Tecniche Avanzate di Stampa 3D Multi-Materiale per l’Automotive
Università di Tohoku
Nell’ambito della ricerca applicata alla stampa 3D, l’Università di Tohoku si è distinta per uno sviluppo significativo nella tecnica di stampa 3D multi-materiale. Gli studiosi dell’Istituto per la Ricerca sui Materiali e del Centro per la Creazione di Nuova Industria hanno dimostrato come sia possibile realizzare parti automobilistiche leggere ma estremamente resistenti.
Il Processo di Stampa Metallica 3D
La stampa 3D metallica consente la costruzione di oggetti depositando strati successivi di metallo, uniti tra loro tramite l’applicazione di calore. Questa tecnica permette di ottenere forme uniche e altamente personalizzabili, spesso risultando meno dispendiose in termini di scarti rispetto ai metodi di fabbricazione tradizionali. Le “strutture multi-materiale”, che combinano strategicamente diversi materiali per ottimizzare le prestazioni di un componente, possono essere realizzate attraverso la stampa 3D. Ad esempio, parti automobilistiche in acciaio possono essere rese più leggere attraverso l’integrazione con l’alluminio. Data la vasta gamma di benefici, la padronanza di tali tecniche di stampa 3D sta attirando un crescente interesse da parte della comunità scientifica.
Sfide e Soluzioni nella Stampa Multi-Materiale
Nonostante i vantaggi, la stampa multi-materiale presenta alcune sfide. “I materiali multipli sono un argomento molto discusso nel campo della manifattura additiva per la flessibilità del processo”, spiega il Professore Associato Kenta Yamanaka dell’Università di Tohoku. “Tuttavia, un’importante sfida nell’implementazione pratica è che, per alcune combinazioni di metalli, come acciaio e alluminio, possono formarsi composti intermetallici fragili agli interfacci metallici diversi. Questo rende il materiale più leggero ma anche più fragile.”
Obiettivi e Metodologie di Ricerca
L’obiettivo dello studio era produrre una lega di acciaio-alluminio leggera ma senza compromessi sulla resistenza. Per raggiungere questo scopo, il team di ricerca ha utilizzato la tecnologia Laser Powder Bed Fusion (L-PBF), una delle principali tecnologie di stampa 3D metallica che impiega un laser per fondere selettivamente le polveri metalliche. Hanno scoperto che aumentare la velocità di scansione del laser riduce significativamente la formazione di composti intermetallici fragili (come Al5Fe2 e Al13Fe4). Hanno proposto che questa maggiore velocità di scansione porti a quello che viene definito solidificazione non equilibrata, che minimizza la separazione del soluto che altrimenti genererebbe punti deboli nel materiale. Il prodotto risultante ha dimostrato di avere interfacce di legame forti.
“In altre parole, non è possibile semplicemente unire due metalli e aspettarsi che aderiscano senza una strategia precisa”, afferma il Professore Aggiunto Seungkyun Yim (Università di Tohoku). “Abbiamo dovuto comprendere completamente il meccanismo di lega in situ prima.”
Applicazioni Future e Implicazioni
Partendo da questo risultato, hanno prototipato con successo il primo componente automobilistico multi-materiale a scala piena al mondo (torretta di sospensione) con una geometria su misura. Il gruppo di ricerca intende applicare queste scoperte ad altre combinazioni di metalli dove sono necessari miglioramenti simili nell’adesione, ampliando così le applicazioni possibili.
I risultati sono stati pubblicati nella rivista “Additive Manufacturing” il 19 novembre 2024.
DOI dell’Articolo: 10.1016/j.addma.2024.104529
Titolo dell’Articolo: “Manifattura additiva multi-materiale di lega di acciaio/Alluminio controllando l’interfaccia liquido/solido nella fusione laser su letto di polvere”
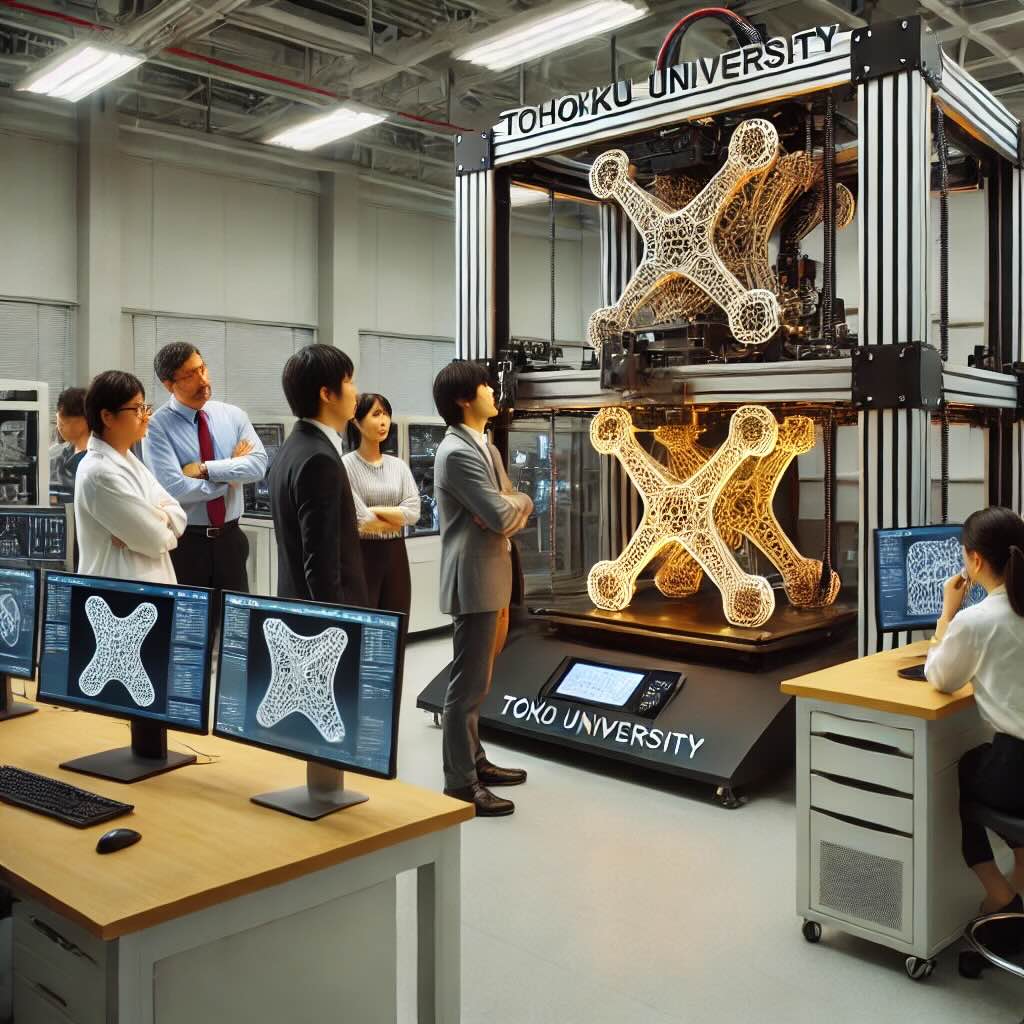