Elemento costitutivo della fabbrica del futuro: gli stabilimenti Ford di Colonia sono nel bel mezzo della più grande trasformazione della loro storia aziendale. Alla fine dell’anno, il primo modello di volume completamente elettrico di Ford in Europa uscirà dalla catena di montaggio di Colonia. Ford non sta solo convertendo i suoi impianti di produzione per il Centro di elettrificazione di Colonia, ma sta anche rendendo i suoi processi di produzione ancora più efficienti e sostenibili, guidando la digitalizzazione e l’Industria 4.0 nel processo. Avanti. Questo video time-lapse mostra come viene creato un supporto per campioni di lamiera nel centro di stampa 3D Ford
Dodici stampanti 3D stampano componenti per veicoli pilota e di piccole serie, ma soprattutto ausili e strumenti per la produzione di veicoli di Colonia : ogni dipendente Ford può richiedere tali ausili per l’installazione tramite l’app. Vengono quindi progettati e stampati digitalmente nel centro di stampa 3D. Per il lancio del primo modello completamente elettrico alla fine dell’anno a Colonia, Ford aumenta così l’efficienza e la qualità dei suoi processi produttivi. Il centro di stampa 3D è un esempio di come lo stabilimento Ford di Colonia stia guidando anche la digitalizzazione e l’Industria 4.0 durante la sua trasformazione nel Centro di elettrificazione di Colonia.
Il processo di stampa 3D esiste da molto tempo alla Ford di Colonia.Già negli anni ’90, gli ingegneri del centro di sviluppo Merkenich hanno iniziato a stampare in 3D componenti per testare veicoli e prototipi. Ford ha stabilito degli standard in questo settore della produzione additiva. Nel 2019, ad esempio, il Ford Research Center di Aquisgrana è stato in grado di produrre la parte metallica più grande mai realizzata utilizzando la stampa 3D. Si trattava di un collettore di aspirazione in alluminio per il motore di un Ford F-150 convertito dalla defunta leggenda del drifting Ken Block.
Nel nuovo centro di stampa 3D di Niehl vengono stampati anche componenti per veicoli pilota e di piccola serie. Ma l’attenzione è altrove: “Qui produciamo principalmente strumenti e strumenti per le nostre aree di produzione”,spiega Nurah Al-Haj-Mustafa, ingegnere di stampa 3D Ford. Si tratta, ad esempio, di misuratori per il controllo delle dimensioni, modelli per l’applicazione del logo Ford, ma anche massicce costruzioni di pinze come attacchi per robot nella costruzione di scocche.
I vantaggi del processo di stampa 3D sono evidenti: “Ogni parte può essere assolutamente unica”, sottolinea Nurah Al-Haj-Mustafa. “Tuttavia, ogni stampa è la stessa in termini di qualità e proprietà.”Inoltre, con piccole quantità si risparmia tempo e denaro, fino all’80 percento rispetto al processo di stampaggio a iniezione convenzionale, in cui la produzione del rispettivo stampo è molto complessa. C’è anche un aspetto della sostenibilità: la stampa 3D richiede molto meno materiale e i granuli triturati possono essere riutilizzati. Insieme alla Rheinisch-Westfälische Technische Hochschule Aachen, il centro di ricerca Ford sta attualmente lavorando a un progetto pilota per il riciclaggio del granulato per la stampa 3D.
Il centro di stampa 3D sta già producendo parti per la produzione del prossimo modello elettronico
La novità e la particolarità del centro di stampa 3D di Niehl è il collegamento in rete con le altre aree e l’accesso a bassa soglia. Ogni dipendente Ford può presentare una domanda tramite un’app. Puoi aggiungere il tuo disegno della parte che desideri o descrivere per cosa ti serve. “Stiamo perseguendo un approccio di start-up con distanze brevi e poca burocrazia “, spiega Oliver Färber, che, in qualità di direttore dello stabilimento di motori, è anche responsabile del centro di stampa 3D. “Le parti richieste dai dipendenti vengono quindi progettate appositamente dal team di stampa 3D e possono quindi essere prodotte molto rapidamente.”
