secondo livello dell’industria hanno ormai sviluppato una buona conoscenza delle possibilità e dei limiti dei processi AM. Inoltre, istituti di ricerca, università e imprese specializzate nel supportare le startup stanno assistendo gli utenti che sono nuovi nel mondo dell’AM o che stanno ottimizzando i loro processi. La conoscenza degli esperti consente un’entrata più rapida sul mercato, ma accorcia anche il ciclo di time-to-market. Un esempio tra molti è Faye Mills, una scienziata del Manufacturing Technology Centre (MTC), un’organizzazione indipendente di ricerca e tecnologia a Coventry (Regno Unito. Faye Mills utilizza il nostro sistema CEM per progetti da parte di clienti finali per testare nuovi materiali nel settore dei metalli, sviluppare linee guida per la progettazione di componenti e per l’ottimizzazione orientata all’applicazione dei cicli di sinterizzazione. Tali istituti esistono in molti paesi.
L’industria e la ricerca ora hanno la conoscenza industriale per evitare le strutture di supporto e possiedono i giusti metodi per effettuare una lavorazione post-produzione delle parti conveniente in termini di costo. Pertanto, la stampa 3D è diventata sempre di più un passaggio di processo all’interno della catena di produzione e non viene più vista come l’unico passaggio di processo. La frase chiave qui è la catena di processo 3D integrata e digitale.
L’industria è anche riuscita a trasferire questa conoscenza dal livello di processo e prototipo alla fase di progettazione e alla comunicazione con il cliente finale.
Allo stesso tempo, tuttavia, dobbiamo valutare i punti di forza unici di una strategia additiva, come la produzione senza attrezzi, la libertà di geometria, i design bionici o la produzione su richiesta, per utilizzare solo alcuni parole chiave. “Pensando” al design con la tecnologia 3D in futuro, emergeranno progettazioni innovative di componenti che si liberano delle limitazioni delle strategie di produzione convenzionali. Qui c’è ancora molto potenziale da sfruttare.
Quali vantaggi vede nell’uso di granuli commercialmente disponibili per plastica e metalli e come valuta gli sviluppi futuri del mercato?
Con l’aiuto delle stampanti 3D a granuli, le aziende possono sviluppare i loro prototipi dalla fase iniziale fino alla produzione in serie utilizzando materiali e macchine identiche, commercialmente disponibili. La nuova generazione di sistemi di stampa industriale a estrusione di granuli (MEX) è fondamentale per questo. Questo non solo completa il ciclo di sviluppo per i polimeri dalla fase di prototipazione alla produzione in serie per la prima volta nell’industria AM, ma consente anche al numero di parti prodotte con la produzione in serie AM di crescere in futuro.
In termini di processo di stampa, queste stampanti MEX a granuli sono molto simili al ben noto processo MEX/FFF a filamento. Per questo motivo, possono essere rapidamente adattate a diverse industrie. Inoltre, queste stampanti a granuli non solo ridurranno i costi unitari, ma aumenteranno anche il numero di materiali polimerici disponibili nel mondo dell’AM da diverse centinaia a più di 10.000. Inoltre, molte di queste stampanti possono stampare contemporaneamente due o tre materiali nello stesso lavoro di stampa, quindi hanno la capacità di stampare componenti multi-componente. Ad esempio, una parte in poliammide 6 con il 50% di fibre di vetro (PA6-50GF) e una guarnizione TPE possono essere stampati in modo estremamente economico e competitivo con un materiale portante solubile. Le opzioni offerte da questa tecnologia di sistema consentono anche una combinazione di processi con componenti ibridi, in cui una componente è prodotta in modo convenzionale e una seconda componente è stampata. Ciò porta a molte soluzioni perfette per quasi ogni applicazione industriale.
Per quanto riguarda il processo CEM (Composite Extrusion Modelling) e la stampa 3D a granuli con una stampante a materiali multipli, l’utente ha a disposizione una vasta gamma di materiali ad alte prestazioni di stampa. Infine, l’economicità deriva dalla capacità di elaborare granuli polimerici convenzionali invece di filamenti. Le dimensioni, basate su un componente di esempio, sono le seguenti: a) velocità di stampa (esempio PA6 GF30: filamento: 50 mm/s vs. granuli: 500 mm/s cioè circa 10 volte più veloce) e soprattutto b) prezzo del materiale (filamento: 200 EUR/kg vs. granuli: 10 EUR/kg, cioè circa 20 volte più basso costo). Questo spiega il potenziale di risparmio dei costi di un approccio MEX.
La corrente tecnologia di macchine e sistemi nel campo della stampa a granuli 3D garantisce buone prestazioni meccaniche, alta tenuta ai gas e impermeabilità ai media con spessori di parete ridotti e buona isolazione elettrica. Queste proprietà sono state confermate da fornitori di livello 1 nei settori automobilistico e aerospaziale. Pertanto, il segmento di mercato MEX continuerà a crescere a un tasso superiore alla media nel 2023 e oltre.
