Tessuti plastici modulari fuori dal piatto: la prova di Down2TheShed con una Bambu Lab A1 mini
Un maker su Reddit, Down2TheShed, ha mostrato come ottenere “tessuti” stampati in 3D molto più grandi dell’area utile di una Bambu Lab A1 mini. L’idea ruota attorno a pannelli con bordi disegnati come anelli aperti: il primo job deposita metà giunzione, il pezzo viene riposizionato, il secondo job chiude gli anelli già stampati e salda i moduli tra loro. Il risultato è un tessuto plastico flessibile, estensibile e teoricamente infinito in estensione.
Il principio degli anelli aperti/chiusi
-
Fase 1 – stampa del primo modulo: il bordo esterno contiene “ganci” o anelli incompleti.
-
Fase 2 – riposizionamento: il pannello appena stampato viene centrato sul piatto con una dima (o riferimenti ottici).
-
Fase 3 – stampa del modulo successivo: il secondo file chiude gli anelli del precedente e aggiunge i suoi, pronti a essere chiusi dal terzo, e così via.
Perché funziona
Gli anelli parziali hanno un gioco calibrato: la seconda stampa fonde il nuovo materiale sul bordo del precedente creando una saldatura termica continua. Non serve colla né viti; la precisione della Bambu Lab A1 mini e un flusso costante di PLA da 0,2 mm permettono di “ricucire” i layer come in una catena Jacquard.
Workflow operativo, passo dopo passo
-
Progettazione dei pannelli in CAD: definire la maglia (quadrata, esagonale, romboidale), lo spessore per layer (0,2 mm nel test), il gap tra gli anelli (0,1–0,2 mm è un buon punto di partenza).
-
Suddivisione del tessuto in moduli: ogni STL rappresenta un pannello stampabile sul piatto. I bordi opposti incorporano gli anelli “aperti”.
-
Preparazione della dima di centraggio: può essere un semplice frame stampato che si appoggia ai bordi del piano o una croce di riferimento incisa su un foglio magnetico.
-
Stampa del primo modulo con il profilo standard PLA.
-
Riposizionamento del modulo: aggancia il pannello alla dima, bloccalo con clip a molla o magneti.
-
Stampa del secondo modulo: il G-code è già allineato rispetto allo zero macchina; il slicer deve “ignorare” il pezzo esistente, quindi conviene impostare un’altezza Z iniziale (Z-hop) leggermente superiore per evitare collisioni.
-
Verifica di saldatura: prova a flettere il bordo: se la chiusura degli anelli è completa, non si notano punti deboli.
-
Ripeti per quanti moduli vuoi, alternando direzioni per evitare accumuli termici sempre nello stesso punto.
Strumenti di supporto: dima oggi, slicer domani
-
Dima di centraggio: una guida stampata su misura per il tuo piano. Puoi incorporare magneti o perni di registro.
-
Telecamera del piatto (Bambu Lab, Creality K1, Prusa XL con add‑on): utile per allineare il modulo in overlay sull’anteprima G-code.
-
Macro G-code personalizzate: sequenze che mettono in pausa, spostano la testina, chiedono il posizionamento del pezzo e riprendono la stampa.
-
Funzioni future nel slicer: “stampa modulare continua”, analoga al “tiled printing” dei plotter 2D, con offset automatico e check visivo.
Alternative allineative senza dima
-
Riferimenti incisi sul piano con un primo layer a bassa temperatura, rimosso al termine.
-
Coordinate assolute: se il pezzo ha forme facilmente riconoscibili, puoi usare un comparatore o un righello digitale per allinearlo.
-
Sensori capacitivi/ottici integrati sulla testina per identificare i bordi del modulo precedente.
Stretch, resistenza, comfort: che tessuto è?
Nei test con PLA a doppio layer lo stretch elastico massimo ha raggiunto circa il 35%. La maglia rimane leggera ma non fragile: il doppio layer aiuta la distribuzione dei carichi e riduce la probabilità di rottura degli anelli. Per applicazioni come tappezzeria per camper, pannelli ombreggianti, paratie ripiegabili, questa elasticità è sufficiente; per indumenti tecnici servirebbero polimeri più duttili (TPU, TPEE) e pattern più fitti.
Materiali e parametri consigliati
-
PLA: facile da stampare, salda bene tra job, resistente a trazione limitata.
-
PETG: più tenace, richiede attenzione per evitare “stringing” durante la chiusura degli anelli.
-
TPU: apre scenari per veri tessuti elastici, ma complica il riposizionamento (il pannello si deforma).
