La divisione Manufacturing Intelligence di Hexagon ha presentato il suo nuovo approccio denominato Advanced Compensation, progettato per eliminare i tradizionali tentativi e errori nella produzione di componenti metallici di precisione. Questo metodo combina la simulazione dei processi e la compensazione basata su scansioni 3D, consentendo ai pezzi metallici complessi di raggiungere la forma desiderata durante la stampa.
Sfide della stampa con fusione a letto di polvere laser
La tecnica di fusione a letto di polvere laser (LPBF) si basa su processi fisici intricati, che possono complicare l’adattamento in applicazioni che richiedono alta precisione, come nella costruzione di macchinari, nell’aerospazio e nella produzione di protesi mediche. Questi settori necessitano di superfici di alta qualità, ripetibilità e precisione dimensionale, requisiti difficili da soddisfare con LPBF a causa di problemi come difetti, incoerenze e deviazioni dimensionali.
Come funziona l’approccio Advanced Compensation
Unendo la simulazione dei processi alla compensazione metrologica, il metodo Advanced Compensation offre una qualità costante anche per geometrie sottili e materiali complessi. I profili di superficie raggiungono una tolleranza del 98%-100%, semplificando al contempo il processo di stampa.
Un esempio significativo è fornito da Additive Industries, che ha adottato questo approccio per stampare un miscelatore di scarico in acciaio inossidabile per motori a reazione. Grazie all’Advanced Compensation, l’azienda ha raggiunto una precisione di 0,2 mm utilizzando un solo prototipo.
“Con questo approccio, abbiamo stampato con successo un componente in acciaio 316L di grandi dimensioni con una tolleranza superficiale di +/-0,2 mm, nonostante una distorsione naturale superiore ai 3 mm nelle versioni precedenti,” ha dichiarato Alex Redwood, responsabile delle applicazioni di Additive Industries. “Abbiamo ridotto i tempi, minimizzato gli sprechi di materiale e ottimizzato le strutture di supporto, aprendo nuove possibilità per la produzione additiva su larga scala.”
Strumenti digitali per una maggiore efficienza
Il software Simufact Additive di Hexagon prevede distorsioni e ritiri con simulazioni accurate, riducendo il numero di prove di stampa necessarie. Inoltre, il software VGSTUDIO MAX offre analisi metrologiche e scansioni 3D per affrontare caratteristiche più complesse. Questo strumento compensa la mesh stampabile basandosi sulle deviazioni rilevate da scansioni ottiche o tomografie computerizzate, senza richiedere competenze specifiche in metrologia.
“Se si tratta di una geometria complessa e di grandi dimensioni, la simulazione consente di risparmiare tempo e denaro, anche per un singolo pezzo,” ha spiegato Mathieu Perennou, Direttore della Strategia Additiva di Hexagon. “Quando la simulazione non è sufficiente, abbiamo semplificato il processo per compensare eventuali problemi residui attraverso scansioni 3D ottiche, garantendo il successo al secondo tentativo.”
Un futuro senza tentativi inutili
Questo approccio basato sui dati elimina l’incertezza nella stampa di piccoli lotti e può essere scalato per ottimizzare processi più complessi, utilizzando gemelli digitali che considerano non solo la geometria, ma anche i parametri della macchina e il comportamento dei materiali. Hexagon dimostra così come innovazione e precisione possano convergere per rivoluzionare la stampa 3D dei metalli.
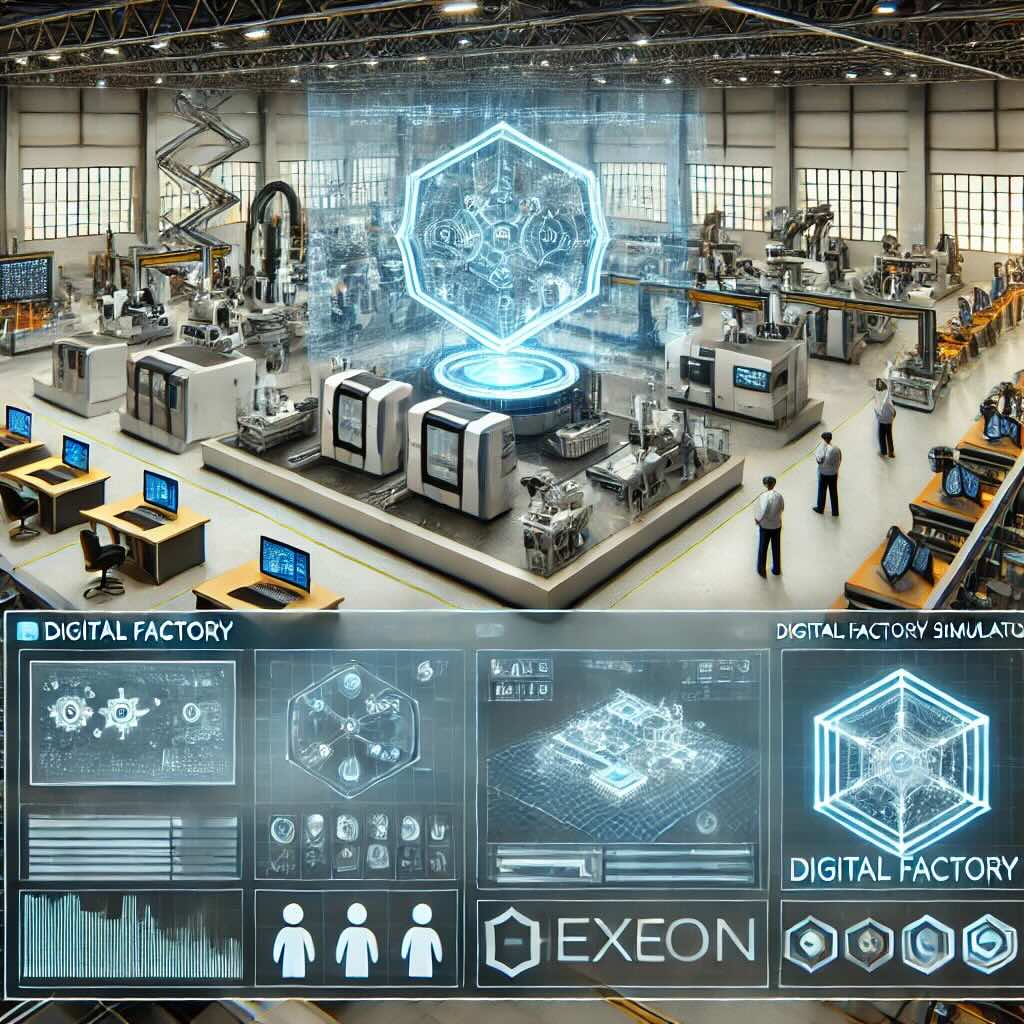