L’azienda gallese Apex Additive Technologies, specializzata in produzione additiva di metalli lungo tutta la filiera, ha introdotto nel proprio stabilimento il primo sistema ENESKApostprocess operativo sul territorio del Regno Unito. Questo impianto, sviluppato dall’azienda tedesca joke Technology e distribuito a livello locale da Moleroda Finishing Systems, è stato progettato per migliorare la sicurezza degli operatori e ridurre l’esposizione alle polveri sottili durante le fasi di post-lavorazione dei componenti metallici realizzati tramite stampa 3D.
Una soluzione integrata per la gestione delle polveri pericolose
Il cuore del sistema ENESKApostprocess è una cabina chiusa, con un volume operativo di 0,75 m², concepita per ospitare componenti stampati in 3D di dimensioni variabili. L’ambiente è dotato di un sistema di filtraggio certificato secondo gli standard ATEX, capace di trattenere ed eliminare le particelle disperse nell’aria che si generano durante operazioni meccaniche come la lucidatura, la molatura o la rimozione dei supporti. Queste attività comportano il rilascio di polveri metalliche potenzialmente nocive, con implicazioni rilevanti sia per la salute umana sia per la gestione del rischio in ambienti a rischio di esplosione (conformemente alle normative DSEAR – Dangerous Substances and Explosive Atmospheres Regulations).
L’interfaccia operativa è strutturata come un glove box: un contenitore sigillato dotato di guanti integrati che permettono di manipolare i pezzi al suo interno, isolando completamente l’operatore dall’ambiente di lavoro. Il portello resta bloccato finché i sensori non rilevano condizioni d’aria conformi agli standard ambientali previsti. In questo modo, si elimina la necessità di dispositivi di protezione individuale ingombranti e si consente al personale tecnico di operare in modo ergonomico, preciso e ripetibile.
Applicazioni pratiche nel contesto produttivo di Apex
Apex ha installato il nuovo impianto presso il proprio Digital Manufacturing Centre of Excellence, situato in Galles. In collaborazione con il distributore Moleroda, l’azienda ha scelto una soluzione che permettesse di conciliare l’efficienza produttiva con la salvaguardia della salute dei lavoratori.
Dall’avvio dell’utilizzo, il sistema è stato impiegato in diverse fasi fondamentali della post-elaborazione dei componenti metallici stampati in 3D: dalla rimozione dei supporti generati durante la stampa, alla pulizia delle superfici, passando per la separazione dalla piastra di costruzione e le operazioni di finitura superficiale. Tutte queste attività sono cruciali per garantire prestazioni funzionali e tolleranze dimensionali adeguate nei componenti destinati all’uso industriale.
Secondo quanto dichiarato da Youssef Beshay, fondatore e CEO dell’azienda, l’introduzione del sistema ha permesso di affrontare in modo unitario diverse criticità legate alla sicurezza: la dispersione delle polveri è stata contenuta alla fonte e l’esposizione dell’operatore è stata annullata grazie al sistema di filtraggio e alla configurazione della cabina sigillata.
Il contesto industriale evidenzia una crescente attenzione per le tecnologie di post-processing
L’introduzione di soluzioni come ENESKApostprocess si inserisce in un contesto più ampio, in cui il settore della produzione additiva sta attribuendo un’importanza crescente alle tecnologie di post-elaborazione. Le prestazioni finali dei componenti stampati in 3D, infatti, dipendono in misura rilevante dalle operazioni successive alla stampa, che devono essere eseguite in modo ripetibile, sicuro e conforme agli standard qualitativi richiesti dai vari settori industriali.
Un esempio rilevante in tal senso è rappresentato dall’azienda britannica Airframe Designs, attiva nel settore aerospaziale, che ha potenziato le proprie capacità produttive mediante l’acquisizione di una seconda stampante 3D Fortus 450mc FDM, fornita da Tri-Tech 3D. Questa macchina, impiegata nel programma nazionale NATEP (National Aerospace Technology Exploitation Programme), è in grado di realizzare assemblaggi complessi entro pochi giorni lavorativi, garantendo tolleranze di precisione fino a ±0,5 mm, grazie anche all’utilizzo di supporti idrosolubili.
