Gravity Pull Systems: soluzione software olistica per la produzione additiva
La start-up svizzera Gravity Pull Systems presenta una nuova soluzione software per la produzione additiva in un comunicato stampa . Secondo il proprio, l’azienda sta perseguendo un approccio olistico e vuole creare una maggiore efficienza dei costi. La soluzione è utilizzata nei settori aerospaziale, automobilistico, automazione e medicale.
Rispetto ai sistemi software consolidati con funzioni single-point individuali, l’approccio alla soluzione olistica della piattaforma software Synoptik consente applicazioni best practice per i processi di produzione additiva industrializzati, dalla pianificazione iniziale al completamento della produzione.
Integrando la funzione Scheduling Optimizer con un Manufacturing Execution System (MES), la modifica dei parametri di processo viene regolata dinamicamente in tempo reale, ad esempio con regolazione flessibile dei tempi di produzione. Il monitoraggio continuo tramite Track & Trace garantisce trasparenza e tracciabilità continue durante l’intero processo di produzione e soddisfa i requisiti di conformità specifici del settore. Allo stesso tempo, l’adeguamento dinamico raggiunge una maggiore redditività, riduce i costi di produzione e ha un effetto duraturo sulla protezione ambientale grazie al minor consumo di materiale.
Il modo in cui Synoptik funziona si basa su modelli di Intelligenza Artificiale altamente complessi, i cui algoritmi calcolano 24 ore su 24, 7 giorni su 7 in tempo reale, eventuali cambiamenti di procedure, parametri di processo, consumo di materiale e orari, li incorporano nei processi di produzione in modo agile e ricalcolano continuamente i costi di produzione. Nei processi di produzione additiva si ottengono risultati concreti per l’allineamento digitale a livello di Industria 4.0 / IIot. Ciò include l’implementazione attiva di un uso efficiente di risorse, materiali ed energia attraverso una produzione sostenibile e il massimo riutilizzo del materiale. Consente il monitoraggio tempestivo dei malfunzionamenti al fine di ridurre al minimo lo spreco di materiale e di generare “al volo” le necessarie istruzioni della macchina e le impostazioni dei parametri.
C’è anche un adattamento efficiente dei processi di produzione, ad esempio nel caso di nuovi ordini con scadenza temporale per i quali la produzione deve essere riallineata senza influire sull’ambiente di produzione esistente.
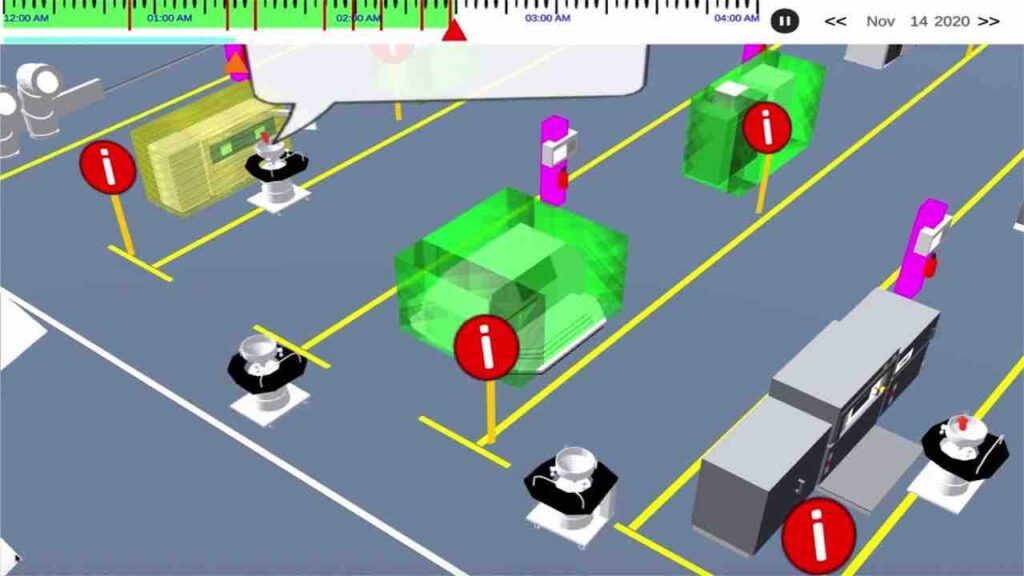