Il nuovo sistema AM garantisce la prima volta le build corrette mediante “annullamento” in-situ dei livelli di errore
Nonostante i numerosi progressi della tecnologia Laser Powder Bed Fusion negli ultimi anni, comprese le funzionalità multi-laser e persino le build senza supporto, la fusione del letto di polvere è rimasta limitata da alcuni fattori, ovvero la coerenza. In effetti, parlando a molte persone in tutto il settore, la coerenza e l’affidabilità sono due punti critici che continuano a rappresentare ostacoli alla piena industrializzazione dell’AM.
Fortunatamente, il problema della coerenza e delle impeccabili parti stampate in 3D viene affrontato in tutto il settore, sia dalle aziende metal AM che dai ricercatori che spingono al limite. In quest’ultima categoria, i professori Bianca Maria Colosimo e Marco Grasso del Dipartimento di Ingegneria Meccanica del Politecnico di Milano hanno appena presentato una nuova e avvincente tecnologia che non solo può identificare le incoerenze nel processo LPBF ma anche risolverle durante la stampa.
Un brevetto per il processo di monitoraggio in situ è stato recentemente depositato (è attualmente in attesa di brevetto), rendendolo oggi una delle innovazioni più promettenti e all’avanguardia per la fusione laser a letto AM. Il sistema, un “prototipo LPBF ad architettura aperta altamente sensorizzato con sistema di rimozione integrato”, si chiama PENELOPE. Il sistema prende il nome dalla moglie di Odisseo nella mitologia greca, che divenne un simbolo di fedeltà: per evitare le avances dei suoi corteggiatori, promise che avrebbe scelto uno di loro per sposarsi quando finì di tessere un sudario funebre. Tuttavia, ogni notte, avrebbe sbrogliato il pezzo in modo molto simile al sistema PENELOPE AM che avrebbe “annullato” un livello stampato.
La tecnologia di monitoraggio in-situ sviluppata dal Prof. Colosimo e Grasso può essere suddivisa in tre aree distinte: metrologia della qualità in situ, termografia in situ e correzione dei difetti in situ. Nel loro insieme, i tre elementi costituiscono una soluzione potenzialmente rivoluzionaria per garantire la produzione di parti impeccabili e coerenti utilizzando la produzione additiva LPBF. Mentre il sistema descritto di seguito è abbastanza complesso, uno dei risultati più impressionanti finora è che il team ha dimostrato che la correzione del difetto in loco non altera affatto la qualità finale della parte.
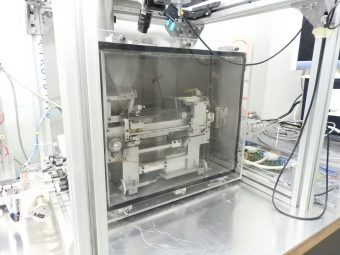
Metrologia in-situ
PENELOPE Politecnico di Milano
Nel processo LPBF, ci sono molti modi in cui possono verificarsi difetti, tra cui deviazioni nel piano e deviazioni fuori piano. Per i produttori industriali, non è fattibile dedicare tempo e risorse alla stampa di una parte metallica, solo per far sì che si verifichi un difetto a metà strada. La metrologia in-situ, quindi, è il primo passo per identificare se e quando si verifica un errore di processo.
La metrologia della qualità in loco proposta dal team di ricerca italiano comprende il primo passo nell’innovativo sistema PENELOPE. È costituito da un dispositivo di imaging ad alta risoluzione, con immagini pre- / post-esposizione e capacità di 20 μm / pixel, nonché un sistema di illuminazione riconfigurabile, montato sulla camera di costruzione della stampante.
In breve, il sistema metrologico in-situ offre il rilevamento in linea di distorsioni geometriche catturando immagini ad alta risoluzione della stampa in diverse condizioni di illuminazione. Ciò consente al sistema di rilevare i contorni utilizzando la segmentazione delle immagini basata sul livello. Il sistema di imaging cattura anche le misurazioni dimensionali della geometria di una determinata parte, il che significa che può identificare anche inconsistenze minime nei livelli della stampante. Infine, Penelope è in grado di stimare l’errore di misurazione e la variabilità della stampante da una build all’altra.
