Fabrisonic unisce la fusione del letto in polvere di metallo con la stampa 3D ad ultrasuoni per parti grandi e complesse
L’ azienda Fabrisonic, con sede in Ohio, ha sviluppato un processo UAM (Ultrasonic Additive Manufacturing) unico , che utilizza le onde sonore ultrasoniche per unire strati di lamina metallica insieme in uno stato solido. Il suo processo di stampa 3D ibrido è montato su apparecchiature CNC tradizionali in modo che, una volta uniti gli strati, la macchina ritagli la forma finale. Il suo processo UAM è noto per la sua capacità di creare caratteristiche uniche e geometrie interne complesse, oltre a incorporare sensori in parti metalliche solide e combinare metalli dissimili. Ora, Fabrisonic sta spingendo le cose ancora oltre combinando queste tre caratteristiche e quindi aggiungendo la geometria organica creata attraverso la stampa PBF (Metal Powder Bed Fusion).
Le tecnologie di fusione a letto di polvere stanno “penetrando nei perimetri della vera produzione, e questa accettazione iniziale ha solo alzato il livello collettivo per le prestazioni e la capacità delle tecnologie”. Nel processo PBF , uno strato di polvere metallica viene depositato su una piastra di costruzione e qualcosa, il più delle volte un laser, fonde quindi una sezione trasversale del materiale, prima che venga aggiunta nuova polvere strato per strato fino al completamento della parte.
Sebbene la tecnologia UAM di Fabrisonic sia una buona scelta quando si tratta di stampare componenti di grandi dimensioni con, come accennato in precedenza, strutture interne complesse, sensori incorporati e metalli multipli, non è eccezionale per strutture organiche fini, a causa delle grandi forze necessarie per la creazione un legame. Il rovescio della medaglia, mentre PBF è in grado di stampare motivi organici e delicati, le parti grandi non sono il suo punto di forza. Quindi, Fabrisonic ha combinato i due per ottenere la parte migliore possibile.
Il cliente Fabrisonic senza nome voleva tre cose per questo particolare progetto: geometria organica dell’acciaio inossidabile, transizione di metallo dissimile e sensori incorporati che erano completamente incapsulati nel metallo. Fabrisonic ha visto che combinando PBF e UAM, sarebbe stato in grado di ottenere i modelli organici necessari che potrebbero essere incorporati in grandi strutture metalliche e dare al cliente esattamente ciò che desiderava. I componenti PBF sono stati inviati a Fabrisonic come grezzi grezzi, che sono stati poi inseriti in un dispositivo in modo che potessero essere vincolati per la saldatura, un passaggio necessario per mantenere il substrato in movimento durante le vibrazioni che il processo UAM provoca. L’azienda ha collaborato con EWI per realizzare la struttura di base per il componente.
“La maggior parte dei processi AM basati sulla fusione avrebbe problemi a stampare metalli dissimili su una parte a letto di polvere”, ha scritto in un post il presidente di Fabrisonic Mark Norfolk . “Tuttavia, lo scanner UAM è diverso in quanto può adattarsi a un’ampia gamma di condizioni esterne. Se è presente un substrato metallico liscio, è possibile utilizzare lo scanner UAM “.
La tecnologia sottrattiva di UAM è stata utilizzata per fresare la parte superiore della parte stampata in PBF organico su una superficie uniforme e piana, quindi sono stati stampati strati di foglio di rame e alluminio.
Una volta che Fabrisonic ha stampato i metalli dissimili all’altezza corretta, ha fresato la parte per creare una tasca per il sensore personalizzato. Una volta che il sensore era all’interno, lo scanner UAM è stato nuovamente utilizzato per stampare più strati di rame e alluminio sulla tasca per avvolgerla e una chiusura ermetica, creata da questi strati extra che si legano al metallo esistente, migliora la durata e protegge il sensore in modo da fornire letture più accurate. Infine, Fabrisonic ha macinato tutta la pellicola in più nella forma finale.
“La parte e il processo mostrati sono stati i primi di molti a includere sia UAM che una forma alternativa di AM”, ha concluso Norfolk. “Man mano che Fabrisonic riceve maggiori opportunità per incorporare questa tecnologia unica in nuove applicazioni, i prodotti fabbricati continueranno ad avanzare. Combinando i vantaggi di altre forme di additivo con i numerosi vantaggi di UAM, diversi processi inizieranno a completarsi a vicenda. Chissà quali saranno i prossimi limiti che ingegneri e designer si spingeranno? “
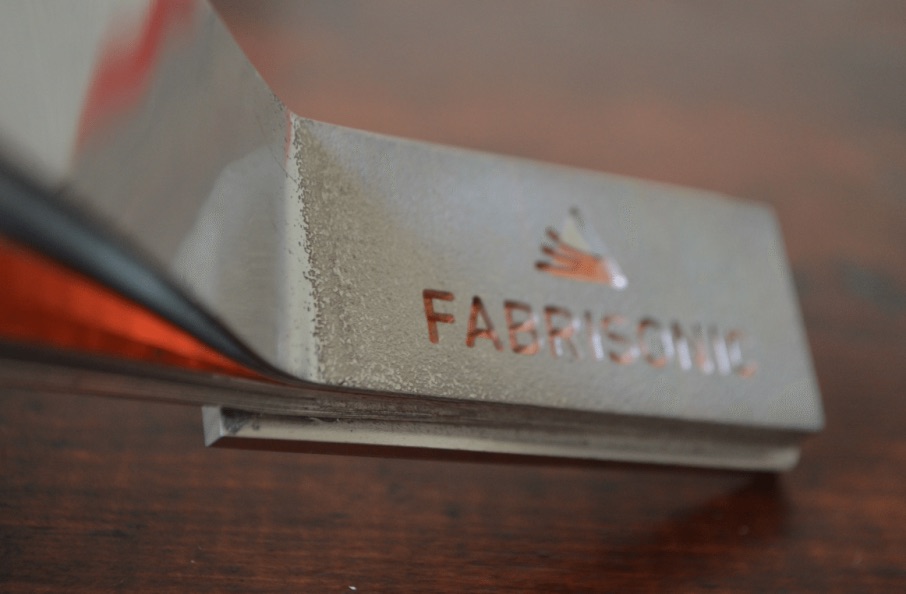