Contesto e obiettivi di HyFAM
La produzione additiva garantisce libertà geometrica e personalizzazione, ma resta limitata dalla velocità di deposizione strato per strato e dalla necessità di testine di piccolo diametro, che rallentano drasticamente la costruzione di grandi volumi. I processi formativi, come colata e stampaggio, consentono invece di ottenere in tempi rapidi parti massive ma richiedono attrezzature specifiche e hanno vincoli progettuali elevati .
Con il metodo Hybrid Formative-Additive Manufacturing (HyFAM), sviluppato presso il Dipartimento di Civil and Systems Engineering (CaSE) della Johns Hopkins University, si cerca di superare questi limiti, marciando sulla complementarità tra additive e formative .
Principi di funzionamento del processo ibrido
-
Tracciamento dei profili esterni: una testina di stampa 3D a ugello sottile definisce i contorni e le superfici dettagliate, assicurando tolleranze dell’ordine dei decimi di millimetro.
-
Riempimento bulk: la parte interna viene colmata rapidamente con un getto ad alto flusso, simile a un’operazione di colata diretta, riducendo il tempo di costruzione fino a 20 volte nelle sezioni non critiche .
-
Coesione dei materiali: la precisione nella regolazione della viscosità e nelle proprietà di flusso è cruciale per garantire che le porzioni formative e additive si saldino senza difetti strutturali, eliminando bozzature e vuoti interni .
Risultati sperimentali e materiali impiegati
Nel lavoro pubblicato su Advanced Materials, Müller e Brown descrivono test con una vasta gamma di materiali: silicone, argilla, resine epossidiche, metalli e persino cioccolato. Ciascuno di questi supporti ha richiesto un’ottimizzazione dei parametri di flusso per evitare ritiri e deformazioni post-solidificazione .
I primi prototipi dimostrano che, nei pezzi con grandi volumi interni, HyFAM offre un accelerazione di processo compresa tra dieci e venti volte rispetto alla stampa 3D tradizionale, mentre nei componenti ricchi di dettagli il miglioramento si attesta su un fattore di circa due .
Vantaggi tecnologici e operativi
-
Efficienza: riduce il fabbisogno energetico e il tempo macchina grazie al riempimento bulk.
-
Flessibilità: si adatta a materiali con caratteristiche molto diverse, favorendo applicazioni che vanno dall’edilizia alla robotica soffice.
-
Qualità: mantiene alta la risoluzione superficiale e assicura unioni robuste tra le parti formate e quelle stampate, minimizzando gli scarti di produzione .
Aree di applicazione e prospettive future
HyFAM si presta a scenari di produzione di massa personalizzata, dove le parti richiedono sezioni dettagliate alternate a volumi di scarso dettaglio, come moduli edilizi o attuatori per robotica morbida .
Le ricerche in corso puntano a integrare materiali con proprietà meccaniche differenziate all’interno dello stesso componente, aprendo la strada a strutture multi-materiale e a funzioni meccaniche variabili lungo il pezzo. Questo sviluppo potrà estendere l’impiego di HyFAM in settori come l’aerospaziale, l’automotive e l’industria medicale.
Sfide e prossimi passi
La diffusione di HyFAM dipende dal perfezionamento dei sistemi di controllo del flusso e dalla standardizzazione degli indicatori di qualità per le interfacce additive-formative. Occorre inoltre sviluppare software CAD/CAM in grado di generare automaticamente i tracciati di contorno e i pattern di riempimento ottimali, oltre a codificare le ricette di temperatura, pressione e velocità per ogni materiale.
Ruolo dei materiali e controllo del processo
Per ottenere un’unione solida tra le porzioni formate e quelle stampate, il flusso e la viscosità del materiale devono essere calibrati con precisione. I primi test condotti dagli ingegneri guidati dal professor Jochen Müller hanno coinvolto polimeri come silicone e resine epossidiche, argilla tecnica, leghe metalliche e addirittura cioccolato. Ogni supporto ha richiesto una messa a punto dei parametri termici e meccanici per evitare ritiri o punti di scarsa adesione.
Riscontri dagli studi sperimentali
Nathan Brown, dottorando e co-autore dello studio, evidenzia che nei pezzi con ampie sezioni interne HyFAM offre accelerazioni significative rispetto alla sola stampa additiva, mentre mantiene invariata la qualità delle geometrie più complesse. I risultati sono stati esposti sulla rivista Advanced Materials, sottolineando l’efficacia del metodo su prototipi di dimensioni e caratteristiche molto variabili.