Termografia in situ
Il secondo elemento critico nel processo di monitoraggio in-situ brevettato è la termografia, che si basa su un sistema di termografia ad alta velocità per mappare e monitorare termicamente fenomeni di raffreddamento transitori e veloci, compresi spruzzi e pennacchio. Il sistema in questione è una termocamera ad infrarossi con onda centrale da 3-5 μm (MWIR) con 1000 fps @ 200 μm / pixel e calibrazione fino a 1500 ° C.
PENELOPE Politecnico di Milano
In breve, lo scopo del sistema di termografia in situ è quello di catturare la stima in linea della microstruttura della parte usando l’imaging video. Ciò è ottenuto attraverso l’analisi e la modellizzazione a livello di strati dei gradienti di raffreddamento spaziale e temporale all’interno della regione scansionata e attraverso la stima degli indicatori di morfologia del grano microstrutturale, come i grani colonnari oi grani equivoci.
Secondo i ricercatori, c’è ancora lavoro da fare per migliorare la stima della microstruttura in linea. Tra le prossime fasi della ricerca, si sta migliorando la calibrazione della telecamera IR, che è “difficile o addirittura impossibile a causa del coefficiente di emissività della variazione della temperatura e della variazione di fase del materiale durante il processo LPBF”; validare ulteriormente la metodologia effettuando test con proprietà microstrutturali differenti; e monitorare i profili di raffreddamento termico per stabilizzare il processo.
Correzione dei difetti in-situ
La parte finale della tecnologia PENELOPE di Colosimo e Grasso, in attesa di brevetto, si ispira alla possibilità di disporre di un sistema LPBF in grado di rilevare autonomamente i difetti utilizzando la tecnologia di monitoraggio in-situ e di rimuovere lo strato difettoso, risultando in parti impeccabili.
PENELOPE Politecnico di Milano
Forse la parte più convincente della soluzione di monitoraggio in-situ, la funzione di correzione dei difetti integra funzionalità di invio, monitoraggio e produzione ibrida in-situ, che consentono efficacemente al sistema di rettificare la superficie di una parte, cancellando i più recenti strati stampati.
Questa nuova tecnica potrebbe consentire ai sistemi LPBF di identificare i difetti mentre si verificano, eliminarli rimuovendo gli strati difettosi, regolare di conseguenza i parametri di processo e riprendere il lavoro di stampa.
Il sistema ideato per rimuovere lo strato (o gli strati) difettoso è costituito da una mola di superficie installata in un carrello di macinazione montato su un asse lineare, parallelo all’asse Y. Il componente ruota è una ruota abrasiva Borazon con una granulometria media di 120 μm, una velocità massima di 4.000 giri / min, un’alimentazione massima di 30 mm / se una profondità di taglio di 10-20 μm.
I ricercatori hanno preso in considerazione molte domande di fattibilità per il processo di rimozione dello strato difettoso, compreso se è possibile ripristinare un letto di polvere incontaminato e uniforme dopo che la mola rimuove gli strati superiori di una parte e se la rimozione dello strato influisce sulla meccanica generale esecuzione della parte in questione.
PENELOPE Politecnico di Milano
Nei test, tuttavia, il prototipo del sistema PENELOPE ha dimostrato che era effettivamente possibile utilizzare lo strumento di macinazione e mantenere comunque un letto di polvere non contaminato e omogeneo . Ulteriori test – scansioni TC di campioni stampati – hanno mostrato che non vi era alcuna differenza statistica nella densità delle parti tra una parte che aveva rimosso uno strato e una che non lo aveva. Allo stesso modo, non è stata trovata alcuna concentrazione anomala di pori.
Penelope 2.0
In questa fase, i ricercatori continueranno a sviluppare e far avanzare il nuovo processo LPBF con funzionalità di monitoraggio e correzione in situ. Le fasi future del progetto di ricerca innovativa riguarderanno la caratterizzazione delle prestazioni meccaniche, l’analisi microstrutturale aggiuntiva, le indagini sugli effetti dell’ossidazione e altro ancora. Dopo aver affrontato questi problemi, i ricercatori intendono introdurre PENELOPE 2.0, un “controller completamente integrato per il rilevamento e la correzione di difetti autonomi”.