In questo modo, ad esempio, è già stata creata una protezione del bordo della porta che viene attualmente testata sulla linea nell’assemblaggio finale e che potrà essere utilizzata in futuro in altre stazioni, o un ausilio per l’installazione ergonomicamente migliorato per gli airbag. Le parti vengono già stampate in 3D per la futura produzione del primo modello E “made in Cologne”. Attualmente sono in costruzione 1.800 dispositivi di protezione contro gli urti per il nuovo sistema di trasporto delle porte. Garantiscono che le porte non vengano danneggiate durante il trasporto alla linea.
“Sono lieto di poter aprire il centro di stampa 3D prima del lancio del nostro nuovo modello elettronico”, afferma Rene Wolf, amministratore delegato della produzione presso Ford-Werke. “Il processo di trasformazione più completo nella storia dell’azienda a Colonia non riguarda solo la conversione della produzione di veicoli in modelli elettrici. Ford vuole anche promuovere la digitalizzazione e l’Industria 4.0, sottolinea Wolf: “Il centro di stampa 3D è un buon esempio di questo e un altro elemento costitutivo per la fabbrica del futuro, ovvero la nostra visione della produzione futura nel Centro di elettrificazione di Colonia”.
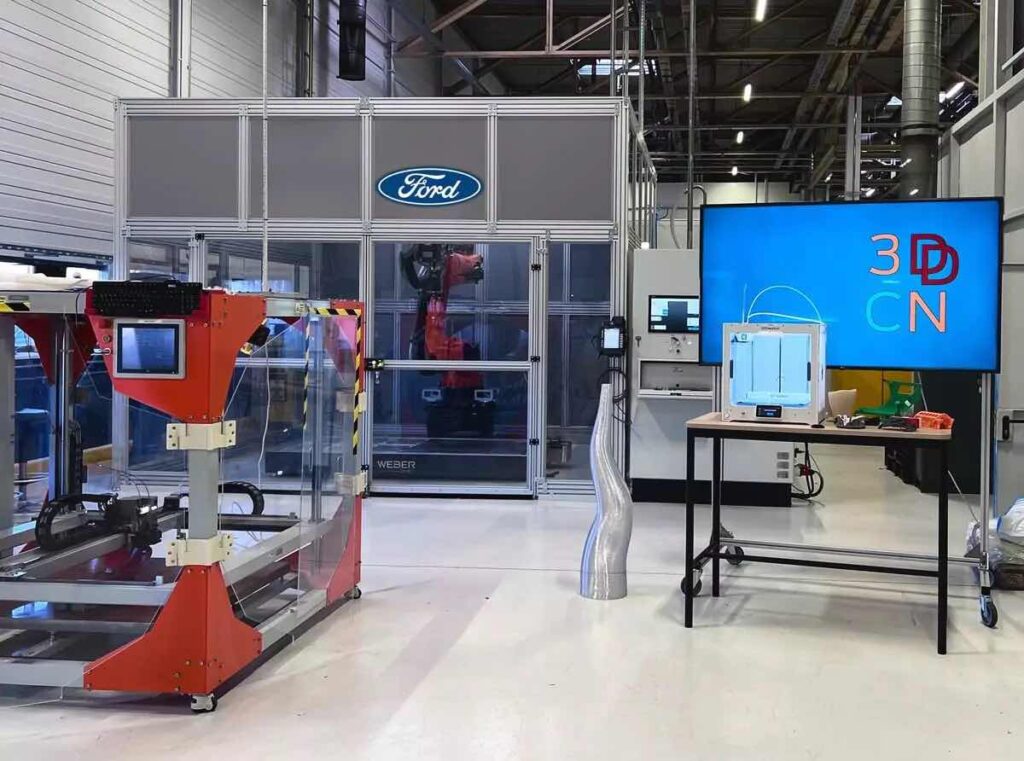