Nuova Frontiera nella Stampa 3D: Tecnologia Fotopolimerizzabile per Strutture Tubolari Multimateriale
Una recente innovazione nel campo della stampa 3D, sviluppata dai ricercatori dell’Università di Beihang, ha permesso di realizzare strutture tubolari multimateriale con spessori di parete minimi di 50 micrometri e dimensioni fino a 10 micrometri. Questa tecnologia, presentata sull’International Journal of Extreme Manufacturing, potrebbe trasformare la produzione di innesti tubolari e di componenti tubolari in settori quali odontoiatria e aerospaziale.
Sfide e Soluzioni nella Produzione di Strutture Complesse
La creazione di geometrie radialmente complesse e multimateriali, come i vasi tissutali e gli innesti tubolari, rappresenta una sfida significativa, specialmente senza l’uso di strutture di supporto. Jiebo Li, professore alla Scuola di Scienze Biologiche e Ingegneria Medica dell’Università di Beihang e autore principale dello studio, evidenzia le difficoltà incontrate con i sistemi di coordinate cartesiane tradizionali. “Le strutture tubolari ultrasottili lisce sono comuni nell’ingegneria biomedica”, afferma Li, “ma è difficile produrle con i metodi convenzionali.”
Per superare questi ostacoli, i ricercatori hanno proposto una soluzione innovativa: l’adozione di un sistema di coordinate polari, che si adatta meglio alle forme tubolari attraverso fasi di rotazione e retrazione, facilitando così la produzione.
La Tecnologia PLLP: Una Svolta nel Settore
L’approccio adottato sfrutta la tecnologia PLLP (Polar-coordinate Line-projection Light-curing Production), che utilizza un mandrino rotante come substrato per la creazione di strutture polimeriche solidificate attraverso l’illuminazione a luce modellata. Questo metodo si distingue per la sua capacità di generare strutture tubolari multimateriale a pareti sottili, superando i limiti delle tecniche tradizionali basate su coordinate cartesiane.
Vantaggi e Applicazioni Future
Il professor Li sottolinea i principali benefici della tecnologia PLLP: “Il più grande vantaggio è la capacità di fabbricare rapidamente strutture tubolari multimateriali con superficie liscia”. Questo rende la tecnologia particolarmente adatta per la personalizzazione rapida di innesti tubolari e per la fabbricazione di componenti tubolari in vari campi.
Gli esperimenti e le simulazioni hanno confermato i vantaggi della PLLP rispetto ai metodi di stampa 3D convenzionali, e hanno dimostrato la fattibilità della stampa di materiali idrogel, ampliando ulteriormente le potenziali applicazioni della tecnologia.
Prospettive di Ricerca e Sviluppo
I ricercatori sono impegnati nel continuo sviluppo di questa tecnologia, con l’obiettivo di migliorare ulteriormente la velocità di formazione e la risoluzione. Le future applicazioni della PLLP potrebbero estendersi a una vasta gamma di settori, promettendo significativi progressi in odontoiatria, aerospaziale e oltre, offrendo vantaggi sia ecologici che economici.
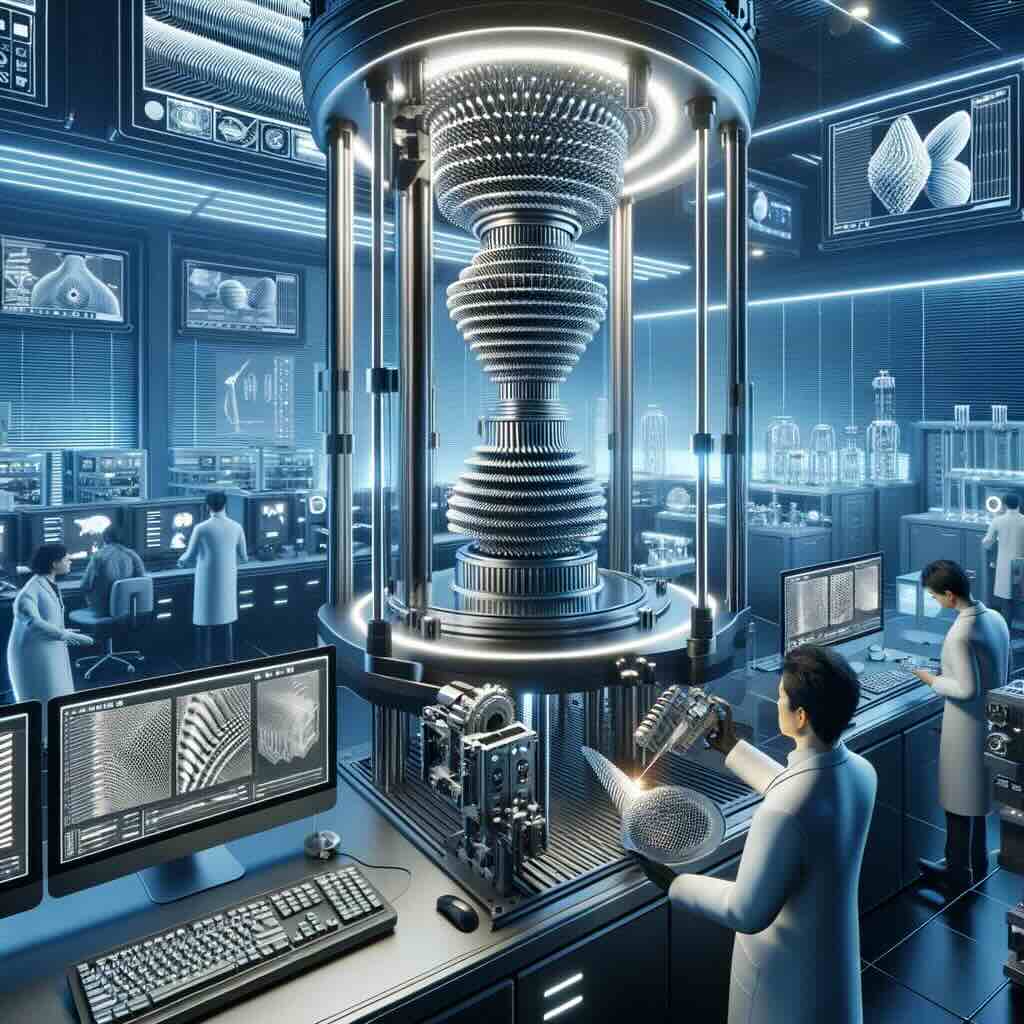