-
Ugello 0,4 mm e altezza layer 0,2 mm funzionano per la maggior parte dei pattern; per maglie sottili si può scendere a 0,12 mm.
-
Ventola al 100% nella seconda stampa: aiuta a solidificare rapidamente il ponte sugli anelli precedenti, riducendo il rischio di “sblobbature”.
Confronto con le belt-printer
Le stampanti a nastro (Creality CR-30, iFactory3D, Sainsmart Infinimaker) offrono stampa teoricamente infinita lungo un asse, ma richiedono angoli di 45° e gestione diversa del supporto. L’approccio a moduli saldati:
-
si adatta a qualsiasi macchina a letto fisso;
-
elimina vincoli geometrici legati all’inclinazione dell’asse Z;
-
può essere automatizzato con pick-and-place che depositano il modulo e riavviano il job successivo.
Automazione possibile: pick-and-place al posto del belt
Una testina secondaria o un braccio collaborativo può:
-
prelevare il pannello finito,
-
posizionarlo sulla zona di chiusura,
-
confermare l’allineamento via visione artificiale,
-
far ripartire la stampa.
In fabbrica, aziende come Bambu Lab, Prusa Research, Creality e Raise3D potrebbero integrare questi flussi in futuro, soprattutto se MakerWorld (o piattaforme analoghe) permetteranno di caricare pacchetti “modulo + macro”.
Applicazioni realistiche
-
Tappezzerie e pannelli decorativi per veicoli ricreazionali e imbarcazioni.
-
Vele da ombreggiatura pieghevoli, gazebo modulari, pareti flessibili.
-
Supporti morbidi per robotica soft, cover per sensori, fasce tecniche.
-
Prototipi di abbigliamento tecnico (con TPU) per test ergonomici rapidi.
-
Filtri e separatori: cambiando pattern e materiale si possono ottenere strutture permeabili controllate.
Limiti e punti critici
-
Precisione di allineamento: pochi decimi di millimetro di errore possono compromettere la chiusura degli anelli.
-
Accumulo di errori: più moduli si concatenano, più è necessario un riferimento globale.
-
Deformazioni termiche: materiali flessibili tendono a imbarcarsi durante il riposizionamento.
-
Tempo di preparazione: la dima va pensata, stampata e testata.
MakerWorld e comunità
Down2TheShed segnala MakerWorld per file di prova. Vale la pena pubblicare varianti di pattern, macro di pausa/ripresa, dime parametriche. La community può contribuire inviando feedback su tolleranze, gap e strategie di allineamento, creando un kit open-source replicabile su qualsiasi FDM.
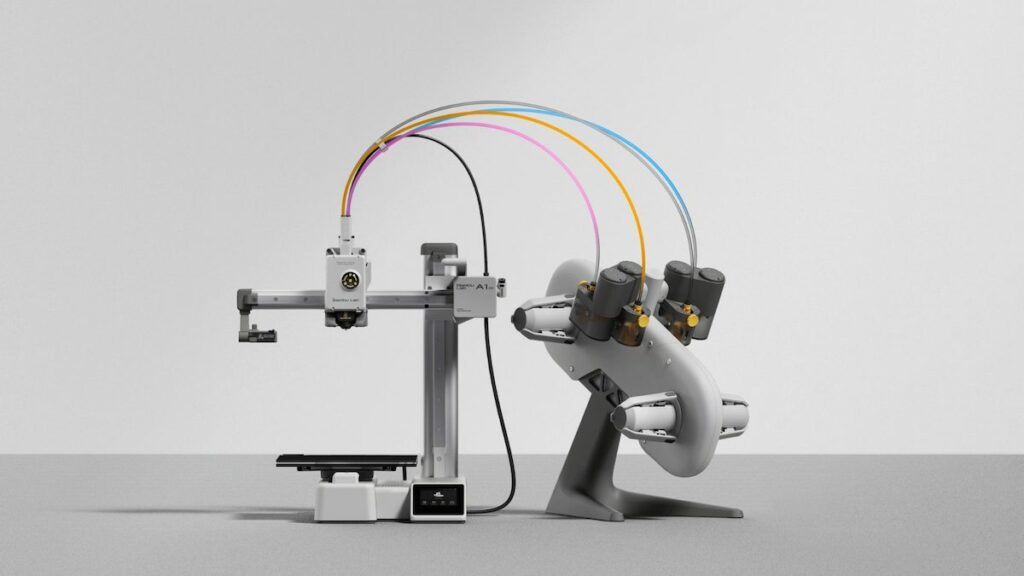