Fusione laser a letto di polvere
Produzione additiva: simulata dall’inizio alla fine
La produzione additiva di utensili mediante un processo di fusione laser a letto di polvere offre numerosi vantaggi: è economica, precisa e consente soluzioni personalizzate. Detto questo, può essere difficile determinare i parametri di processo ottimali, come la velocità di scansione o la potenza del laser. Per la prima volta, i ricercatori del Fraunhofer stanno ora simulando il processo a livello di microstruttura per identificare correlazioni dirette tra le proprietà del pezzo ei parametri di processo selezionati. Per fare ciò, stanno combinando una serie di diversi metodi di simulazione.
La produzione additiva offre numerosi vantaggi. In particolare, è possibile risparmiare energia e materiali e realizzare geometrie di componenti complesse e prodotti personalizzati. Il processo di fusione a letto di polvere laser, o LPBF in breve, è un processo ampiamente utilizzato per la produzione additiva di componenti e strumenti: questo processo colpisce per i suoi brevi cicli di innovazione e l’elevata economicità. Il principio qui è che un letto di polvere spesso fino a 50 micrometri viene riscaldato con precisione millimetrica da un laser. La polvere si liquefa, le particelle si fondono e il pool di fusione si solidifica non appena il laser si sposta. Nelle aree in cui il raggio laser non entra in contatto con la polvere, non si verifica alcuna fusione. Questo processo viene ripetuto numerose volte, facendo crescere il componente in altezza strato dopo strato.
È importante che il componente finito abbia una densità del cento per cento, senza pori e che ogni nuovo strato applicato si leghi saldamente allo strato sottostante. Ciò si ottiene regolando i parametri di processo, come la velocità di scansione e la potenza del laser. La microstruttura dei grani metallici è particolarmente importante per le proprietà meccaniche del pezzo. Questi hanno determinati orientamenti, dimensioni e forme e hanno un notevole impatto sulle proprietà meccaniche, come il modulo elastico del materiale o la tensione di snervamento, ovvero il carico al di sopra del quale il materiale si deforma plasticamente.
Quindi la domanda è: come si controlla il processo in modo tale che la microstruttura risultante sia adatta alle future condizioni di utilizzo del componente? Inoltre, componenti e pezzi sono spesso realizzati con diverse leghe metalliche: acciai, leghe di alluminio, leghe di titanio con varie composizioni e rapporti di miscelazione. Ogni materiale in lega ha proprietà diverse e forma microstrutture diverse. Trovare i parametri e i materiali di processo ottimali e abbinarli tra loro è stato, fino a questo punto, uno sforzo sperimentale e quindi dispendioso in termini di tempo.
Simulare l’intera catena di processo
I ricercatori del Fraunhofer Institute for Mechanics of Materials IWM stanno ora adottando un approccio diverso. “Poiché il processo di fusione del letto di polvere laser sta diventando sempre più complesso a causa di nuovi materiali e requisiti, abbiamo deciso di simulare l’intera catena di processo”, spiega il Dr. Claas Bierwisch, team leader presso Fraunhofer IWM. “Questo ci consente non solo di ridurre al minimo i cicli di tentativi ed errori, ma anche di valutare in modo rapido ed efficace le variazioni nel processo complessivo ed eliminare gli effetti indesiderati durante la produzione”.
La cosa importante qui è che i ricercatori hanno combinato diversi metodi di simulazione. Utilizzando il metodo degli elementi discreti, dapprima simulano come le singole particelle di polvere vengono distribuite nella camera di costruzione con l’ausilio di uno strumento speciale, vale a dire la racla. Successivamente, il modo in cui le particelle di polvere fondono viene simulato utilizzando il metodo dell’idrodinamica delle particelle levigate: vengono calcolate sia l’interazione laser che la conduzione del calore, nonché la tensione superficiale che fa scorrere il fuso. Il calcolo tiene conto anche della gravità e della pressione di rinculo che si verifica quando il materiale vaporizza.
© Fraunhofer IWMCatena di simulazione per modellare il processo LPBF dalla polvere alle proprietà meccaniche
© Fraunhofer IWMSimulazione del processo LPBF con campo di temperatura codificato a colori
La simulazione deve anche descrivere la microstruttura del materiale per prevedere le proprietà meccaniche del materiale. “Per analizzare questa microstruttura, abbiamo incorporato un altro metodo di simulazione, noto come automa cellulare. Questo descrive come i grani metallici crescono in funzione del gradiente di temperatura”, spiega Bierwisch. Questo perché le temperature possono raggiungere i 3.000 gradi Celsius nel punto in cui il laser incontra la polvere, ma a pochi millimetri di distanza il materiale è freddo. Inoltre, il laser si sposta sul letto di polvere a una velocità di diversi metri al secondo. Di conseguenza, il materiale si riscalda molto rapidamente ma poi si raffredda nuovamente in pochi millisecondi. Tutto ciò ha un impatto su come si forma la microstruttura. Il passo finale è la simulazione agli elementi finiti:
“Nell’esperimento possiamo solo studiare il risultato finale, mentre nella simulazione possiamo vedere cosa succede in tempo reale. In altre parole, creiamo una relazione processo-struttura-proprietà: ad esempio, se aumentiamo la potenza del laser, la microstruttura cambia. Questo, a sua volta, influisce in modo significativo sulla tensione di snervamento del materiale. La qualità di questo è completamente diversa da ciò che è possibile in un esperimento”, afferma Bierwisch con entusiasmo. “Puoi rilevare le interrelazioni in modo quasi investigativo.”
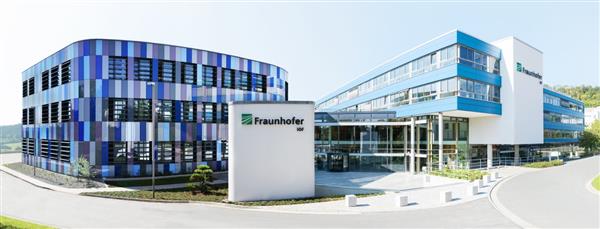