Isar Aerospace ha integrato il software nebumind nel loro processo di stampa 3D (LPBF – Laser Powder Bed Fusion), con l’obiettivo di automatizzare il rilevamento di errori durante la deposizione di nuovi strati di polvere. Questo passo avanti permette all’azienda di risparmiare tempo e ridurre i costi di produzione. Precedentemente, gli ingegneri dovevano esaminare manualmente le immagini del letto di polvere per identificare eventuali anomalie che potessero influenzare la qualità dei componenti. Ora, grazie al software nebumind, l’analisi delle immagini del letto di polvere viene effettuata automaticamente, fornendo ai tecnici dati cruciali per valutare la qualità del processo costruttivo.
Innovazione nel Settore Aerospaziale
Come azienda emergente nel settore aerospaziale, Isar Aerospace si affida a metodi di produzione avanzati, come la stampa 3D basata su letto di polvere, per la realizzazione di componenti complessi di motori a reazione. Uno degli step critici di questo processo è la deposizione del polvere, che avviene dopo ogni strato stampato e che è particolarmente suscettibile a errori. Una copertura irregolare può infatti portare a difetti nei componenti finali.
In precedenza, i sistemi LPBF erano dotati di sensori e telecamere che monitoravano il passaggio di rivestimento, producendo immagini che dovevano essere analizzate manualmente dagli ingegneri per rilevare zone non rivestite, danni allo strumento di rivestimento o altri tipi di errori. Questo metodo era notevolmente dispendioso in termini di tempo: per esempio, se un componente stampato in 3D generava 2.500 immagini di rivestimento e un ingegnere impiegava tre secondi per analizzare ogni immagine, avrebbe dedicato oltre due ore solo per esaminare un singolo lavoro di stampa. Inoltre, gli errori venivano spesso scoperti solo al termine del processo di stampa, dopo che le analisi erano state completate.
Automazione Attraverso nebumind
Per eliminare la necessità di questo processo manuale, Isar Aerospace ha incorporato il software nebumind direttamente nelle loro macchine, automatizzando il riconoscimento degli errori in ogni fase di rivestimento. Il software riceve le immagini del rivestimento, catturate da una camera ottica con risoluzione di 1280×1024 pixel, che vengono estratte automaticamente attraverso un’interfaccia diretta con la macchina. Utilizza algoritmi robusti di riconoscimento di immagini e bordi per identificare gli errori. Inoltre, analizza la posizione degli errori attraverso diversi strati per minimizzare la probabilità di falsi positivi.
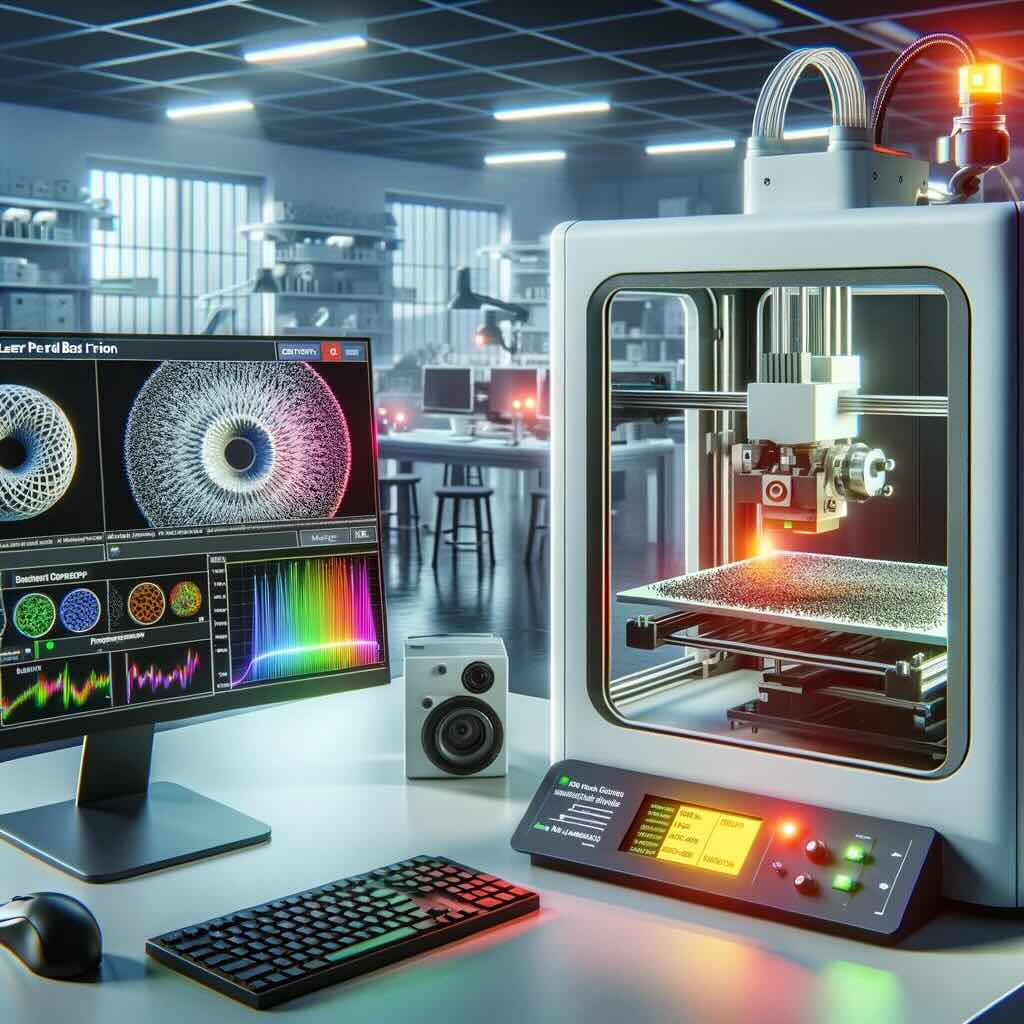