Presso la Iowa State University, un gruppo di ricercatori sta portando avanti un progetto che unisce simulazione digitale avanzata e stampa 3D, con l’obiettivo di migliorare sia le proprietà dei materiali sia i parametri operativi delle tecnologie additive. Il cuore del progetto è l’uso del cosiddetto “gemello digitale”, un modello virtuale capace di replicare in modo dinamico e realistico ciò che accade durante un processo produttivo reale.
Nell’ambito della Materials Genome Initiative, il team ha concentrato i propri sforzi su una specifica tecnica additiva: il Digital Light Processing (DLP), un metodo di stampa 3D che impiega resine fotopolimeriche liquide indurite tramite esposizione controllata alla luce.
Il gemello digitale: oltre la semplice modellazione geometrica
A differenza delle simulazioni tradizionali, spesso statiche e isolate, i gemelli digitali elaborati dai ricercatori di Iowa State sono progettati per interagire in tempo reale con il sistema fisico corrispondente. Questo significa che il modello digitale non si limita a rappresentare la geometria dell’oggetto da stampare, ma tiene conto anche delle interazioni fisiche, chimiche e termiche che avvengono durante la stampa.
Secondo il professor Baskar Ganapathysubramanian, direttore dell’AI Institute for Resilient Agriculture, il gemello digitale funziona correttamente solo se alimentato da dati provenienti in tempo reale dal suo gemello fisico. Questo legame continuo consente al sistema di adattarsi e migliorare la qualità della stampa attraverso cicli iterativi di simulazione e feedback.
Una sinergia tra ingegneria meccanica, AI e manifattura digitale
Il progetto coinvolge diverse competenze interdisciplinari. Il professor Soumik Sarkar, docente di ingegneria meccanica e coordinatore del progetto COALESCE (che sviluppa sistemi cyber-fisici per l’agricoltura di precisione), spiega che la sfida è armonizzare costantemente modelli virtuali e dati reali. In agricoltura, l’obiettivo è gestire piante individuali attraverso robot, droni e sensori; nella stampa 3D, l’analogia è regolare ogni fase del processo additivo sulla base dell’evoluzione del comportamento fisico osservato.
Un altro membro del team, il professor Ming-Chen Hsu, esperto in modellazione computazionale e coinvolto nel Translational AI Center, ha spiegato che uno degli obiettivi principali è rendere questi modelli capaci di evolversi. In passato, le simulazioni numeriche funzionavano come sistemi a senso unico: producevano risultati, ma non erano in grado di adattarsi ai dati reali o di apprendere.
Oggi, l’introduzione dell’intelligenza artificiale nel processo di modellazione consente al gemello digitale di adattarsi alle condizioni operative e di affinare continuamente le previsioni, migliorando così la coerenza tra simulazione e realtà.
Controllo della luce per proprietà differenziate all’interno dello stesso oggetto
Attraverso il controllo selettivo dell’esposizione alla luce, i ricercatori sono in grado di modificare localmente le proprietà del materiale all’interno dello stesso componente. È così possibile creare zone più flessibili o più rigide in una singola stampa, senza dover interrompere o riconfigurare il processo.
Questo tipo di controllo materiale apre nuove possibilità nella progettazione funzionale, ad esempio nella realizzazione di strutture con giunti integrati, o in dispositivi che richiedono comportamenti meccanici variabili a seconda delle sollecitazioni.
Ottimizzazione geometrica e regolazione dinamica dei parametri di stampa
Nella fase attuale del progetto, l’attenzione è concentrata sulla ottimizzazione della geometria dei componenti, ma uno degli sviluppi previsti a medio termine riguarda l’adattamento in tempo reale dei parametri di stampa. Questo sarà possibile grazie a un sistema di controllo retroattivo che riceverà i dati generati dalla simulazione e li utilizzerà per correggere eventuali deviazioni nel processo fisico.
Si tratta di un passaggio importante verso una produzione additiva più reattiva e precisa, in cui la qualità del pezzo finito può essere regolata in base alle condizioni di stampa osservate in corso d’opera.
Un progetto con ricadute che vanno oltre la manifattura
Il potenziale del progetto non si limita alla stampa 3D. Le competenze e gli strumenti sviluppati possono essere trasferiti anche in altri settori, tra cui la salute umana. Secondo Hsu, l’integrazione tra modelli virtuali e dati reali potrebbe essere applicata anche in ambiti biomedicali, come la simulazione del comportamento di tessuti o organi artificiali. Il team ha già sperimentato modellazioni relative al funzionamento delle valvole cardiache, sottolineando l’importanza di sistemi predittivi capaci di adattarsi a parametri biologici variabili.
La simulazione come alternativa ai test fisici su larga scala
Uno dei principali vantaggi del gemello digitale è la possibilità di condurre migliaia di simulazioni virtuali, in parallelo e in tempi molto più rapidi rispetto a quanto sarebbe possibile con prove fisiche. Questa capacità consente di esplorare una vasta gamma di scenari produttivi, valutare l’efficacia di modifiche nei materiali o nei parametri di processo, e ottimizzare rapidamente le strategie operative.
Secondo i ricercatori, questo approccio permette non solo di accorciare i tempi di sviluppo ma anche di aumentare l’efficienza d’uso dei materiali e la qualità dei pezzi stampati, contribuendo a una manifattura additiva più affidabile e sostenibile.
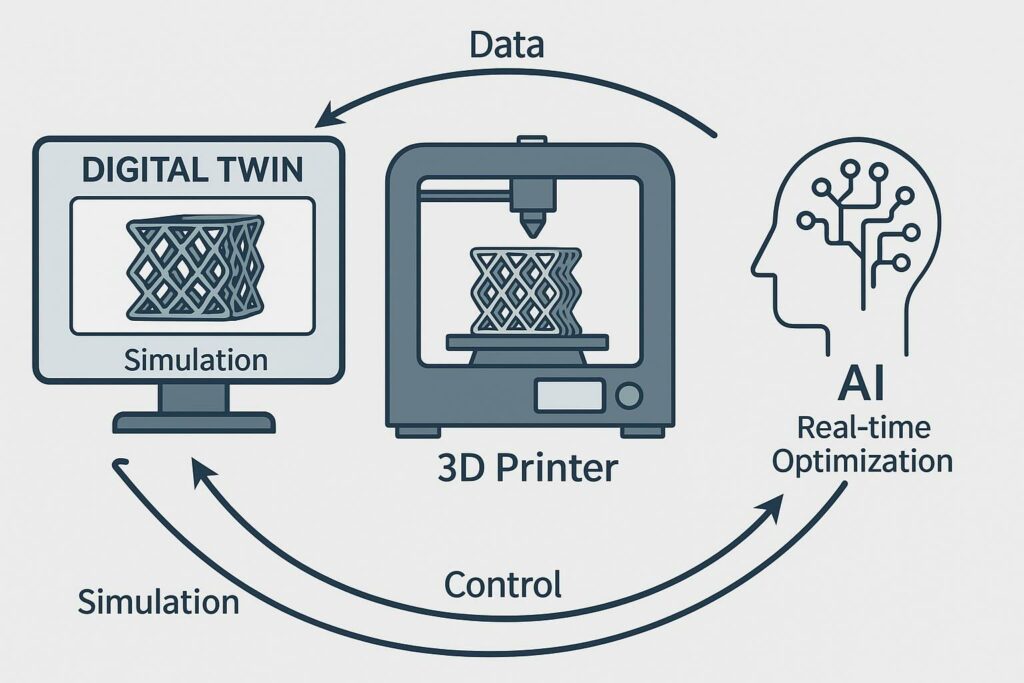