Reinforce 3D e Spring Srl rafforzano la collaborazione strategica per l’avanzamento della produzione di materiali compositi
Reinforce 3D, azienda spagnola sviluppatrice della tecnologia Continuous Fiber Injection Process (CFIP), ha avviato una partnership strategica con Spring Srl, un’impresa italiana attiva nella stampa 3D, con l’obiettivo di accelerare l’adozione e lo sviluppo della tecnologia CFIP in materiali ad alte prestazioni e processi di produzione avanzati.
Combinando la tecnologia CFIP di Reinforce 3D con l’esperienza di Spring Srl nella manifattura additiva, questa collaborazione permetterà la creazione di componenti strutturali rinforzati con una resistenza meccanica superiore, maggiore durata e ottimizzazione del rapporto peso-prestazioni. L’accordo rappresenta un passo significativo per industrie come l’aerospaziale, l’automotive e l’ingegneria industriale, contribuendo allo sviluppo continuo delle prestazioni dei materiali compositi.
Espansione delle capacità nella lavorazione dei materiali compositi
Fabio Gualdo, Direttore Generale di Spring Srl, ha dichiarato: “Spring Srl è da tempo un pioniere nel settore della manifattura additiva. Integrando la tecnologia CFIP di Reinforce 3D, stiamo ampliando le nostre capacità di rinforzo dei compositi e offrendo soluzioni di nuova generazione per applicazioni ingegneristiche ad alte prestazioni.”
Tecnologia CFIP di Reinforce 3D
Reinforce 3D è stata fondata nel 2020 come progetto all’interno del centro tecnologico Eurecat in Catalogna, Spagna. Nel 2022, l’iniziativa ha ottenuto un investimento dal BeAble Innvierte Kets Fund (BIKF), Eurecat e Marc Crescenti, portando alla costituzione ufficiale dell’azienda.
Nel 2023, Reinforce 3D ha introdotto la sua macchina “Delta”, basata sulla tecnologia CFIP brevettata. CFIP è un metodo di post-elaborazione pensato per migliorare la resistenza e ridurre il peso dei pezzi stampati in 3D. Il processo inietta fibre continue, come quelle in carbonio, insieme a resina in cavità tubolari all’interno del pezzo stampato. Una volta indurita, la resina lega le fibre al materiale, migliorando le proprietà meccaniche e le prestazioni del componente.
Questo metodo consente di posizionare le fibre in direzioni multiple, anche tra gli strati, massimizzando la resistenza del pezzo. CFIP è una tecnologia versatile, applicabile a componenti realizzati con una varietà di materiali per la stampa 3D, tra cui plastica, metallo e ceramica.
Collaborazione per lo sviluppo della tecnologia CFIP
Attraverso questa alleanza, Reinforce 3D e Spring Srl lavoreranno insieme per perfezionare la tecnologia CFIP per la produzione su larga scala, garantendo la sua integrazione fluida con le tecniche di produzione esistenti. La collaborazione si concentrerà sullo sviluppo congiunto di tecniche di produzione di compositi, con un’attenzione particolare alla scalabilità, all’automazione e all’ottimizzazione delle prestazioni.
L’accordo si impegna anche a migliorare le metodologie di rinforzo, ad ampliare la compatibilità dei materiali e a fissare nuovi parametri di prestazione per i compositi. Saranno condotte simulazioni FEM/FEA, validazioni meccaniche e prove di produzione per garantire i massimi standard qualitativi per i componenti prodotti.
Soluzioni di post-elaborazione nel settore della stampa 3D
Reinforce 3D e Spring Srl non sono le uniche a fare progressi nelle tecnologie di post-elaborazione nel settore della stampa 3D. L’italiana CRP Technology ha recentemente introdotto soluzioni di post-elaborazione che combinano Selective Laser Sintering (SLS), Vapor Smoothing e lavorazioni CNC. Questa innovazione migliora la qualità e le prestazioni dei materiali compositi Windform di CRP, rispondendo alle elevate esigenze di performance di settori come motorsport, aerospaziale e automotive.
