Qualità Affidabile dei Componenti Stampati in 3D
La stampa 3D si sta affermando sempre di più nel settore manifatturiero, con potenzialità notevoli. Questo metodo può essere utilizzato per produrre componenti bionici leggeri destinati all’aviazione, contribuendo alla riduzione delle emissioni di CO2. Il progetto “Enabl3D” è un’iniziativa in cui i ricercatori stanno sviluppando un sistema efficace di garanzia della qualità per questi componenti.
Componenti Aeronautici e la Sfida della Qualità
La produzione di componenti aeronautici tramite stampa 3D rappresenta un progresso significativo, ma la garanzia della qualità è fondamentale per queste parti, particolarmente critiche per la sicurezza. Prima di essere montati su aerei passeggeri o cargo, i componenti devono superare rigorosi controlli di qualità. Un problema risiede nel fatto che i componenti stampati, anche se apparentemente identici, possono presentare piccole variazioni. Questo rende difficile applicare al 100% i risultati dei test effettuati su campioni di materiali ad altri componenti. Le prove distruttive, comunemente utilizzate, non sono una soluzione praticabile a causa del loro elevato consumo di risorse ed energia, e lo stesso vale per tecniche complesse come la radiografia.
Innovazione nella Misurazione della Durezza
Una possibile soluzione a questo problema è rappresentata dall’impiego di un metodo di test non distruttivo sviluppato da Imprintec GmbH in collaborazione con l’Istituto Fraunhofer per le Tecnologie di Produzione Additiva (IAPT) e VisiConsult GmbH, nell’ambito del progetto “Enabl3D”. Questo approccio consente di registrare le proprietà qualitative dei componenti finiti attraverso controlli con liquidi penetranti, monitoraggio del processo e tomografia microcomputerizzata, garantendo risultati rapidi e affidabili.
Il Contributo del Robot Industriale a 6 Assi
Nel sottoprogetto “Integrazione della Tecnologia di Misurazione della Durezza”, il team ha collaborato anche con esperti dell’Istituto Fraunhofer per l’Ingegneria della Produzione e l’Automazione (IPA). L’obiettivo era integrare una testa di misurazione con un robot industriale a 6 assi, in modo da automatizzare il processo di controllo qualità. “Abbiamo condotto i primi test e studi di fattibilità per integrare la testa di misurazione nella produzione in serie, utilizzando il robot”, spiega Lukas Werdin, scienziato del Fraunhofer IPA.
Una delle sfide principali riguardava la precisione: mentre in un laboratorio di prova il sistema di misura è statico, l’impiego di un braccio robotico può introdurre imprecisioni. I ricercatori hanno quindi valutato se tutti i punti di misurazione desiderati sul componente potessero essere raggiunti dal robot e con quale livello di precisione fosse possibile ripetere le misurazioni. “La nostra priorità era garantire la posizionabilità, la precisione di posizionamento e la qualità delle misurazioni”, sottolinea Werdin.
Conclusioni Positive per la Prima Applicazione
I risultati dei test sono stati incoraggianti. Il robot è stato in grado di raggiungere tutti i punti di misurazione previsti e la qualità delle misurazioni è risultata eccellente. “La deviazione è stata minima, nell’ordine di una cifra percentuale, un risultato molto positivo per una prima applicazione con un robot”, conclude Werdin.
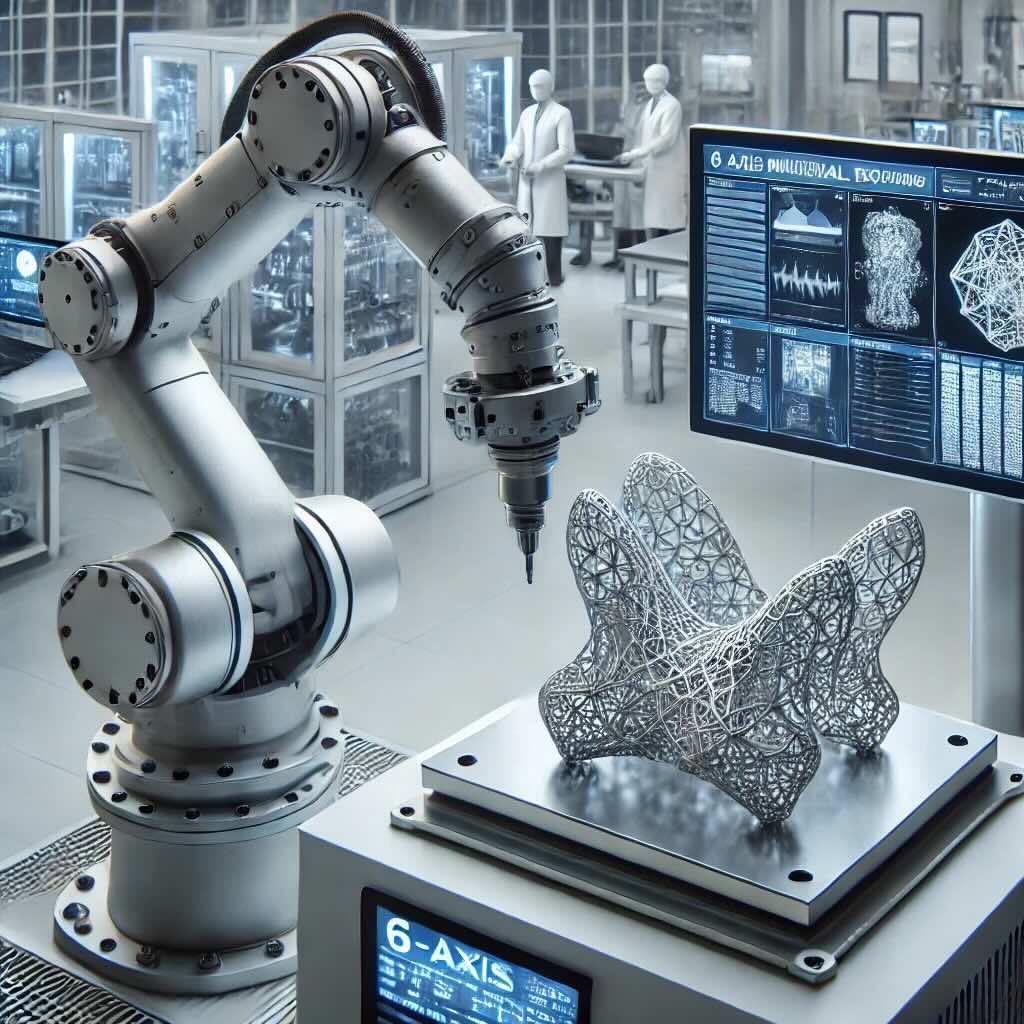