Contesto e criticità nella stampa di leghe ad alte prestazioni
Nel settore delle turbine a gas, le pale rappresentano componenti critici sottoposti a sollecitazioni meccaniche e termiche estreme. Per questa ragione, materiali come il CM247LC—una superlega a base nichel caratterizzata da elevata resistenza alle alte temperature—vengono scelti per garantire durata e affidabilità. Tuttavia, durante la produzione tramite laser powder bed fusion, su questi componenti si manifestano frequentemente cricche di solidificazione e tensioni residue che ne compromettono l’integrità strutturale.
Limiti delle strategie di scansione tradizionali
Il processo di sinterizzazione laser comune prevede l’uso di tracciati continui e di notevole lunghezza: ciò provoca accumuli di calore non omogenei e spiccate variazioni termiche tra zone adiacenti. Di conseguenza, la velocità di raffreddamento disomogenea genera cricche lungo i bordi di grano e una distribuzione irregolare delle tensioni interne, elementi che riducono la tenacità complessiva del pezzo e ne limitano l’applicabilità in ambienti critici.
Scansione a vettori brevi per un controllo termico più uniforme
Il team di ricerca del Centre for Additive Manufacture – Metal (CAM2) ha esplorato una diversa logica di scansione, sostituendo le classiche linee continue con vettori di dimensioni contenute. Questo approccio consente di suddividere il percorso del laser in segmenti più corti, distribuendo il calore in modo più omogeneo e riducendo al minimo le differenze di temperatura tra le sezioni adiacenti. Il risultato è una riduzione significativa dei fenomeni di solidificazione irregolare e delle tensioni interne, con impatto diretto sulla qualità e sulla robustezza delle pale prodotte.
“Virtual” stabilizzazione della geometria
Oltre alla scansione a vettori ridotti, gli studiosi hanno introdotto un metodo di stabilizzazione matematica—denominato Virtual Clamping—capace di correggere digitalmente le deformazioni dovute al raffreddamento. Gli algoritmi impiegati ricostruiscono la forma ideale del componente senza l’influenza delle sollecitazioni di serraggio, permettendo una misurazione e una valutazione della microstruttura priva di distorsioni.
Controllo mirato della microstruttura in aree critiche
Un aspetto distintivo dello studio riguarda l’applicazione localizzata dei vettori brevi nelle zone di maggiore concentrazione di sollecitazioni, come le radici delle pale. In queste aree, il fenomeno del strain age cracking (SAC) rappresenta una delle principali cause di guasto. Grazie alla scansione mirata, è possibile ottenere zone con grana raffinata e orientamento del reticolo cristallino controllato, meno soggette all’insorgenza di cricche sotto carico.
Test e risultati
Le prove condotte sui campioni hanno mostrato un drastico calo delle cricche di solidificazione e una distribuzione più uniforme delle tensioni residue. I ricercatori hanno osservato un miglioramento della duttilità complessiva e una maggiore ripetibilità dei risultati lungo diverse build plate. Questi miglioramenti contribuiscono a rendere la produzione additiva di CM247LC una soluzione concreta anche per componenti ad alto stress meccanico e termico.
Prospettive per la resistenza al creep
Parallelamente alla riduzione delle cricche, il gruppo di lavoro si dedica all’ottimizzazione delle proprietà di resistenza al creep delle parti stampate. L’obiettivo è avvicinare il comportamento a lungo termine delle componenti additive a quello dei pezzi prodotti per fusione convenzionale, raggiungendo livelli di stabilità dimensionale e integrità meccanica idonei alle sezioni più calde della turbina.
Implicazioni industriali
L’adozione di strategie di scansione a vettori brevi e di Virtual Clamping offre alle aziende del settore turbine un percorso per ottenere pale con caratteristiche prestazionali comparabili a quelle forgiate o fuse, riducendo al contempo tempi di sviluppo e sprechi di materiale. Ciò apre la strada a un utilizzo più ampio della manifattura additiva in applicazioni aerospaziali e di generazione di energia, dove ogni miglioramento nella durabilità dei componenti può tradursi in efficienza operativa e riduzione dei costi di manutenzione.
