Un gruppo di ricerca del Lawrence Livermore National Laboratory, in collaborazione con l’Università della California a Santa Barbara, ha sviluppato una resina “one-pot” capace di indurire in presenza di due diverse lunghezze d’onda luminose. L’obiettivo è integrare durante la stampa 3D sia la componente strutturale definitiva sia le strutture di supporto, le cui parti di servizio si sciolgono in seguito, semplificando il flusso di lavoro e ampliando le possibilità progettuali.
Principio di funzionamento della resina a doppia reattività
La formulazione combina monomeri epossidici, che polimerizzano con radiazione UV a 365 nm, e monomeri (met)acrilici, sensibili alla luce visibile a 405 nm. Sotto l’azione selettiva di ciascuna lunghezza d’onda, la parte epossidica crea la rete portante a elevata resistenza, mentre la frazione acrilica costituisce un’impalcatura sacrificial che si dissolve completamente immergendola in una soluzione acquosa a pH basico.
La stampante DLP a doppia lunghezza d’onda
Bryan Moran e colleghi hanno realizzato un dispositivo DLP (Digital Light Processing) brevettato con un singolo chip a microspecchi digitali (DMD) capace di alternare, pixel per pixel, l’emissione di luce UV e luce visibile. Questo approccio evita l’allineamento tra più proiettori e riduce di oltre la metà i tempi di stampa rispetto agli impianti sequenziali, mantenendo alta la risoluzione delle parti sia strutturali sia di supporto.
Ottimizzazione chimica e prestazioni meccaniche
Attraverso spettroscopia FTIR in linea si è osservato che la polimerizzazione visibile cura esclusivamente i precursori acrilici, mentre la componente UV innesca sia la reazione cationica dell’epossido sia la reticolazione radicalica. Dopo una fase di post-indurimento termico, le parti di servizio vengono eliminate per degradazione in ambiente basico: la densità di reticolazione cala di circa un terzo, ma i provini finali mantengono un modulo elastico elevato e superfici regolari.
Dimostrazione su geometrie complesse
Per provare l’efficacia del metodo, sono stati stampati modelli come anelli intrecciati, una gabbia contenente una sfera libera e un’elica avvolta su due piccole sfere. I supporti solubili hanno sostenuto ponti e sbalzi durante l’estrusione senza deformazioni; una volta disciolti, le forme definitive restano pulite, con finiture omogenee e tolleranze entro pochi decimi di millimetro.
Confronto con altri progetti nel settore
Al MIT, gruppi guidati da ricercatori del Dipartimento di Ingegneria Chimica hanno sperimentato resine bicomponenti che, esposte a due lunghezze d’onda, differenziano tra zone flessibili e zone rigide. All’Università del Texas, un team ha realizzato una DLP multicolore capace di produrre supporti solubili in acetato di etile, utile per dettagli estremi in applicazioni aerospaziali. Queste esperienze convergono verso l’obiettivo di ridurre il tempo di post-lavorazione e di eliminare il rischio di danneggiamento dei pezzi.
Ambiti di applicazione e sviluppi futuri
La tecnica presenta interesse in settori quali la microfluidica, dove canali e valvole interne richiedono supporti rimovibili senza contaminazione; in ambito biomedicale, per scaffold anatomici a geometria complessa; e nei componenti aerospaziali, dove la precisione e la qualità superficiale sono fondamentali. Prossimi passi includono la standardizzazione delle resine e l’integrazione di moduli di lavaggio automatizzato direttamente nella stampante.
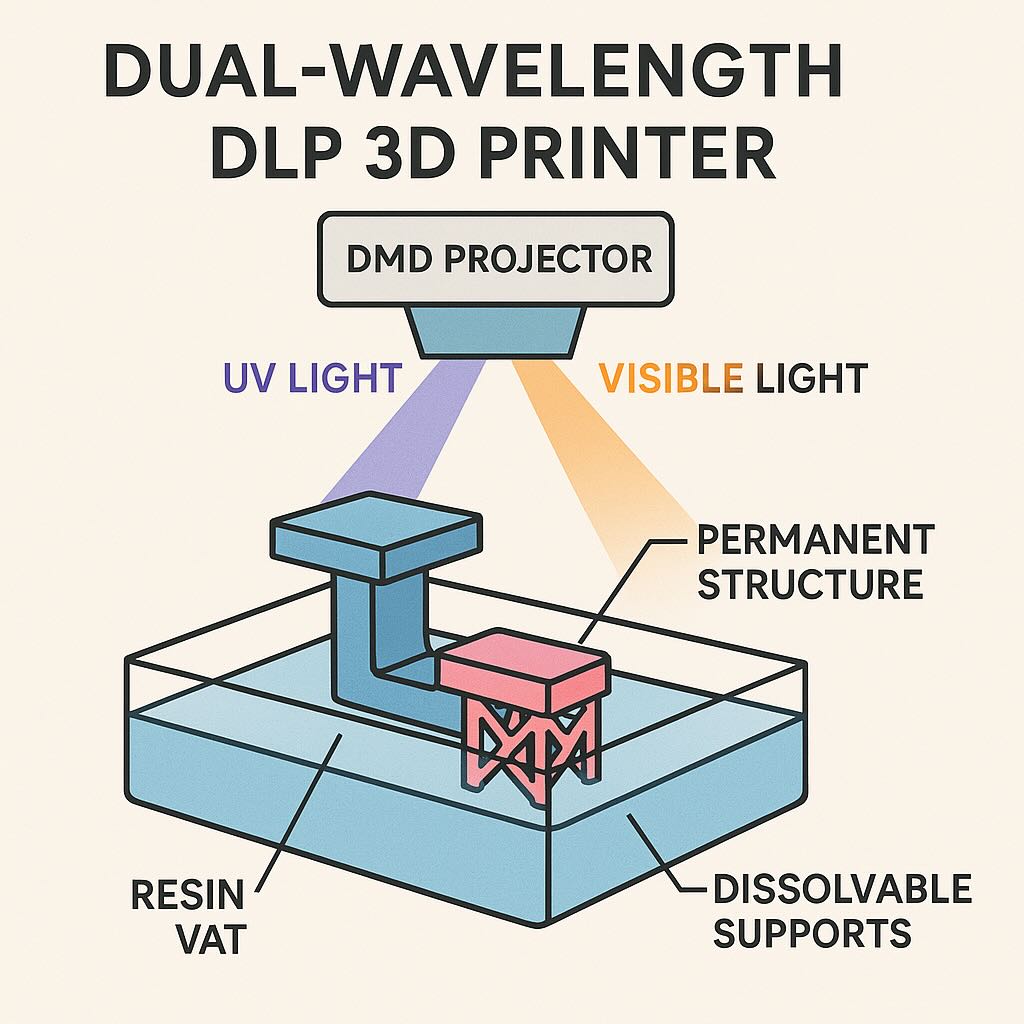