Nel frattempo, il fornitore tedesco di soluzioni di post-elaborazione DyeMansion ha attirato l’attenzione con la sua tecnologia Powerfuse S per la levigatura a vapore, adottata da centri di servizi come Forecast 3D, FKM, Hasenauer & Hesser e RapidCenter. Powerfuse S offre vantaggi ecologici sostituendo i solventi a base di PFAS con alternative sostenibili, riducendo le emissioni, i requisiti infrastrutturali di sicurezza e gli oneri normativi, garantendo al contempo una qualità costante per geometrie complesse.
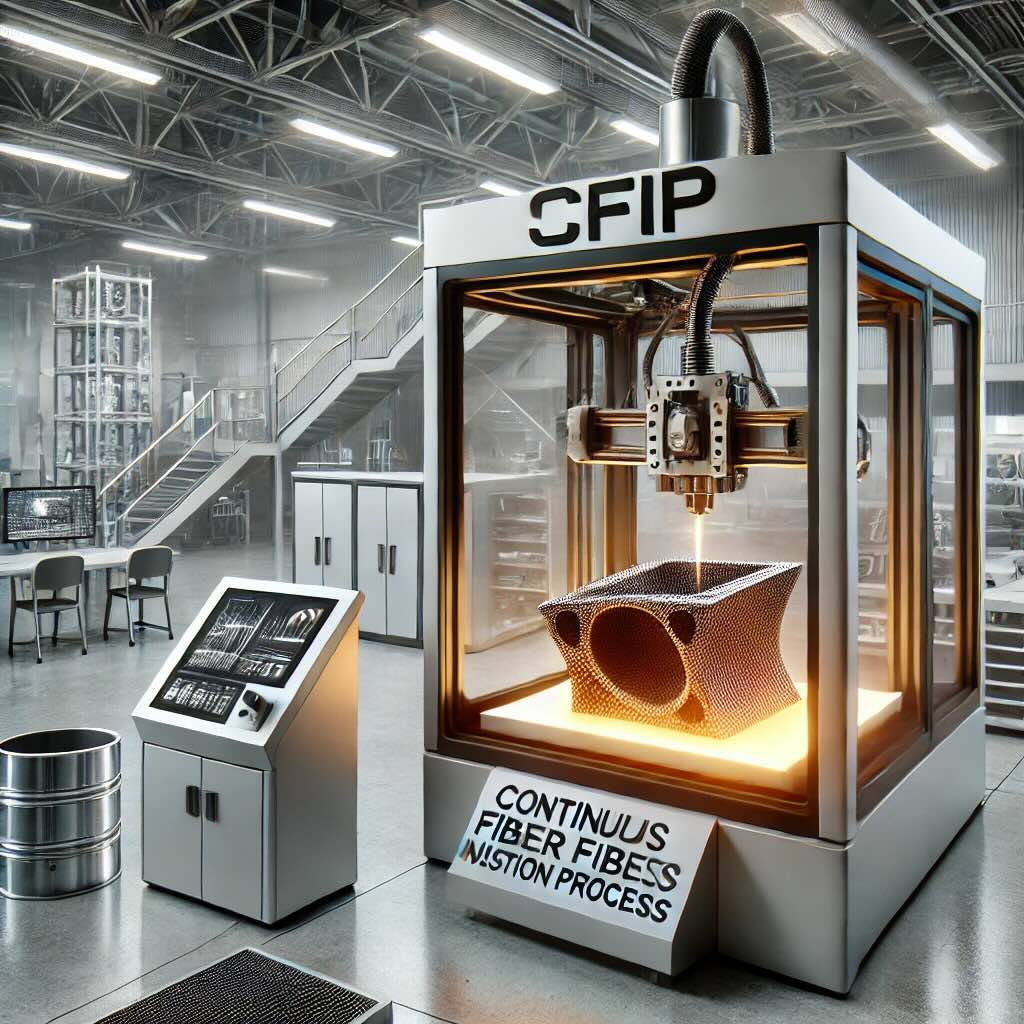