Ford utilizza la tecnologia SLA e SLS di Formlabs per prototipare parti del veicolo elettrico Explorer
Il colosso automobilistico Ford è stato uno dei primi utilizzatori della stampante Form 4 di Formlabs, impiegando questa tecnologia presso il suo stabilimento di Colonia, in Germania. Gli ingegneri di Ford a Colonia hanno accesso anche alle macchine Form 3L e Fuse 1+ 30W, strumenti che stanno rivoluzionando il modo in cui l’azienda prototipa parti complesse per i suoi veicoli elettrici, tra cui il modello Explorer.
Parti prototipate con la tecnologia di Formlabs
Tra le componenti prototipate utilizzando le stampanti 3D di Formlabs si annoverano un complesso connettore di ricarica, una copertura per il connettore, un assemblaggio per lo specchietto retrovisore, parti del cruscotto e elementi esterni del veicolo. Ford ha anche stampato in 3D inserti per stampi a iniezione per produrre due componenti in gomma, fondamentali per il design delle maniglie delle porte, grazie alle loro capacità di smorzamento e isolamento.
Lo stabilimento di Colonia è rinomato per l’assemblaggio del modello Ford Fiesta e, in linea con l’obiettivo di Ford di vendere esclusivamente veicoli elettrici (EV) in Europa entro il 2030, ha avviato la produzione in serie del modello Explorer nello stesso stabilimento. Accanto a questa fabbrica, il centro di sviluppo PD Merkenich, responsabile della progettazione di tutti i veicoli passeggeri per il mercato europeo, è da tempo all’avanguardia nella stampa 3D, avendo adottato la tecnologia SLA già nel 1994, e successivamente ampliando la sua flotta con tecnologie FDM, SLS e di stampa 3D in metallo.
Velocità e flessibilità con Form 4
L’ultima aggiunta alla gamma di stampanti 3D di PD Merkenich è la Form 4, che Ford ritiene abbia migliorato significativamente la capacità degli ingegneri di soddisfare le richieste in meno di 24 ore. Bruno Alves, esperto di produzione additiva e specialista di attrezzature presso Ford, ha affermato: “La Form 4 è davvero molto veloce. Penso che sia la migliore macchina che abbia visto finora in termini di velocità. È un notevole miglioramento rispetto ai modelli precedenti ed è più facile da usare, il che semplifica l’apprendimento per gli operatori del nostro laboratorio e consente di ottenere parti di alta qualità.”
Sandro Piroddi, supervisore del Rapid Technology Center di PD Merkenich, ha aggiunto: “Lavorare con la Form 4 è davvero rivoluzionario. La velocità della stampante cambierà il nostro flusso di lavoro. Possiamo consegnare più parti, il throughput è maggiore e siamo molto più flessibili in caso di richieste urgenti.”
Prototipazione di grandi componenti e test di parti meccaniche
La Formlabs Form 3L, d’altro canto, ha permesso a Ford di prototipare grandi componenti come parti della carrozzeria esterna, mentre la tecnologia SLS del Fuse 1+ 30W è stata impiegata per testare parti meccaniche, come la copertura del connettore di ricarica. Alves ha spiegato: “La Form 3L ci consente di stampare parti grandi, ad esempio, parti della carrozzeria esterna del veicolo. Abbiamo stampato questa calotta dello specchietto per validare un design. La stampa 3D è adatta a questa applicazione perché è veloce e possiamo ottenere una qualità molto buona rispetto alle parti prodotte in serie.”
Per la copertura del connettore di ricarica, Alves ha sottolineato l’importanza dell’uso della tecnologia SLS: “È un design davvero complesso che non possiamo produrre in alcun modo valido. Non possiamo fresare questa parte. Non possiamo usare lo stampaggio a iniezione per produrre solo alcuni campioni. Quindi, la migliore soluzione è stampare in un materiale che possiamo testare fisicamente.”
Combina stampa 3D e stampaggio a iniezione per risultati rapidi
Oltre ai successi ottenuti con la prototipazione, gli ingegneri di Ford hanno anche esplorato la combinazione delle capacità della stampa 3D con lo stampaggio a iniezione per produrre componenti per crash test. Questi componenti devono essere realizzati con lo stesso materiale e processo utilizzato nella produzione di massa, il che significa che erano destinati alla produzione tramite stampaggio a iniezione. Tuttavia, Ford ha visto il potenziale della stampa 3D per accelerare il processo di produzione degli inserti per stampi, riducendo i tempi da mesi a settimane.
Alves ha concluso: “Vediamo un grande potenziale nell’uso di inserti stampati in 3D per lo stampaggio a iniezione, poiché possiamo iterare il design molto rapidamente. Stampiamo cavità nei core e poi possiamo cambiarle nello strumento e iniettare le parti. Normalmente, lo stampaggio a iniezione esterno richiederebbe forse due o tre mesi. Internamente, utilizzando la produzione additiva, possiamo accelerare il processo a due o tre settimane al massimo. Per questo progetto, se avessimo dovuto utilizzare strumenti esterni, sarebbe stato molto più dispendioso in termini di tempo e non saremmo riusciti a consegnare le parti in tempo.”
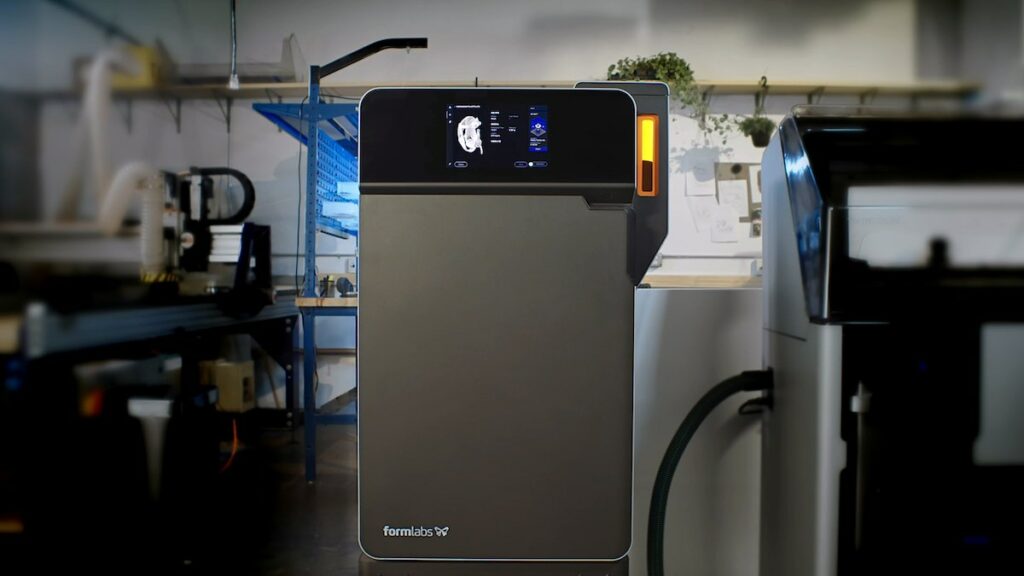