Nuovi approcci alla stampa 3D in metallo riducono costi e migliorano la qualità della superficie
Le aziende Equispheres, Aconity3D e Dyndrite hanno collaborato per sviluppare una soluzione innovativa che migliora la produzione additiva di metalli (AM), riducendo significativamente i costi e migliorando la qualità della superficie. Il loro studio congiunto ha dimostrato come l’integrazione di materiali ottimizzati, hardware all’avanguardia e software avanzato possa abbattere i costi di produzione dell’80% e migliorare la qualità superficiale dei componenti prodotti.
Tecnologia avanzata per velocità e precisione
Il progetto ha cercato di superare le sfide comuni nella produzione additiva di metallo, come la velocità di stampa, la riduzione dei costi e il mantenimento degli standard di qualità. Tradizionalmente, la produzione di parti metalliche ha comportato un compromesso tra questi fattori, con tempi di produzione lunghi e costi elevati, mentre la qualità superficiale spesso veniva sacrificata. Grazie alle nuove tecnologie utilizzate, è stato possibile raggiungere un equilibrio ottimale tra tutti e tre gli aspetti.
Materiali specializzati e hardware ottimizzato
Nel contesto di questo progetto, Equispheres ha fornito la sua polvere di alluminio NExP-1, progettata per il processo Laser Powder Bed Fusion (LPBF), caratterizzata da una dimensione uniforme delle particelle e una capacità di fusione ottimizzata. Aconity3D, invece, ha integrato un profilo del raggio laser con un design innovativo a “cappello a cilindro” nella stampante 3D AconityMIDI+, migliorando la velocità e la coerenza del processo di fusione. Infine, Dyndrite ha messo a disposizione il suo software LPBF Pro, che consente la regolazione precisa dei parametri di stampa, migliorando la qualità della superficie attraverso la segmentazione volumetrica.
Risultati tangibili e vantaggi economici
Uno degli esempi pratici dei miglioramenti ottenuti è la produzione di una valvola a sfera, per la quale sono stati raggiunti risultati notevoli: con uno spessore dello strato di 240 µm e parametri ottimizzati, la velocità di produzione è stata fino a 9 volte più rapida rispetto agli approcci tradizionali. Inoltre, i costi per componente sono diminuiti dell’80%, mentre la rugosità superficiale (Sa) è stata ridotta di oltre l’80%, grazie all’uso del software avanzato di Dyndrite.
Questo studio ha confermato che combinando materiali ottimizzati, hardware innovativo e software avanzato, è possibile ottenere una produzione additiva di metallo altamente produttiva e di qualità superiore, riducendo al minimo la necessità di costose e complesse operazioni di post-elaborazione.
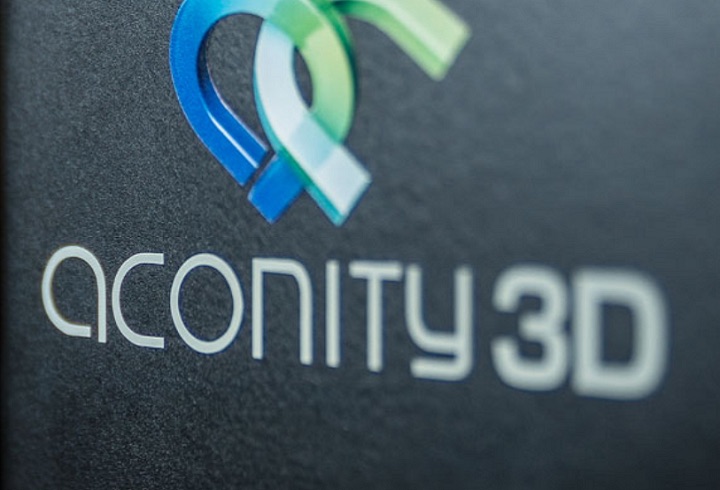