Rivoluzionare il design e la produzione di supercar con l’ecosistema UltiMaker
La rinomata casa automobilistica britannica Briggs Automotive Company utilizza stampanti 3D UltiMaker per progettare e produrre parti personalizzate per le sue auto sportive di alta gamma.
La Briggs Automotive Company (BAC) è stata fondata nel 2009 dai fratelli Neill e Ian Briggs, entrambi appassionati del mondo delle auto. Due anni dopo, la BAC ha rivoluzionato l’industria automobilistica con la prima supercar monoposto omologata per la strada al mondo: la BAC Mono. La Mono è stata la realizzazione della visione dei fratelli di un veicolo stradale che offrisse un’esperienza di guida autentica e pura combinata con le ultime tecnologie da corsa.
“Abbiamo voluto creare un’auto che rappresentasse lo sport della guida, un’attività di svago”, ha dichiarato Ian Briggs, direttore del design e co-fondatore della BAC. “Dal punto di vista dell’ispirazione, abbiamo guardato alla fantascienza, ai robot, alle cose del futuro. Per persone come noi che amano guidare, volevamo concentrarci su un aspetto e una sensazione futuristiche”.
Nel corso del tempo, la BAC ha apportato significativi miglioramenti e aggiornamenti alla Mono, dando vita alla Mono R. In grado di accelerare da 0 a 100 km/h in 2,5 secondi, la Mono R è una testimonianza del potenziale delle moderne tecniche di produzione.
Leader tecnologico nel settore automobilistico
Sempre all’avanguardia nelle innovazioni tecnologiche, la BAC agisce come un incubatore per le ultime innovazioni e concetti rivoluzionari all’interno dei suoi progetti pionieristici di ricerca e sviluppo.
A tal fine, la BAC è stata una delle prime ad adottare la stampa 3D. Poiché l’azienda progetta e produce la Mono R per gli appassionati e i collezionisti di auto sportive, realizza parti personalizzate in piccoli lotti. Di conseguenza, la lavorazione CNC o lo stampaggio ad iniezione non erano necessari per questo livello di produzione.
Invece, il team della BAC si è rivolto ad UltiMaker. L’ecosistema di stampa 3D UltiMaker ha consentito alla BAC di produrre parti altamente personalizzabili e di alta qualità in modo rapido ed economico, apportando significativi miglioramenti nelle iterazioni di design, riduzioni dei costi e nell’efficienza complessiva della produzione.
“Nei primi giorni, quando la stampa 3D era definita prototipazione rapida, non comprendevamo appieno le implicazioni sulle parti di produzione”, ha affermato Ian Briggs. “Ma ora oltre 44 parti diverse dell’auto sono stampate in 3D: componenti strutturali del motore, supporti per gli specchietti retrovisori, cornici per i fari. Abbiamo davvero abbracciato la stampa 3D e la libertà di progettazione che ci ha offerto. L’ecosistema UltiMaker ci consente di unire tutti i diversi aspetti della nostra produzione per essere costantemente ottimizzati e conservati in un’unica posizione”.
Gli ingegneri della BAC utilizzano esclusivamente stampanti 3D UltiMaker e attualmente utilizzano tre stampanti UltiMaker S5. La BAC produce rapidamente e testa molteplici iterazioni di design, incorporando i feedback dei clienti o apportando miglioramenti in base alle esigenze funzionali. Questo approccio iterativo consente la creazione di parti altamente personalizzabili ottimizzate per prestazioni, ergonomia ed estetica. L’accesso immediato alle stampanti UltiMaker consente alla BAC di produrre parti quando necessario, riducendo la necessità di grandi scorte di componenti pre-manufacturati.
Utilizzando la Digital Factory di UltiMaker, la BAC può centralizzare e semplificare le operazioni di stampa 3D, dalla gestione delle iterazioni di design e della preparazione della stampa, alla stampa vera e propria e alla post-produzione. La Digital Factory consente al team di archiviare i file digitali, insieme ai relativi parametri di stampa, impostazioni e specifiche dei materiali, garantendo la coerenza e la ripetibilità in molteplici istanze di stampa. Con l’accesso remoto, possono controllare le stampanti sulla linea di produzione che operano su richiesta 24 ore su 24.
