Phase3D, azienda statunitense attiva nello sviluppo di tecnologie per il monitoraggio avanzato nei processi di produzione additiva, ha messo a punto un nuovo sistema di ispezione specificamente progettato per la tecnologia a spruzzo a freddo. Il sistema prende il nome di Fringe Inspection Cold Spray ed è stato sviluppato nell’ambito di una collaborazione con l’Air Force Research Laboratory (AFRL), grazie a un finanziamento pari a 1,25 milioni di dollari previsto dal programma STTR (Small Business Technology Transfer) di Fase II.
L’obiettivo del progetto è stato chiaro sin dall’inizio: migliorare in modo significativo il controllo qualità nei processi di riparazione e produzione aerospaziale, introducendo un sistema in grado di verificare in tempo reale l’integrità degli strati applicati durante la stampa additiva a spruzzo a freddo.
Il contesto: cos’è la stampa 3D a spruzzo a freddo
Il processo noto come Cold Spray Additive Manufacturing (CSAM) si basa sull’applicazione di particelle metalliche accelerate ad alta velocità su una superficie. Le particelle non vengono fuse, ma si deformano plasticamente al contatto con il substrato, legandosi per effetto meccanico. Questa tecnica è impiegata soprattutto per la manutenzione e il ripristino di componenti metallici, in particolare in ambito difesa e aerospazio, dove è fondamentale preservare le proprietà meccaniche originarie delle parti.
Uno dei limiti di questo processo, fino ad oggi, è sempre stato la difficoltà di applicare metodi di controllo qualità non distruttivi in tempo reale. La verifica dei difetti veniva spesso effettuata solo a lavorazione ultimata, con un margine di errore che poteva comportare scarti, rilavorazioni o problemi di affidabilità nel lungo termine.
Un sistema ottico per la verifica immediata degli strati applicati
La proposta di Phase3D si concentra sull’uso della luce strutturata per monitorare in modo continuo e preciso la qualità della superficie durante l’applicazione dello spray metallico. Il sistema utilizza sensori ottici per acquisire dati tridimensionali ad alta risoluzione sugli strati appena applicati, rilevando in modo istantaneo variazioni geometriche, crepe, imperfezioni superficiali o accumuli irregolari di materiale.
I dati ottenuti vengono elaborati in tempo reale e possono essere utilizzati per modificare dinamicamente i parametri del processo di stampa, garantendo che ciascun strato sia conforme alle specifiche. Questa capacità di adattamento immediato rappresenta un importante passo avanti nella gestione dei processi additivi critici, soprattutto in ambienti dove precisione e affidabilità sono imprescindibili.
Sviluppo del progetto e test in ambiente operativo
La parte hardware del sistema è stata realizzata in collaborazione con l’University of Dayton Research Institute (UDRI), mentre la validazione sul campo è stata condotta presso la base aeronautica di Ellsworth, in un ambiente prossimo alle reali condizioni operative.
Durante le fasi di collaudo, il sistema è stato sottoposto a test ciechi: i componenti campione sono stati prodotti senza che il personale a valle conoscesse la presenza o l’assenza di difetti, e il sistema è stato in grado di identificare correttamente le criticità presenti secondo parametri oggettivi. Questo risultato ha confermato l’affidabilità e l’efficacia dell’approccio basato su luce strutturata.
Benefici attesi per l’aeronautica e oltre
Secondo Niall O’Dowd, fondatore e CEO di Phase3D, il completamento del progetto e l’installazione operativa presso la base di Ellsworth rappresentano una conferma dell’utilità concreta di questa tecnologia nei contesti produttivi avanzati. Il sistema permette di ottenere riparazioni più accurate, riducendo al tempo stesso costi e tempi legati a rilavorazioni o scarti. Inoltre, la possibilità di integrare il controllo qualità direttamente nel flusso produttivo aiuta a rendere più stabile e prevedibile l’intero processo.
Espansione futura e prospettive industriali
Dopo aver dimostrato l’efficacia della tecnologia in ambito militare, Phase3D è ora orientata verso un’espansione delle applicazioni nel settore industriale. L’azienda sta attivamente cercando nuovi partner per validare il sistema in ambienti produttivi civili, nei settori dove la qualità dei rivestimenti o delle riparazioni superficiali è un fattore determinante – come l’energia, il trasporto, la manifattura meccanica o l’oil & gas.
L’obiettivo a lungo termine è quello di rendere l’ispezione tramite luce strutturata uno standard per tutte le applicazioni di stampa 3D a elevato contenuto tecnico, con particolare attenzione ai processi di riparazione e ricondizionamento dove la tolleranza ai difetti è minima.
Una nuova fase per il controllo qualità nella stampa additiva
La proposta di Phase3D dimostra come sia possibile integrare sistemi intelligenti di ispezione direttamente nei processi produttivi senza rallentare i cicli operativi. La capacità di rilevare difetti in tempo reale e adattare i parametri di stampa rappresenta un passo decisivo verso una manifattura additiva più affidabile e sostenibile, capace di coniugare precisione, efficienza e controllo.
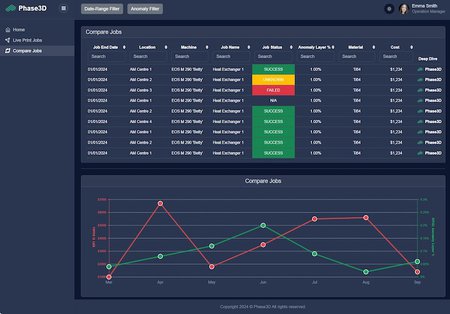