Evoluzione della stampa multi-materiale: il caso di Fraunhofer IKTS
Un altro ambito che sta mostrando sviluppi significativi è quello della stampa multi-materiale, con l’introduzione di tecnologie in grado di gestire materiali differenti all’interno di un unico processo. Un esempio in questa direzione è rappresentato dalla collaborazione tra Fraunhofer IKTS e AMAREA Technology, che ha portato all’installazione della stampante MMJ ProX.
Questo sistema utilizza un metodo di deposizione basato su goccioline termoplastiche per combinare fino a sei materiali diversi all’interno dello stesso pezzo. La possibilità di regolare con precisione caratteristiche come durezza, conduttività o resistenza chimica apre nuove prospettive per applicazioni in settori come l’aerospaziale, l’energia, l’elettronica e la medicina. Le goccioline hanno un volume variabile tra 0,5 e 50 nanolitri, mentre lo spessore degli strati può oscillare tra 70 e 300 micrometri. Il raffreddamento rapido e la riutilizzabilità dei materiali completano il quadro, contribuendo all’efficienza e alla stabilità del processo produttivo.
Considerazioni finali
L’esperienza di Apex Additive Technologies con l’introduzione del sistema ENESKApostprocess evidenzia l’attenzione crescente verso soluzioni in grado di coniugare efficacia tecnica e sicurezza operativa nella post-elaborazione dei metalli stampati in 3D. Parallelamente, l’evoluzione delle attrezzature di stampa e la sperimentazione con materiali multipli dimostrano che la filiera della produzione additiva continua a svilupparsi in direzione di una maggiore integrazione, controllo dei processi e adattabilità alle esigenze di settori avanzati.
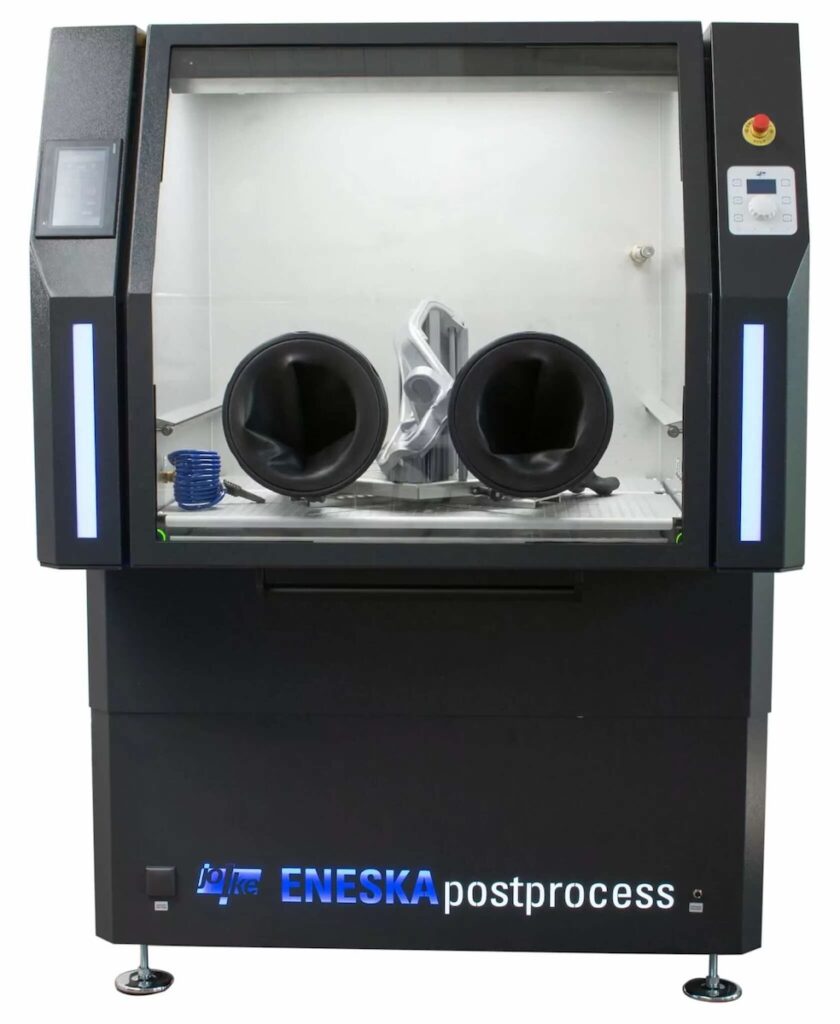