EMAG adotta la tecnologia LMD per rispondere alle nuove normative europee sulla sostenibilità nell’automotive
Il produttore tedesco di macchine utensili EMAG propone la sua tecnologia ELC 450 LMD per la deposizione laser di metalli, in risposta ai requisiti ambientali stabiliti dalle normative europee per il settore automobilistico.
A partire da novembre 2026, entrerà in vigore il nuovo standard Euro 7, che prevede una riduzione significativa delle emissioni di particolato derivanti da componenti non legati al motore, come i dischi freno. Tra le misure previste, è richiesto un taglio del 27% delle emissioni da abrasione dei freni, fissando un nuovo limite massimo di 7 milligrammi di particolato per chilometro, rispetto ai circa 40 milligrammi attualmente generati dai veicoli.
Un nuovo approccio per dischi freno più sostenibili
Per supportare l’adeguamento ai nuovi parametri, EMAG propone la tecnologia LMD (Laser Metal Deposition) attraverso il sistema ELC 450, che consente di applicare un rivestimento metallico duro ai dischi freno. Questo rivestimento migliora la resistenza all’usura e alla corrosione, prolungando la durata utile del componente e contribuendo a ridurre la produzione di particolato. Inoltre, i dischi trattati richiedono interventi di manutenzione meno frequenti, con benefici diretti anche per l’utente finale.
Dischi freno come fonte significativa di emissioni
Le emissioni generate dal sistema frenante sono spesso trascurate rispetto a quelle provenienti dal motore. Tuttavia, secondo l’azienda Prima Additive, circa il 21% delle emissioni di particolato dei veicoli a combustione è riconducibile all’usura dei dischi. Questo fenomeno si verifica durante la frenata, quando l’attrito tra disco e pastiglia genera particelle di dimensioni microscopiche, che si disperdono nell’ambiente.
Lo standard Euro 7 prevede anche una riduzione del 13% delle emissioni totali di particolato per ciascun veicolo. Per rispondere a queste esigenze, i costruttori devono valutare nuove tecnologie produttive.
Criticità degli approcci alternativi
Secondo EMAG, soluzioni alternative come i sistemi di estrazione delle polveri installati vicino ai freni offrono una copertura parziale del problema e comportano modifiche strutturali complesse per i produttori di veicoli. Le pastiglie freno NAO (Non-Asbestos Organic), pur essendo considerate una scelta più ecologica, perdono efficacia con l’uso e non garantiscono il rispetto dei nuovi limiti imposti dalle normative.
EMAG individua quindi nel rivestimento dei dischi freno un’alternativa più efficace e sostenibile, capace di combinare riduzione delle emissioni e incremento della durata operativa, con conseguente diminuzione dell’impatto ambientale complessivo, inclusi produzione, logistica e smaltimento.
Produzione additiva applicata ai rivestimenti
I rivestimenti per dischi freno non sono una novità, ma i metodi convenzionali come la spruzzatura termica o l’elettrodeposizione hanno limiti strutturali: non garantiscono un legame metallurgico diretto con il materiale di base, richiedendo complesse fasi di post-lavorazione.
Con la tecnologia LMD, EMAG propone un sistema che saldando direttamente il materiale metallico al disco, evita sprechi di materiale e consente un’applicazione più efficiente del rivestimento. Inoltre, il processo è pensato per produzioni su larga scala, grazie a una struttura modulare e flessibile che può essere adattata a seconda delle esigenze di produzione.
Il sistema è disponibile in diverse configurazioni:
ELC 450 LMD con un modulo di processo
ELC 450 DUO LMD con due moduli
ELC 450 TRIO LMD con tre moduli
Questo consente di adattare il sistema a diverse capacità produttive e organizzazioni di turno, rispondendo alle esigenze di case automobilistiche e fornitori.
Confronto con metodi tradizionali di rivestimento
Secondo EMAG, il sistema LMD si distingue da altri approcci come il rivestimento HVOF (High Velocity Oxygen Fuel), che prevede l’applicazione del metallo a velocità elevata con conseguente dispersione di materiale e perdite consistenti. LMD, invece, prevede una deposizione controllata e localizzata, con una maggiore efficienza nell’uso del materiale.
La stampa 3D nella produzione automobilistica sostenibile
EMAG non è l’unica realtà a puntare sull’additive manufacturing per migliorare l’impatto ambientale. Prima Additive ha sviluppato, in collaborazione con Comau, una soluzione per il rivestimento rapido dei dischi freno, destinata a Stellantis. Il sistema Rapid Coating Process integra laser, robotica, gestione polveri e tecnologia DED (Direct Energy Deposition), riuscendo a ridurre le emissioni legate all’usura dei dischi fino all’80%.
Anche altre realtà stanno adottando la produzione additiva per migliorare la sostenibilità. GM Ventures, la divisione venture capital di General Motors, ha investito in Forge Nano, azienda attiva nella deposizione a strati atomici (ALD) per lo sviluppo di materiali avanzati per batterie, con l’obiettivo di migliorare l’efficienza e ridurre i costi dei veicoli elettrici.
