Huntington Ingalls Industries (HII), il maggiore costruttore navale degli Stati Uniti, ha annunciato che Newport News Shipbuilding ha installato un collettore di valvole stampato in 3D su una portaerei. Secondo l’azienda, l’uso di componenti certificati realizzati con stampa 3D potrebbe ridurre i tempi di produzione e migliorare la qualità della manifattura, contribuendo ad accelerare la costruzione e la consegna delle navi alla Marina statunitense.
Un componente dalle dimensioni considerevoli
Il pezzo installato non è solo significativo dal punto di vista tecnico, ma anche per le sue dimensioni: supera il metro e mezzo di lunghezza e pesa oltre 450 kg, dimostrando come la stampa 3D possa essere impiegata anche per componenti di grandi dimensioni.
La produzione del collettore è stata affidata a DM3D Technology, un’azienda specializzata nella deposizione di energia diretta (DED), che collabora anche con NASA e U.S. Army. DM3D ha qualificato oltre 30 materiali per la stampa 3D e può realizzare pezzi fino a tre metri di altezza. La società ha già prodotto ugelli per razzi di grandi dimensioni e utilizza macchine con due o quattro testine di deposizione per gestire geometrie complesse.
Tecnologia avanzata per la produzione additiva
DM3D adotta un processo a circuito chiuso in cui i componenti di grandi dimensioni vengono montati su una tavola rotante, mentre le testine di deposizione vengono angolate per ampliare le geometrie realizzabili. Oltre alla produzione di parti, l’azienda ha sviluppato i propri macchinari e detiene oltre 40 brevetti nel settore. Accanto ai suoi sistemi su larga scala, DM3D integra testine DED su bracci robotici e sistemi a portale chiuso, offrendo anche servizi interni di trattamento termico (HIP), lavorazione CNC, scansione CT e rivestimento. La società è certificata dalla Naval Sea Systems Command (NAVSEA), garantendo così la conformità delle sue soluzioni alle esigenze della Marina.
“Quello che era iniziato come un test si è trasformato rapidamente in un risultato concreto, migliorando l’efficienza nella costruzione navale. I benefici di questa tecnologia andranno ben oltre la portaerei Enterprise (CVN 80), poiché integreremo sempre più la stampa 3D nei nostri processi produttivi”, ha dichiarato Dave Bolcar, vicepresidente dell’ingegneria e progettazione presso Newport News Shipbuilding.
Costi e tempi della produzione navale
Le operazioni e il mantenimento della Marina statunitense ammontano a circa 17 miliardi di dollari all’anno, mentre il piano per acquisire 85 nuove navi potrebbe raggiungere un costo di 1.000 miliardi di dollari. Per dare un’idea, il PIL mondiale stimato è di 95.000 miliardi di dollari e una pila di banconote da 100 dollari pari a quella somma arriverebbe a oltre 1.000 km di altezza.
Uno dei principali ostacoli nella costruzione di nuove unità navali è la carenza di manodopera qualificata e disponibile, oltre ai lunghi tempi di realizzazione. Una portaerei richiede circa otto anni per essere completata, mentre un cacciatorpediniere classe Arleigh Burke impiega da due a tre anni. Questo modello, in produzione dal 1991, costa circa 2 miliardi di dollari per unità, con 74 esemplari già costruiti e 19 in ordine. Tuttavia, solo il 30% delle riparazioni sulle navi viene completato nei tempi previsti, con cantieri che devono affrontare notevoli arretrati.
La stampa 3D potrebbe rappresentare una soluzione a questi problemi, riducendo i tempi di produzione da mesi a settimane e abbassando i costi. Inoltre, la possibilità di velocizzare le riparazioni rende questa tecnologia particolarmente interessante per l’industria navale.
Un’applicazione pratica su una portaerei di ultima generazione
Il componente stampato in 3D è un collettore di distribuzione dei fluidi installato nella sala pompe di una portaerei della classe Gerald R. Ford, attualmente in costruzione. Questa nuova unità, denominata Enterprise, avrà una stazza di 100.000 tonnellate e potrà trasportare fino a 50 aerei e 20 elicotteri. Un elemento distintivo di questa nave è l’impiego di acciaio riciclato proveniente dal precedente modello con lo stesso nome.
La portaerei Enterprise del passato ha avuto un ruolo significativo nella storia della Marina statunitense: attiva negli anni ‘60 in Vietnam, ha partecipato all’invasione dell’Afghanistan ed è stata la prima portaerei nucleare della flotta. Ancora prima, una nave con lo stesso nome ha giocato un ruolo fondamentale nella Seconda Guerra Mondiale, prendendo parte a quasi tutte le principali battaglie navali del Pacifico.
La nuova Enterprise è la prima portaerei progettata interamente con software CAD. Con un equipaggio di oltre 4.600 persone, sarà operativa per diversi decenni, rappresentando un elemento chiave nelle strategie militari degli Stati Uniti.
L’impiego crescente della stampa 3D nella cantieristica navale
Il collettore di valvole stampato in 3D non è un caso isolato. Un’altra portaerei, la Doris Miller, utilizzerà componenti simili. Huntington Ingalls Industries ha dichiarato di aver già installato 55 parti stampate in 3D su diverse unità navali e prevede di produrne altre 200 entro l’anno. Questo dato conferma come la produzione additiva stia trovando un impiego sempre più ampio nella cantieristica, aprendo prospettive interessanti per il futuro della costruzione navale, sia negli Stati Uniti che a livello globale.
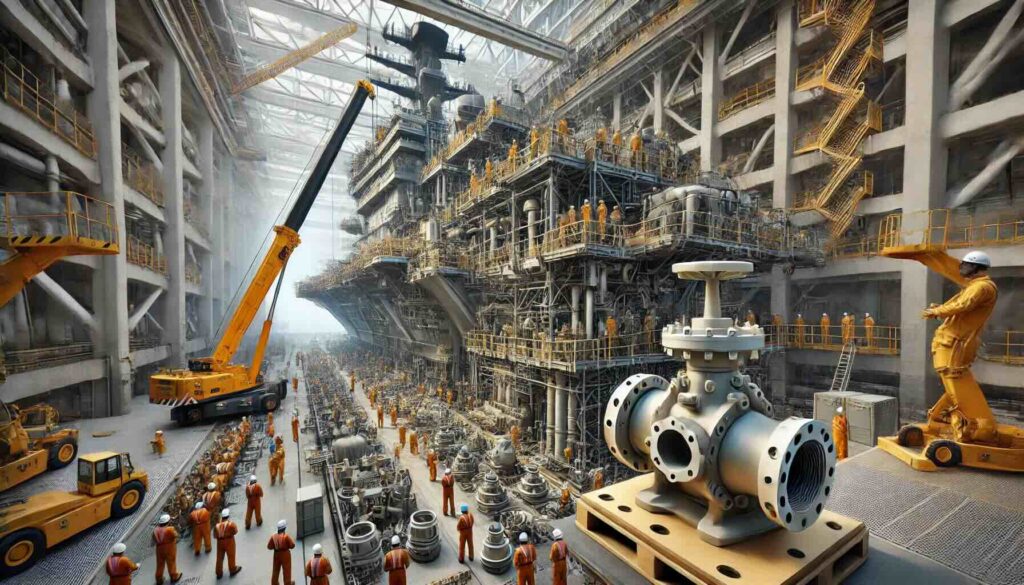
