Produzione satellitare migliorata con le tecnologie di manifattura additiva di INTAMSYS
L’agenzia spaziale governativa francese, il Centro Nazionale di Studi Spaziali (CNES), sta utilizzando le tecnologie di manifattura additiva (AM) di INTAMSYS per migliorare le proprie capacità tecnologiche nello spazio.
Il dipartimento Realizzazione e Integrazione (RI) del CNES si specializza nell’assemblaggio e nel collaudo di satelliti, oltre a sviluppare strumenti e mezzi per facilitare queste operazioni nelle camere bianche del CNES prima del lancio (ad esempio, telai di integrazione, carrelli multiuso, dispositivi di sollevamento, ecc.). Queste camere bianche mantengono condizioni precise per garantire un ambiente stabile per i componenti dei satelliti.
Facilità d’uso e qualità di stampa
“L’impressionante facilità d’uso e l’alta qualità di stampa delle stampanti 3D di INTAMSYS hanno contribuito notevolmente al nostro flusso di lavoro, rispondendo perfettamente alle nostre sfide. Ora possiamo utilizzare l’intera gamma di materiali INTAMSYS con una funzionalità click-and-print. Inoltre, CADvision, partner di INTAMSYS, è altamente reattivo e fornisce un ottimo supporto locale, consentendo uno sviluppo congiunto per migliorare sia la macchina che il software, aumentando ulteriormente l’efficienza e il flusso di lavoro”, ha dichiarato Theodore Froissart, responsabile dell’integrazione meccanica presso il Centro Nazionale di Studi Spaziali.
Fondato nel 1961, il CNES conduce ricerche, progetta e gestisce missioni spaziali e promuove lo sviluppo di tecnologie spaziali in Europa e a livello internazionale.
Stampa 3D per una produzione più veloce degli strumenti satellitari
Per produrre strumenti come telai di integrazione e carrelli multiuso, il CNES ha adottato sempre più il metodo di stampa 3D FFF (Fused Filament Fabrication) con materiali polimerici innovativi. Partito inizialmente con una stampante monomateriale nel 2014, il laboratorio di manifattura additiva del CNES si è rapidamente evoluto a causa dell’alta domanda e del numero crescente di parti da produrre.
La stampante INTAMSYS FUNMAT PRO 610HT è stata la prima ad essere integrata negli studi spaziali del CNES, seguita successivamente dalla FUNMAT PRO 410 per completare la gamma di stampanti presenti nel laboratorio.
Prima di integrare la manifattura additiva, il CNES ha affrontato numerose sfide con i metodi di produzione tradizionali, in particolare la qualifica dei materiali per l’uso nelle camere bianche e per il collaudo dei satelliti. Inoltre, i lunghi cicli di progettazione e produzione richiesti per realizzare uno strumento stavano incidendo sull’efficienza complessiva. Utilizzando la stampa 3D, il CNES è ora in grado di snellire questo processo a un singolo giorno, consentendo la prototipazione rapida e l’iterazione dei progetti, facilitando così il collaudo e l’assemblaggio dei satelliti.
Nuove applicazioni per il collaudo dei satelliti
Le applicazioni sviluppate dal CNES sono varie e spaziano da semplici strumenti per le camere bianche a complessi strumenti strutturali per il collaudo dei satelliti, inclusi i test di cicli termici, shock e vibrazioni prima del lancio. Una delle applicazioni più complesse è la struttura di un drone stratosferico, che richiede condizioni ideali per camere a vuoto e ambienti di prova. Questa parte è stata stampata in un unico pezzo utilizzando il materiale ULTEMTM 9085 sulla stampante 3D FUNMAT PRO 610HT. Grazie al volume di costruzione di 610 x 508 x 508 mm della stampante e alla temperatura costante della camera di 300°C, facilitata da un sistema termico ad alta temperatura, la parte è stata stampata con precisione.
Il CNES ha progettato la struttura del drone stratosferico per essere posizionata sotto palloni stratosferici per test di validazione. Di conseguenza, la parte è stata testata in ambienti diversi, simulando condizioni di atmosfera rarefatta o assente, per garantirne l’idoneità in condizioni estreme.
Durante il processo di test del prototipo, il design è stato qualificato dagli ingegneri meccanici del CNES, confermando anche la compatibilità del materiale ULTEMTM 9085 all’interno delle camere a vuoto senza fenomeni di degassamento, un elemento cruciale per mantenere prestazioni ottiche ideali. Oltre alle proprietà di basso degassamento, l’ULTEMTM per l’industria aerospaziale è fondamentale anche per il suo eccezionale rapporto resistenza-peso e la sua elevata resistenza termica, rendendolo ideale per la produzione di componenti soggetti a condizioni estreme nello spazio.
Collaborazione internazionale e prossimi sviluppi
Un altro progetto degno di nota in cui è stata utilizzata la stampa 3D è il Rover MMX, un’alleanza tra CNES, l’Agenzia Giapponese per l’Esplorazione Aerospaziale (JAXA) e il Centro Aerospaziale Tedesco (DLR). L’MMX, abbreviazione di Martian Moons eXploration, è un piccolo rover progettato per esplorare la più grande luna di Marte, Phobos. Per questo progetto, il team sta utilizzando la stampa 3D per creare, assemblare e testare le parti del rover.
Guardando al futuro, il CNES intende migliorare ulteriormente la propria tecnologia di manifattura additiva, massimizzando i benefici della stampa 3D per l’esplorazione spaziale.
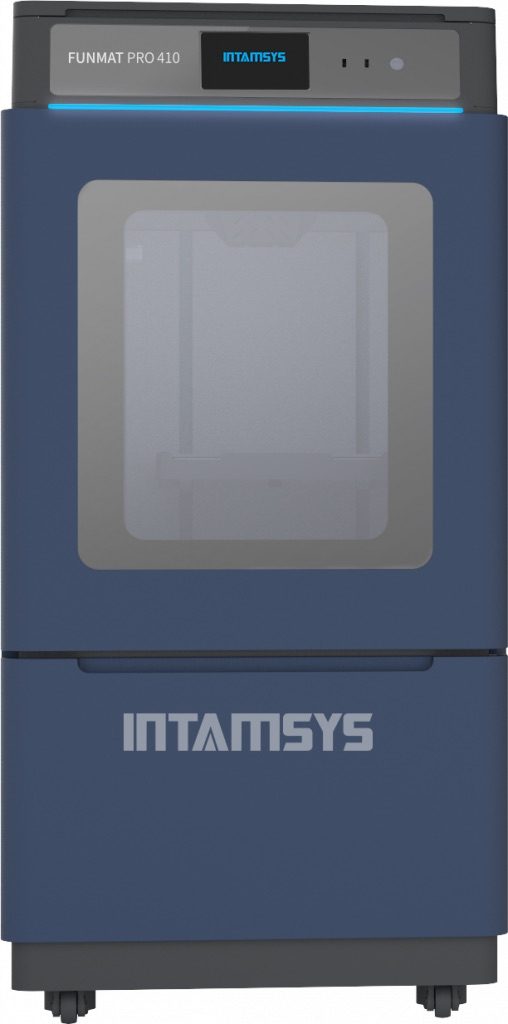