Stampare in 3D scocche audio per auto su scala reale con Aura3D A5
L’azienda statunitense Aura3D, specializzata nella progettazione di stampanti 3D industriali, ha messo a punto la A5 Pellet 3D Printer, un sistema che consente di realizzare scocche complete per impianti audio automobilistici direttamente da granuli di plastica. Grazie a questa tecnologia, i produttori possono accelerare i tempi di realizzazione, ridurre i costi del materiale e godere di una maggiore libertà progettuale rispetto ai metodi tradizionali.
Dalla simulazione acustica al pezzo finito
Il processo inizia con la modellazione digitale dell’involucro in ambiente CAD, dove si definiscono le geometrie interne ed esterne per ottimizzare la risposta acustica e l’inserimento nell’abitacolo specifico. Una volta approvato il progetto, l’A5 trasforma granuli di termoplastici tecnici – come ABS o compound rinforzati con fibra di carbonio – in strati sovrapposti, costruendo l’involucro completo (530 × 530 × 530 mm) senza necessità di stampi o attrezzaggi.
Post‐processing e montaggio
Terminata la stampa, il componente subisce la rimozione dei materiali di supporto, una levigatura delle superfici e l’applicazione di finiture esterne, vernici o trattamenti protettivi. A valle si procede con l’inserimento dei driver acustici, il posizionamento di schiume fonoassorbenti e il cablaggio interno, ottenendo un modulo pronto per l’installazione a bordo del veicolo.
Confronto con tecnologie concorrenti
-
Fused Deposition Modeling (FDM): per scocche di simili dimensioni richiede fino a dieci giorni, con costi elevati per piccole serie e limitata qualità superficiale.
-
Stampaggio a iniezione: prevede 40–50 giorni di attesa fra realizzazione stampo e avvio produzione, risultando conveniente solo per alti volumi.
-
Pellet‐based 3D printing di Aura3D: consegna pezzi finiti in circa otto ore, elimina costi di attrezzaggio, utilizza materiali a basso prezzo e si adatta a lotti ridotti e componenti di grandi dimensioni.
Scalabilità per esigenze diverse
Oltre al modello A5, Aura3D propone configurazioni più ampie:
-
A8 (800 × 800 × 810 mm)
-
A12 (1100 × 1000 × 1000 mm)
-
A16 (1600 × 1300 × 1250 mm)
Queste soluzioni trovano impiego non solo nel settore audio automobilistico, ma anche in ambiti come aerospazio, medicale e cantieristica navale, dove tempi rapidi e riduzione degli scarti sono requisiti indispensabili.
Esempi di applicazioni AM nell’industria auto
-
Donkervoort Automobielen si è affidata a Conflux Technology per produrre scambiatori aria‐acqua stampati in 3D destinati alla supercar P24 RS, con tecnologie derivate dalla Formula 1.
-
Subaru Corporation, in collaborazione con HP Inc. e DMM.make 3D Print, ha realizzato componenti in fibra di polimero mediante Jet Fusion per la concept car Legacy Outback BOOSTGEAR, svelata al Tokyo Auto Salon 2024.
Questi esempi dimostrano come la stampa additiva di ultima generazione stia trovando applicazioni concrete sui veicoli di serie, abilitando design complessi e personalizzazioni mirate senza penalizzare tempi e costi di sviluppo.
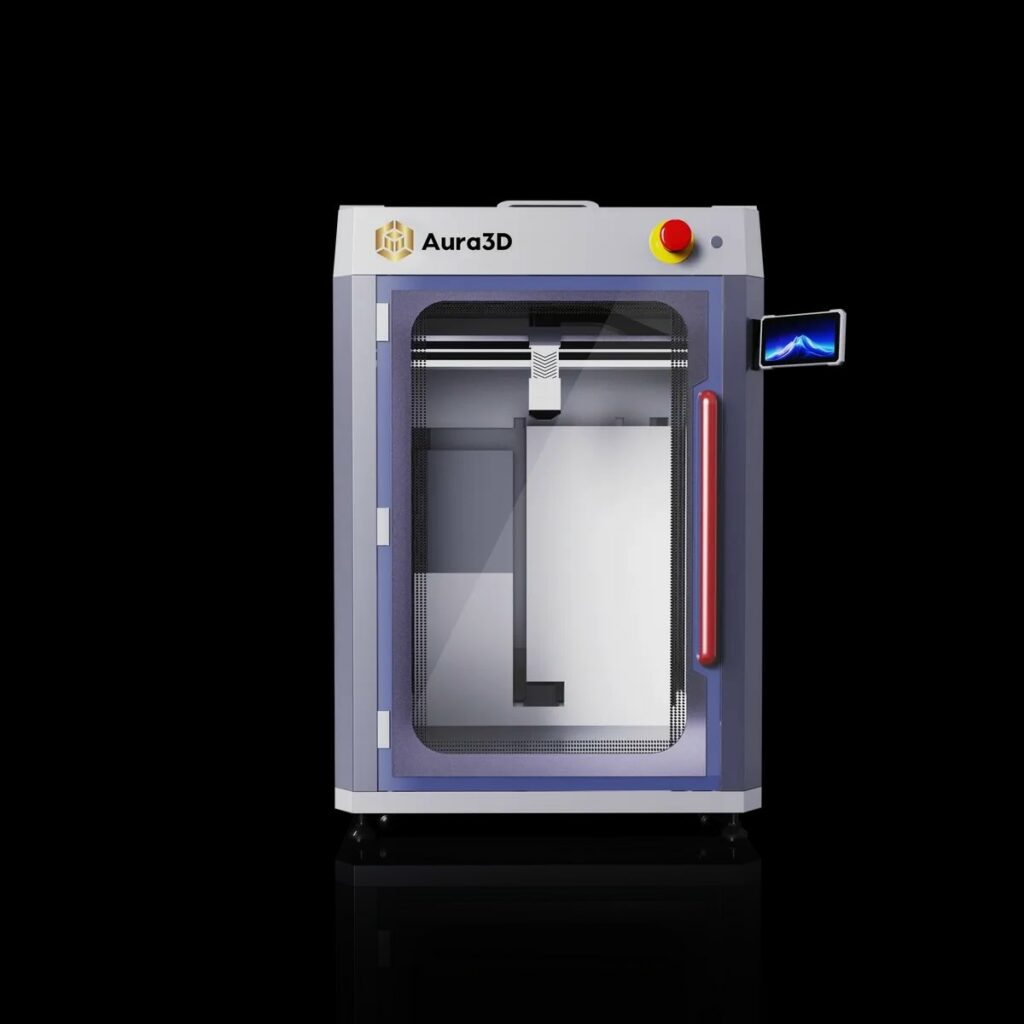