QUINDI
L’approccio innovativo messo a punto dal CAM2 combina precisione termica e controllo microstrutturale per affrontare due dei principali ostacoli nella stampa 3D di superleghe: cricche di solidificazione e tensioni interne. Guardando al futuro, il perfezionamento delle proprietà di creep e la scalabilità del processo rappresentano le prossime tappe per integrare stabilmente queste metodologie nelle linee produttive di turbine a gas e altre applicazioni ad alta criticità.
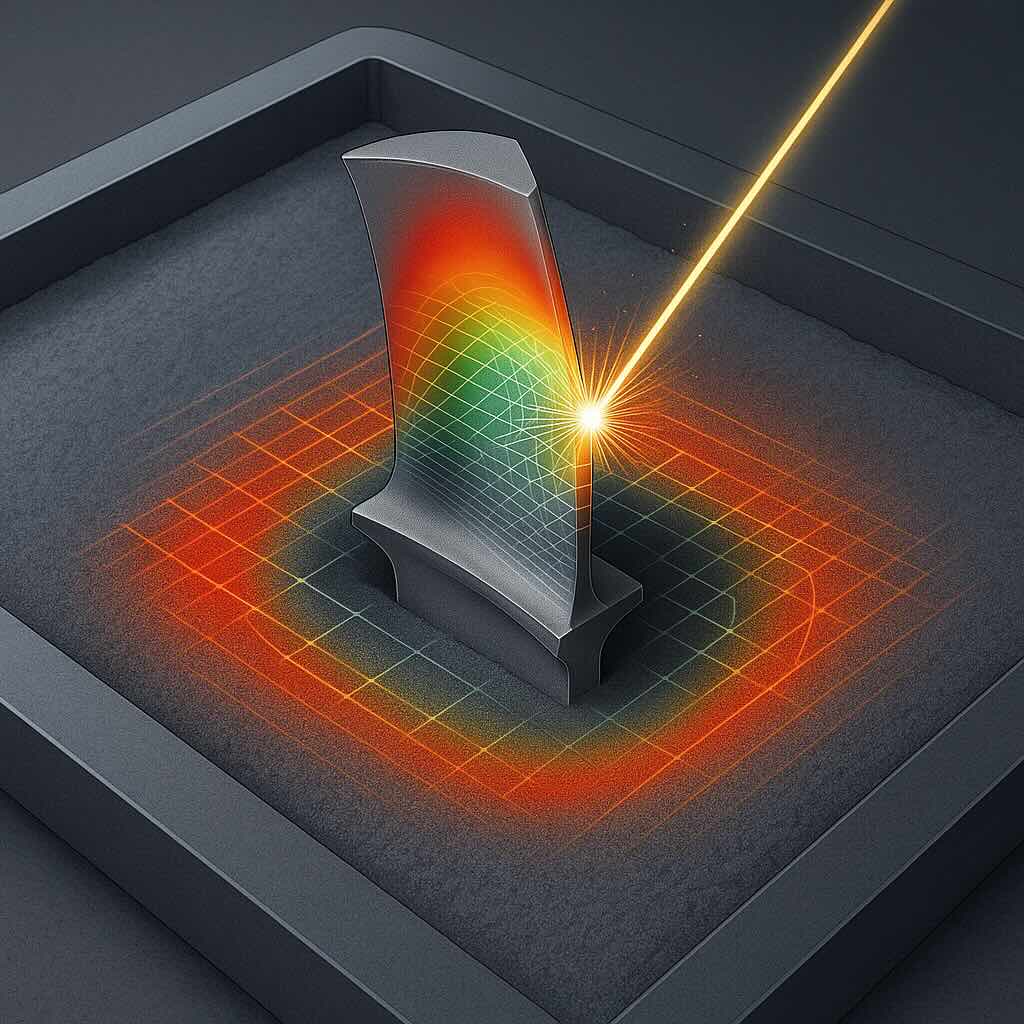