Il mese scorso, Tangible Solutions , con sede a Fairborn, Ohio , fondata nel 2013 e che produce impianti ortopedici in titanio stampati in 3D, ha annunciato che stava espandendo il suo portafoglio di apparecchiature di post-elaborazione e il suo personale di ingegneria e post-elaborazione, al fine di incontrare e coprire la crescente domanda di produzione AM a causa della pandemia di COVID-19. L’azienda certificata ISO 13485:2016 e registrata dalla FDA 3014273501 gestisce ogni aspetto della creazione dei suoi impianti ortopedici, dal supporto alla progettazione, prototipazione e autorizzazione 510(k) alla stampa 3D, post-elaborazione e finitura e test sia durante che dopo la produzione , ed è lieta di poter offrire la post-elaborazione internamente presso la propria struttura.
Tangible Solutions si impegna a garantire alta qualità, reattività e coinvolgimento dei clienti e consegne puntuali. Portando la post-elaborazione in loco, l’azienda sarà in grado di assicurarsi che i suoi impianti stampati in 3D siano efficienti in termini di costi, con una buona qualità e consegnabilità ai clienti nel campo ortopedico.
“Il costo in tempo e denaro coinvolti nelle fasi di post-elaborazione può variare notevolmente; e se questi processi vengono esternalizzati per un progetto di produzione, i costi possono essere anche più alti. Un produttore a contratto che gestisce un progetto di produzione additiva dall’inizio alla fine all’interno della propria struttura può far risparmiare tempo e costi importanti al cliente quando introduce un impianto sul mercato”, ha affermato Adam Clark, CEO di Tangible Solutions, in un comunicato stampa.
Clark ha affermato in passato che il modello di business dell’azienda è focalizzato al 100% su impianti ortopedici in titanio stampati in 3D e che il flusso di lavoro AM, il processo di invio alla FDA e la post-elaborazione sono tutti gestiti internamente, poiché i dipendenti comprendono l’importanza di cosa stanno creando e sanno come supportare al meglio i clienti. I dispositivi medici come gli impianti devono essere biocompatibili, estremamente puliti e molto lisci; secondo un recente studio di Fraunhofer IAPT , “le parti metalliche stampate in 3D spesso non soddisfano i requisiti di qualità della superficie”, il che rende la finitura di fondamentale importanza in questo settore. È anche importante ottenere ripetibilità e tracciabilità , poiché il campo medico ha standard estremamente elevati in termini diregolamenti sui materiali e sui dispositivi .
La rimozione della polvere residua può essere complicata e Tangible ha sviluppato un processo di finitura proprietario per garantire che i prodotti siano assolutamente privi di qualsiasi contaminante. La finitura crea parti dall’aspetto superbo, fino al livello microscopico.
Tangible Solutions afferma che ora è pienamente in grado di fornire tutte le necessarie fasi di post-elaborazione per i suoi impianti ortopedici in titanio stampati in 3D, che includono la passivazione (rendendo un materiale non reattivo) e la marcatura laser. Spesso utilizzato in combinazione con la passivazione per supportare i requisiti ASTM F86, la marcatura è richiesta dall’industria dei dispositivi medici, poiché prodotti come gli impianti devono resistere in una varietà di ambienti per tutta la loro vita.
“L’aggiunta della marcatura laser e della passivazione all’elenco dei servizi di Tangible completa quasi il nostro viaggio per diventare un produttore a contratto completo end-to-end di impianti ortopedici in titanio stampati in 3D. Continuiamo a impegnarci per zero servizi esterni a un ritmo rapido”, ha spiegato il COO di Tangible Solutions Chris Collins.
“Tangible produce esclusivamente impianti tramite stampa 3d in titanio (Ti-6Al-4V ELI). Durante tutto il flusso del processo di produzione, questi impianti entrano in contatto con vari materiali di produzione e contaminanti superficiali che vengono rimossi tramite passivazione, nonché con il nostro processo di finitura proprietario, che è vitale per creare una marcatura leggibile e durevole.
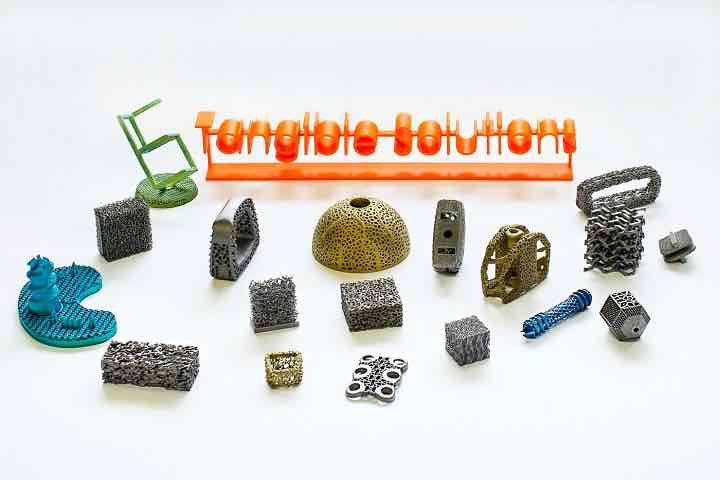