“La Digital Factory di UltiMaker ha reso possibile migliorare i processi di produzione per la prototipazione e le parti di produzione presso la BAC”, ha affermato Thomas Tunstall, tecnico della carrozzeria e operatore di stampa 3D presso la BAC. “Ad esempio, posso pre-tagliare i lavori di stampa e salvarli nel deposito digitale, risparmiandomi molto tempo per le future stampe. La Digital Factory ci consente inoltre di integrare le stampanti con il nostro software, il che mi consente di gestire in remoto le stampanti, i progetti e i team”.
Il programma UltiMaker Material Alliance ha dato alla BAC la flessibilità di scegliere tra una vasta gamma di materiali di grado industriale che sono stati appositamente testati, certificati e ottimizzati per l’uso con le stampanti 3D UltiMaker. Questa versatilità dei materiali consente alla BAC di selezionare il materiale più adatto per ogni applicazione. La BAC utilizza esclusivamente materiali Addigy per tutte le parti stampate in 3D sulla Mono R, inclusa la fibra di carbonio in nylon per le parti che richiedono forti proprietà strutturali, come i bracci degli specchietti che supportano gli specchietti laterali e subiscono molte sollecitazioni, e le prese d’aria dal cassonetto dell’aria.
Ogni veicolo Mono R è realizzato su misura in base alle specifiche del cliente. Ad esempio, la seduta viene sagomata sul guidatore, le impugnature del volante vengono sagomate sul guidatore, viene scelto lo schema di colori dell’auto e persino le tute da corsa vengono realizzate su misura. Tutto è personalizzato e la stampa 3D consente alla BAC di stampare molte delle parti della Mono R. I clienti possono persino aggiungere le loro iniziali e i numeri delle auto direttamente sull’auto e sul portachiavi.