Quali sono le principali sfide tecniche che il mercato delle stampanti 3D affronta dal punto di vista medio e lungo termine?
La prima e centrale sfida riguarda il tasso di scarto come parte dell’ottimizzazione dei costi. Con l’ampio utilizzo dell’AM nella produzione in serie, i produttori di macchine e impianti dovranno risolvere il fatto che il tasso di scarto del processo AM rispetto a quello dei processi di produzione convenzionali e delle strategie di produzione è ancora relativamente alto. Anche considerando il fatto che i processi di estrusione del materiale e fusione del letto di polvere raggiungono alti tassi di riciclaggio, il riciclaggio delle parti scartate non risolverà davvero questo problema, poiché questo consume tempo di elaborazione ed energia. Per superare questo, la sfida chiave per tutti i processi AM è di stabilizzare i tassi di scarto a ben al di sotto del 2%, questo vale anche nel caso di elevati flussi di produzione. La conseguenza di ciò è che il tasso di scarto di un processo AM deve essere ridotto per corrispondere ai tassi di scarto usuali dei processi convenzionali. I processori dei settori automobilistico e aerospaziale oggi raggiungono tassi di scarto del 2 al 2,5% nel settore dei metalli (MIM) così come nel settore delle materie plastiche. Questo è già molto buono – e si applica anche al confronto con l’iniezione di plastica MIM e altre tecnologie additive. Tuttavia, alla luce dei maggiori costi unitari rispetto all’iniezione di plastica, c’è un grande bisogno di ridurre significativamente questo tasso. La produzione additiva deve competere con le applicazioni convenzionali per diventare più competitiva.
La seconda sfida che il mondo dell’AM deve affrontare è il gran numero di parametri di processo che devono essere continuamente monitorati durante la stampa, soprattutto se si considera il tempo di costruzione delle parti. Le strategie convenzionali, come i test di parte in corso di lavorazione con sensori laser, sono troppo lente per la dinamica del processo di costruzione e non migliorano la loro economicità. Di conseguenza, i fornitori di macchine e impianti devono cambiare il modo in cui vedono il controllo del processo. Gli approcci a questa sfida includono PLC ad alte prestazioni e nuove tecnologie di sensori con le rispettive possibilità. I controlli di processo complessi basati su AI neuronali potrebbero anche essere implementati nelle macchine per controllare le grandi quantità di dati di processo e l’elevato numero di aree di condizione del processo.
Risolvere entrambe le sfide sarà una grande preoccupazione per l’industria dell’AM in futuro. Il grado in cui affronteremo queste sfide determinerà in modo decisivo il potenziale tecnico e la redditività delle strategie di produzione AM.
Per concludere con una domanda dettagliata: perché i sensori laser sono troppo lenti quando la velocità di costruzione richiede già tempo?
La ragione risiede nella risoluzione necessaria e nella “lenta” frequenza di scansione dei sistemi laser, che è di circa 2.000-4.000 Hz. Certamente abbiamo bisogno di alcuni minuti per stampare uno strato, ma il laser impiega molto più tempo. Prendiamo come esempio l’ExAM 510: possiamo assumere una velocità di stampa media di 500 mm/s per grandi componenti. Se viene posizionata una striscia con una larghezza di 0,42 mm, la macchina raggiunge un’accuratezza del componente di 10-50 µm. Supponiamo ora che la media sia di 30 µm, cioè 0,03 mm. Ci vuole un secondo per estrudere una linea lunga 500 mm e larga 0,42 mm. Scansionando 30 µm con un laser a punto, questa striscia avrebbe 500 mm diviso per 0,03 mm, che equivale a 16.666 punti di lunghezza e 0,42 mm diviso per 0,03 mm, che equivale a 14 punti di larghezza. Ciò significa che dovremmo scansionare 16.666 punti x 14 punti, che equivale a 233.324 punti per questa sola striscia. Con una frequenza di scansione di 4.000 Hz, questo richiede 58,331 secondi. In altre parole, la scansione della striscia richiede 58 volte il tempo necessario per stamparla. Il processo di scansione può essere accelerato un po’ con i laser a linea. Tuttavia, fino ad ora, la scansione di solito ha richiesto almeno tanto tempo quanto la stampa e ciò quasi raddoppia i costi del componente.
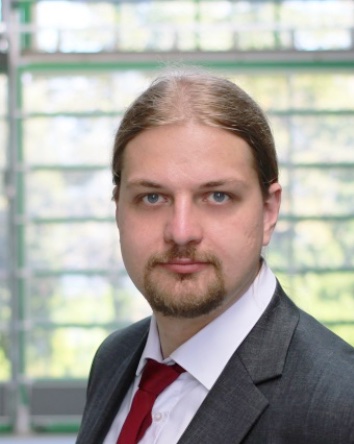