Ambiti di utilizzo e prospettive applicative
La flessibilità di HyFAM rende la tecnologia interessante per settori dove si alternano esigenze di definizione superficiale e volumi di massa:
-
Robotica morbida, per realizzare attuatori con gusci dettagliati e riempimenti interni rapidi.
-
Edilizia modulare, per ottenere pannelli strutturali seguendo sia contorni complessi sia porzioni di riempimento che conferiscono rigidità.
-
Componentistica industriale, in cui certe parti richiedono finiture di precisione accanto a ingombri interni non critici.
Sviluppi futuri
Il team di Johns Hopkins mira ora a integrare materiali diversi all’interno dello stesso pezzo, ottenendo proprietà meccaniche variabili a seconda delle zone. Questo consentirà di realizzare componenti multi-materiale e strutture con funzionalità integrate, aprendo a nuovi scenari per l’automotive, l’aerospaziale e il settore medicale.
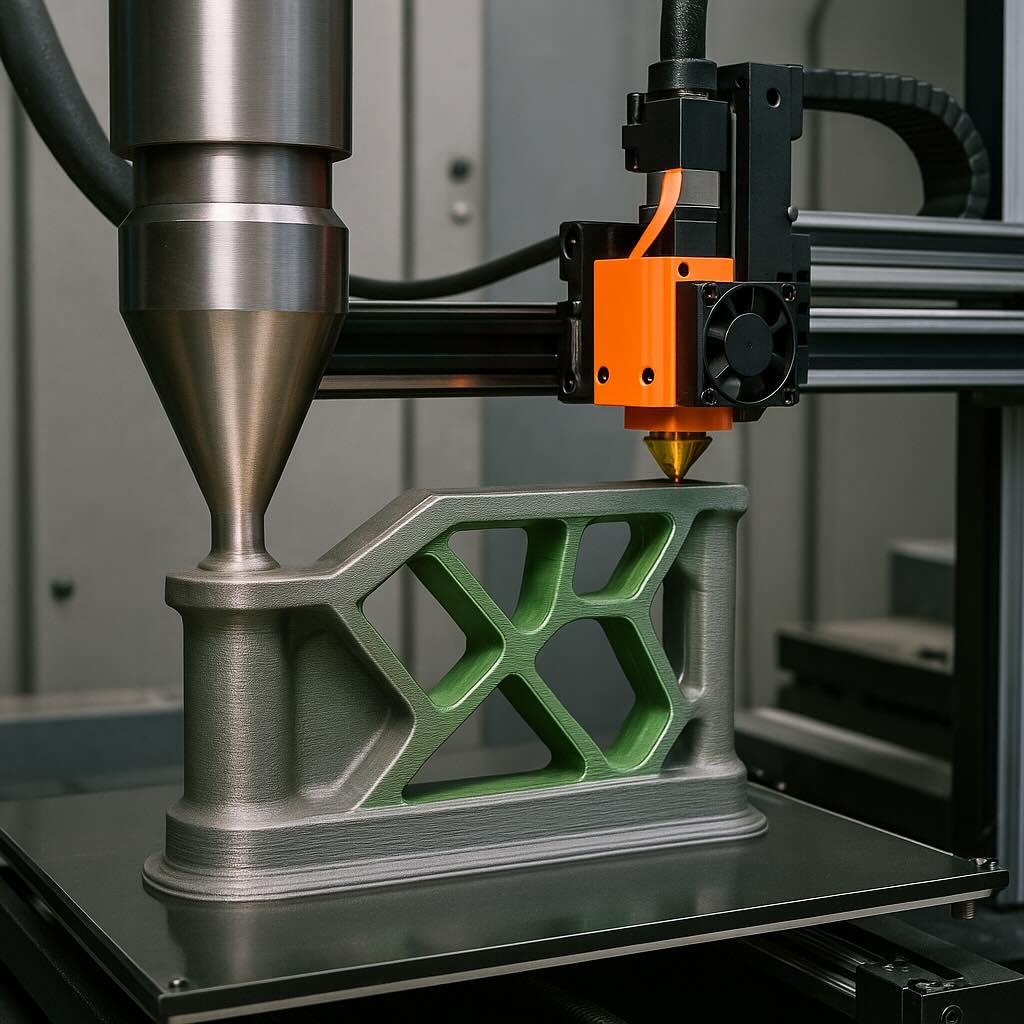