Grazie al supporto locale di UltiMaker GB e a una vasta rete di rivenditori nel Regno Unito e in Irlanda, la BAC può sfruttare il potere della stampa 3D. La stampa 3D ha dato al team una maggiore libertà di progettazione per realizzare geometrie complesse che sarebbero difficili o impossibili da produrre utilizzando i metodi di produzione tradizionali.
“Come produttore che si è avvicinato alla stampa 3D, una delle cose più importanti per noi era avere un supporto locale. È stato un percorso nuovo per noi. Le macchine erano nuove, i materiali erano nuovi, imparare a progettare le parti era nuovo. Avremmo aspettato più a lungo se non avessimo avuto il supporto locale. È stato fondamentale per noi adottare questa tecnologia”, ha dichiarato Briggs.
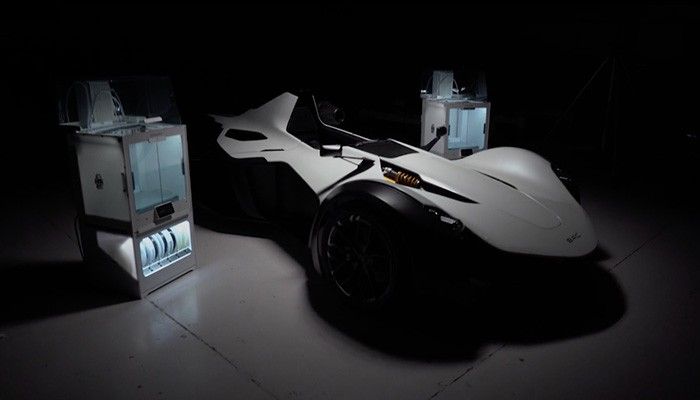
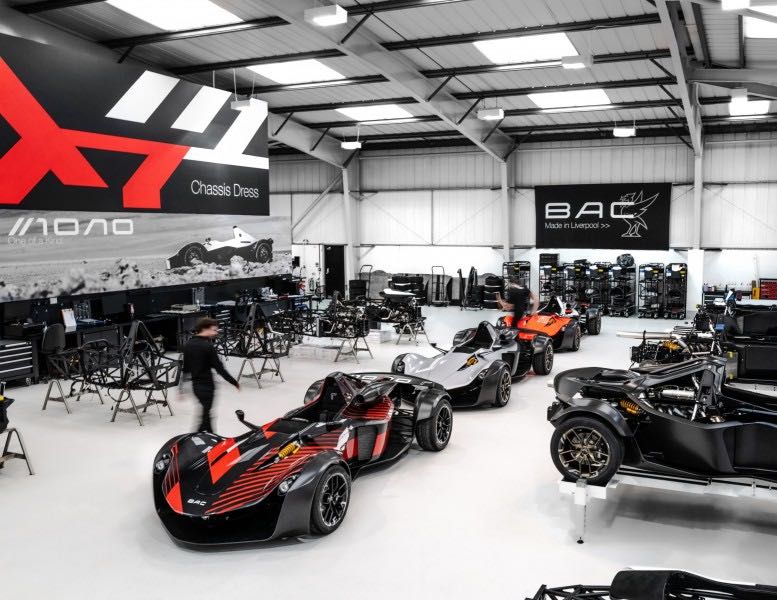
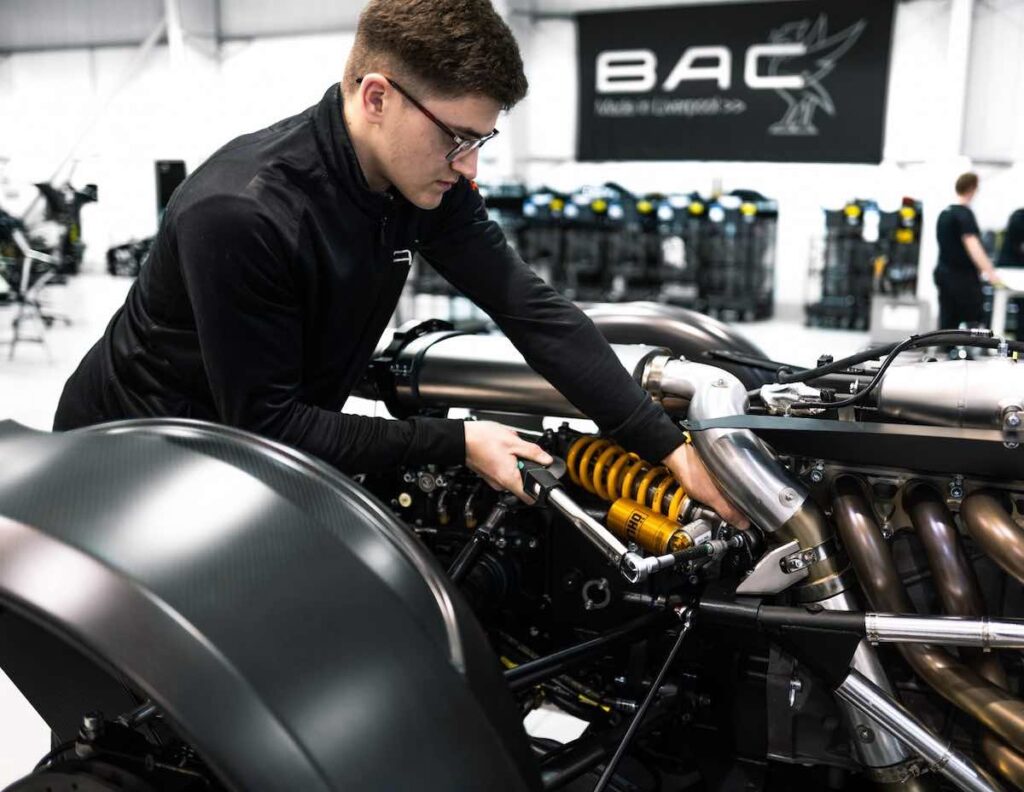

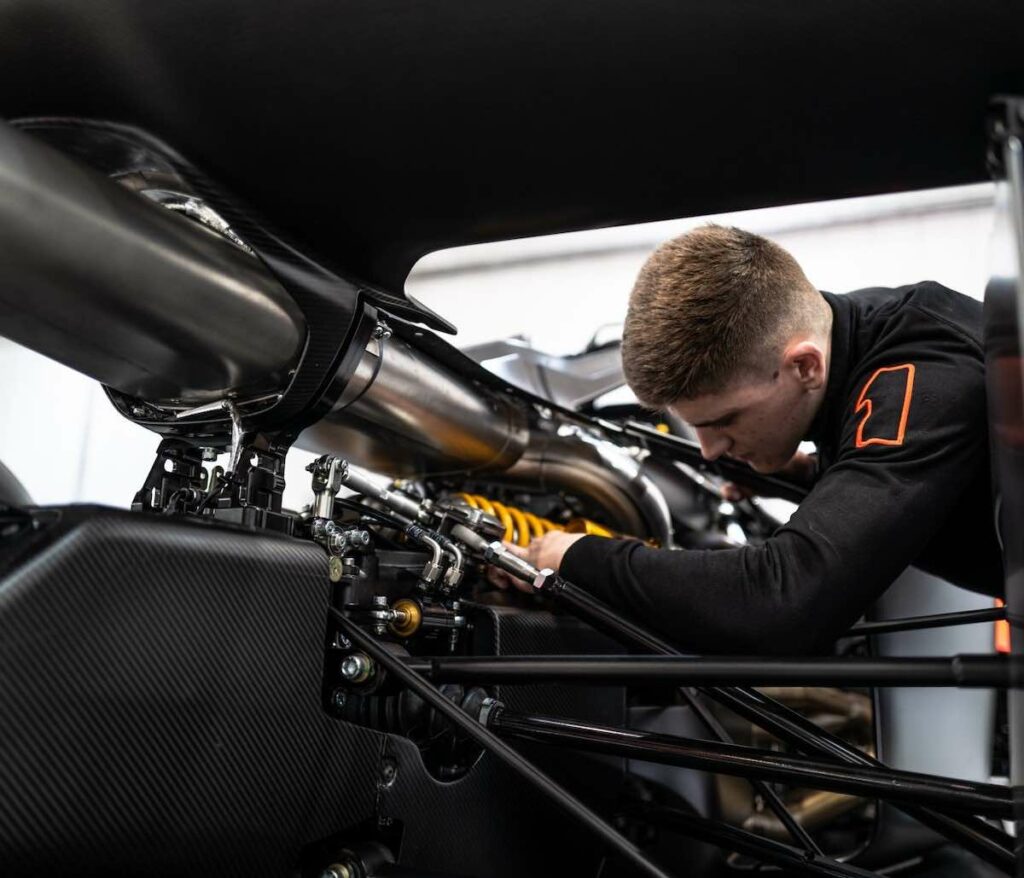
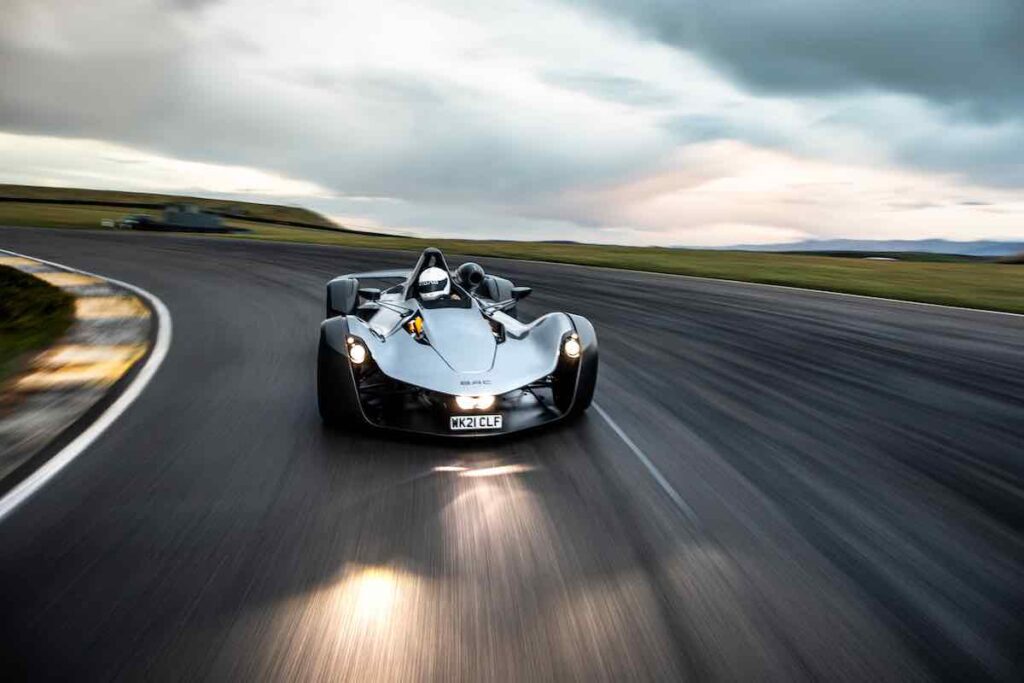