Partire per la terza dimensione
I componenti metallici sofisticati possono essere stampati in 3D in modo produttivo e riproducibile in serie? I ricercatori di Aquisgrana possono rispondere affermativamente a questa domanda: al Fraunhofer Institute for Laser Technology ILT, hanno trasferito l’EHLA bidimensionale Extreme High-speed Laser Material Deposition a un sistema CNC a cinque assi modificato per la produzione additiva di componenti complessi. Estendendo il processo EHLA alla terza dimensione, l’istituto può stampare in 3D materiali difficili da saldare come acciai per utensili, titanio, alluminio e leghe a base di nichel.
EHLA è in grado di spostare gli utensili in modo rapido, altamente dinamico e preciso in direzione laterale. Con una tavola rotante e inclinabile, è adatto non solo per la produzione additiva, ma anche per rivestimenti superficiali a forma libera.
Per decenni, due processi laser hanno dominato la stampa e il rivestimento di componenti metallici. La tecnologia dominante nella stampa 3D metallica industriale diretta è il processo di fusione a letto di polvere basato su laser (LPBF) brevettato da Fraunhofer ILT 26 anni fa. Qui, la radiazione laser scioglie una piccola parte del materiale di base e converte la polvere in uno strato solido che aderisce metallurgicamente al materiale di base. In questo modo, un componente 3D cresce strato dopo strato dal letto di polvere.
Anche la Laser Material Deposition (LMD) si è dimostrata una tecnologia di superficie efficiente di tipo speciale. In LMD, sulla superficie del componente si forma una pozza fusa, nella quale viene continuamente introdotto il materiale di riempimento, filo o polvere. Questo pool fonde sia il substrato che il materiale di riempimento, determinando un legame metallurgico tra lo strato e il substrato del componente.
Recupero di componenti costosi
Il potenziale economico risiede, da un lato, nella possibilità di aggiornare i componenti di base con uno strato funzionale o di apportare modifiche locali e aggiuntive ai componenti. La seconda importante area di applicazione dell’LMD è la riparazione, vale a dire il recupero di componenti costosi, ad esempio dall’industria aerospaziale o dalla costruzione di utensili. I componenti usurati o difettosi possono essere resi completamente funzionali dopo il rivestimento locale utilizzando LMD e, quindi, non devono più essere rottamati.
LMD e LPBF sono diventati indispensabili per la produzione additiva a base di metallo poiché presentano vantaggi specifici del processo: LMD è attraente grazie alla sua elevata produttività mentre LPBF può essere utilizzato per la stampa 3D di componenti estremamente filigranati e complessi. Fraunhofer ILT e la cattedra per la produzione additiva digitale DAP presso la RWTH Aachen University hanno aperto una strada completamente nuova nel 2012 con lo sviluppo di Extreme High-speed Laser Material Deposition EHLA. Nel processo brevettato, un laser fonde le particelle di polvere già al di sopra del bagno di fusione. Grazie a questa innovazione, è stato possibile aumentare la velocità di processo dai precedenti 0,5 a 2,0 (LMD) fino a 200 m/min e ridurre lo spessore del rivestimento da 500 fino a 10 µm. Ora è possibile rivestire fino a cinque metri quadrati all’ora. Inoltre, i rivestimenti sono diventati più lisci,
Successi internazionali nel rivestimento rapido
L’invenzione ha preso piede: Hornet Laser Cladding BV di Lexmond (Paesi Bassi), ad esempio, ha integrato una sorgente di raggio laser, una testa di lavorazione EHLA e un sistema di alimentazione della polvere nei suoi torni per utilizzare EHLA nei processi industriali. Anche TRUMPF Laser- und Systemtechnik GmbH, con sede a Ditzingen, in Germania, ha incluso il processo nel suo portafoglio di prodotti e offre apparecchiature laser e tecnologie di sistema per il processo EHLA. Tra i primi utenti ci sono aziende nei Paesi Bassi, Cina, Germania e Turchia. La svolta è arrivata nel 2015 per il settore offshore: da allora, molte centinaia di cilindri idraulici lunghi sono stati rivestiti con leghe resistenti all’usura e alla corrosione per l’uso in tutto il mondo in ambienti marittimi.
Nel 2019 è seguito il passaggio alla terza dimensione, dopo ulteriori successi nel rivestimento rapido e affidabile di dischi freno, pistoni, cilindri e cuscinetti. Jonathan Schaible, ex ricercatore associato presso Fraunhofer ILT, ha partecipato all’ulteriore sviluppo nell’ambito del suo dottorato: ha affrontato la questione di quali requisiti speciali per la tecnologia delle macchine e dei sistemi devono essere soddisfatti per combinare EHLA con la stampa 3D ad alta velocità. Parallelamente, il suo successore, Min-Uh Ko, ha continuato a perfezionare l’ingegneria di processo su un sistema CNC a cinque assi appositamente modificato che unisce la massima precisione con elevate velocità di avanzamento per la produzione additiva, il rivestimento a forma libera e la riparazione di componenti utilizzando EHLA.