Nel Regno Unito, McLaren ha presentato una nuova hypercar ibrida dotata di componenti sospensivi in titanio stampati in 3D. I bracci trasversali e i montanti anteriori sono stati realizzati grazie alla collaborazione con Divergent Technologies, utilizzando il sistema DAPS (Divergent Adaptive Production System). Questa partnership punta a rendere più efficiente e sostenibile la produzione di veicoli ad alte prestazioni.
Scheda tecnica – Sistema EMAG ELC 450 LMD (Laser Metal Deposition)
Voce | Dettagli |
---|---|
Tecnologia | Deposizione laser di metallo (LMD – Laser Metal Deposition) |
Applicazione principale | Rivestimento di dischi freno per veicoli |
Finalità | Riduzione delle emissioni da abrasione, aumento della durata, resistenza all’usura |
Materiali utilizzabili | Combinazioni multiple di leghe metalliche |
Vantaggi ambientali | Fino all’80% di riduzione delle emissioni, minori sostituzioni, meno smaltimenti |
Configurazioni disponibili | – ELC 450 (1 modulo) \n- ELC 450 DUO (2 moduli) \n- ELC 450 TRIO (3 moduli) |
Struttura del sistema | Modulare, espandibile in funzione della capacità produttiva richiesta |
Tipo di legame del rivestimento | Metallurgico diretto (senza necessità di post-lavorazione complessa) |
Efficienza del materiale | Basso spreco grazie a deposizione localizzata |
Compatibilità produttiva | Adatto per linee ad alto volume, integrazione in cicli esistenti |
Alternative superate | Spruzzatura termica (HVOF), elettrodeposizione, sistemi di aspirazione freni |
Settori di impiego | Automotive (OEM e Tier 1), veicoli elettrici, componenti meccanici usurabili |
Integrazione in fabbrica | Possibilità di adattamento a strutture di turno multiple |
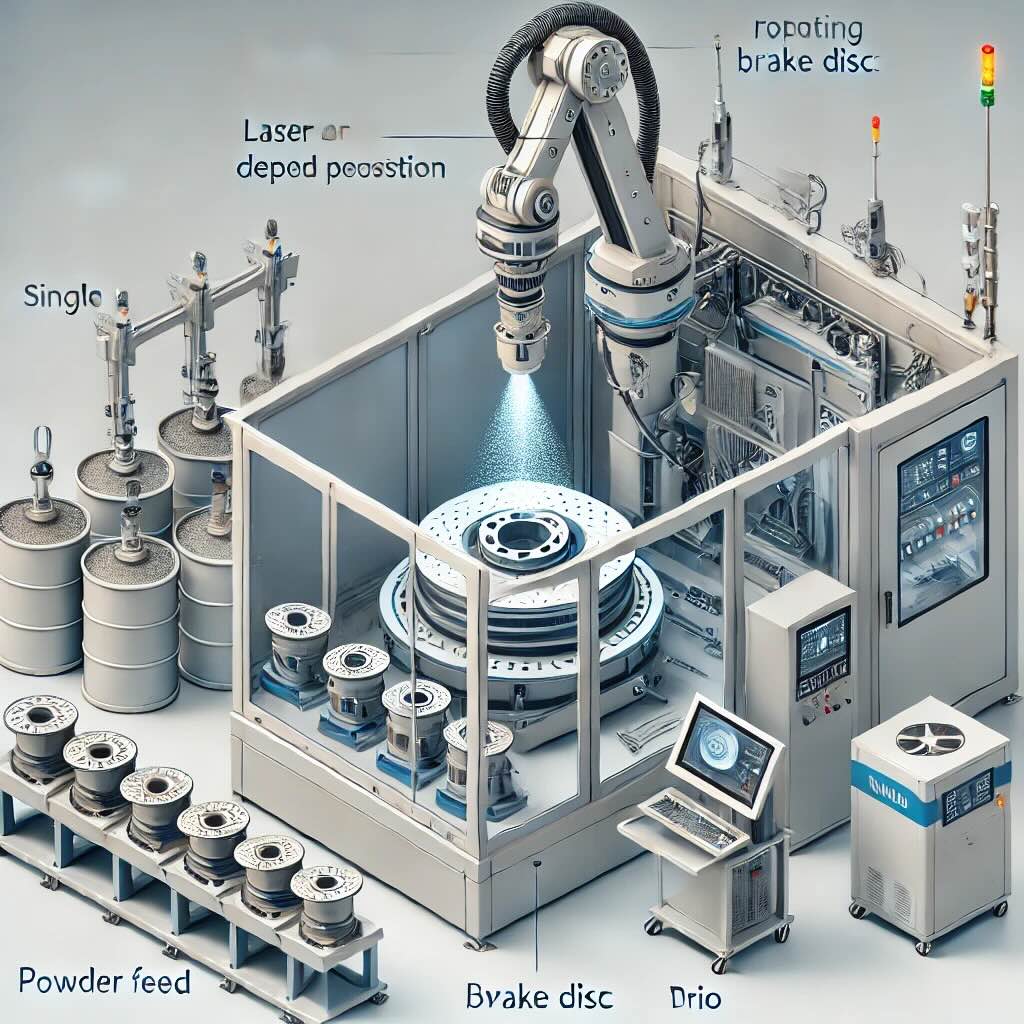