“EHLA 3D combina la produttività di LMD con i suoi strati spessi da 500 a 2000 µm con l’accumulo strutturalmente mirato e preciso di LPBF con strati spessi da 30 a 100 µm”, spiega Min-Uh Ko, capogruppo di Additive Manufacturing and Repair LMD presso l’Istituto Fraunhofer per la tecnologia laser ILT. “EHLA 3D è nella fascia media con 50-300 µm.”
Vicino al contorno finale
Anche la zona a bassa diluizione e l’elevata velocità di raffreddamento parlano a favore del processo. Grazie a queste proprietà, è possibile produrre in modo additivo anche componenti realizzati con materiali difficili da saldare e accoppiamenti multimateriale. Il processo mostra i suoi punti di forza nella stampa 3D reale. Lo scienziato Ko spiega: “Con EHLA 3D, è possibile produrre in modo produttivo componenti che si avvicinano già molto al contorno finale. Oltre al cosiddetto near-net shaping, il processo consente anche di costruire in modo rapido e preciso, nonché di applicare rivestimenti su superfici a forma libera.
Forme complesse in tempi record – Questo è possibile solo con una tecnologia della macchina adeguatamente progettata e una pianificazione del percorso adattata dei programmi CNC. La produttività affonda o nuota qui poiché il cosiddetto fly-in – quando la testa laser accelera fino al punto di utilizzo con il raggio laser acceso – interagisce con il successivo fly-out – quando decelera fuori dalla zona di lavorazione. L’efficienza risulta dal rapporto tra il tempo di lavorazione con il raggio laser acceso e il tempo totale di lavorazione. Le indagini di Schaible lo dimostrano: con un’accelerazione di 50 m/s² e una velocità di avanzamento di 50 m/min per una distanza di 100 mm, l’efficienza M-PDE (efficienza di deposizione della polvere correlata alla macchina) è di circa l’80%. Con un’accelerazione di 10 m/s², la M-PDE è di ca. 40 percento.
Lo sforzo dell’istituto per sviluppare ulteriormente il processo EHLA ha dato i suoi frutti, come dimostrato dalle prime dimostrazioni riuscite. All'”AKL’22 – International Laser Technology Congress” ad Aquisgrana, in Germania, lo scienziato Ko ha mostrato gli attuali progressi della tecnologia EHLA 3D durante la sua presentazione nella primavera del 2022. Ad esempio, un video ha dimostrato la produzione produttiva e additiva di uno strumento di formatura il cui tempo di stampa potrebbe essere ridotto di un fattore due rispetto a LMD. Inoltre, ulteriori vantaggi derivano dalla riduzione dello sforzo richiesto per le lavorazioni di finitura.
Stampa in metallo 3D affidabile con polvere usata
Il processo è anche caratterizzato da un’elevata efficienza: i componenti realizzati con il materiale aerospaziale Inconel 718 sono stati stampati in 3D sul sistema CNC a cinque assi a una velocità di deposizione di oltre 2 kg/h con una densità superiore al 99,5%. I ricercatori di Aquisgrana hanno anche studiato come cambiano i valori caratteristici quando lavorano con polvere di metallo riciclata anziché nuova. In entrambi i casi, la resistenza alla trazione R mera di circa 1300 MPa. Ko spiega: “In entrambi i casi la resistenza alla trazione si è rivelata buona come con la fusione”. Buoni risultati sono stati ottenuti anche dallo scienziato Schaible, il cui lavoro includeva lo sviluppo del processo EHLA 3D di componenti realizzati in acciaio inossidabile 316L e leghe di alluminio-silicio. Anche qui le proprietà meccaniche ottenute sono in linea con quelle riportate in letteratura per campioni prodotti convenzionalmente. La risoluzione strutturale attualmente possibile dei componenti in alluminio a parete sottile prodotti utilizzando EHLA 3D è di circa 500 µm.
Il sistema CNC situato presso Fraunhofer ILT è un prototipo appositamente adattato in grado di muovere l’utensile in modo affidabile, preciso e allo stesso tempo altamente dinamico. Ko invita le parti interessate a guardare un po’ più da vicino: “Se sei interessato a questa tecnologia di impianto o ad altri possibili usi per il processo EHLA 3D, sarò felice di aiutarti qui al Fraunhofer ILT”.
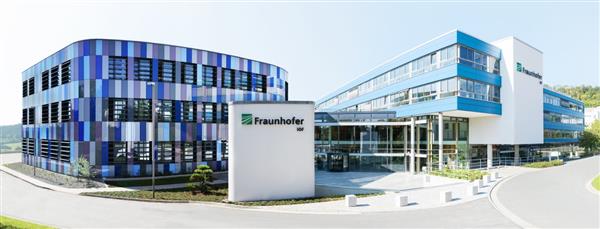