Introduzione al progetto MADE3D
Il Laboratorio Nazionale per le Energie Rinnovabili degli Stati Uniti (NREL), finanziato dall’U.S. Department of Energy tramite l’ufficio Wind Energy Technologies, ha portato a termine un programma quinquennale di ricerca denominato MADE3D (Manufacturing and Additive Design of Electric Machines by 3D Printing). L’iniziativa ha coinvolto centri di ricerca come l’Oak Ridge National Laboratory e il NASA Glenn Research Center, insieme all’industria rappresentata da Bergey WindPower. L’obiettivo è stato ripensare la progettazione e la produzione di generatori per turbine eoliche, sfruttando metodi di stampa 3D multimetallo e multimateriale per contenere l’uso di terre rare e ridurre peso e costi.
Componenti stampati e prototipi realizzati
All’interno del progetto sono stati sviluppati due filoni principali: un prototipo da 15 kW destinato a generatori onshore di piccola taglia e un modello concettuale da 15 MW pensato per impianti offshore. Per il prototipo da 15 kW, realizzato in collaborazione con Bergey WindPower, il team ha impiegato magneti polimerici e nuclei in acciaio elettrico prodotti mediante additive manufacturing. Le prove sperimentali sul banco di prova hanno evidenziato una corrispondenza inferiore al 10 % tra valori di coppia simulati e misurati, confermando la validità del processo.
Sul fronte dell’unità offshore, la ricerca ha introdotto nuclei rotore a flusso radiale ottimizzati, conduttori personalizzati e magneti con composizioni ibride: sinterizzati tradizionali affiancati a magneti polimerici senza disprosio. Questo approccio ha permesso di alleggerire il rotore fino al 35 % e le parti in acciaio elettrico del 20 % rispetto a generatori convenzionali, con una riduzione dei costi dei materiali magnetici stimata in quasi il 9 %.
Strumenti di ottimizzazione basati sul machine learning
Un elemento chiave del programma è stato lo sviluppo del tool MADE3D‑AML, un motore di ottimizzazione topologica che utilizza modelli surrogate basati su machine learning. A differenza dei metodi tradizionali a elementi finiti, questa soluzione accelera i cicli di progettazione di oltre mille volte, permettendo di esplorare in modo rapido configurazioni che bilanciano coppia, flusso magnetico e massa attiva. Gli ingegneri hanno potuto testare superfici magnetiche asimmetriche, avvolgimenti e configurazioni multimateriale con tempi di calcolo ridotti da giorni a minuti.
Innovazioni materiali e processi di stampa
Oltre alla modellazione, il team ha messo a punto processi di stampa avanzati:
-
Binder jetting e selective laser melting per produrre componenti in acciaio Fe₃Si ad alta saturazione magnetica;
-
Additive overmolding per inglobare magneti polimerici e laminati di statore senza necessità di supporti esterni;
-
Utilizzo di ULTEM 1010 e poliammidi per realizzare rivestimenti isolanti stampati direttamente sull’avvolgimento.
Queste tecniche hanno consentito di ottenere parti prive di cricche, con caratteristiche elettriche e meccaniche che rispondono alle specifiche imposte dalle applicazioni eoliche.
Impatto sul settore e prospettive di adozione
I risultati di MADE3D si inseriscono nella strategia del DOE per raggiungere 30 GW di capacità eolica offshore entro il 2030. Le progettazioni aperte e i report tecnici pubblicati da NREL sono diventati fonte di ispirazione per aziende come GE Renewable Energy, che ha recentemente inaugurato un centro di ricerca dedicato alla stampa 3D di torri eoliche, e per realtà emergenti che studiano l’impiego di componenti stampati per ridurre i costi di logistica e assemblaggio.
L’uso di magneti a basso contenuto di terre rare rappresenta un vantaggio strategico per mitigare rischi legati alle catene di approvvigionamento globali, mentre la possibilità di trasferire la manifattura direttamente presso i porti offshore semplifica la movimentazione di pezzi di grandi dimensioni. Inoltre, l’approccio multimateriale apre la via a generatori che integrano direttamente sensori o sistemi di raffreddamento interno.
Sguardo alle evoluzioni future
Il percorso intrapreso da MADE3D prosegue con ulteriori sfide: espandere il range di materiali stampabili, validare processi su scala industriale e integrare strumenti di intelligenza artificiale per la manutenzione predittiva. In parallelo, istituti come Oak Ridge stanno approfondendo l’uso di leghe nitride e sistemi a memoria di forma per realizzare macchine in grado di autoregolarsi in condizioni di carico variabile.
Nel complesso, la combinazione di ottimizzazione computazionale, additive manufacturing e innovazioni nei materiali promette di trasformare il ciclo vita dei generatori eolici, dall’ideazione alla dismissione, rendendo l’energia eolica più sostenibile e accessibile.
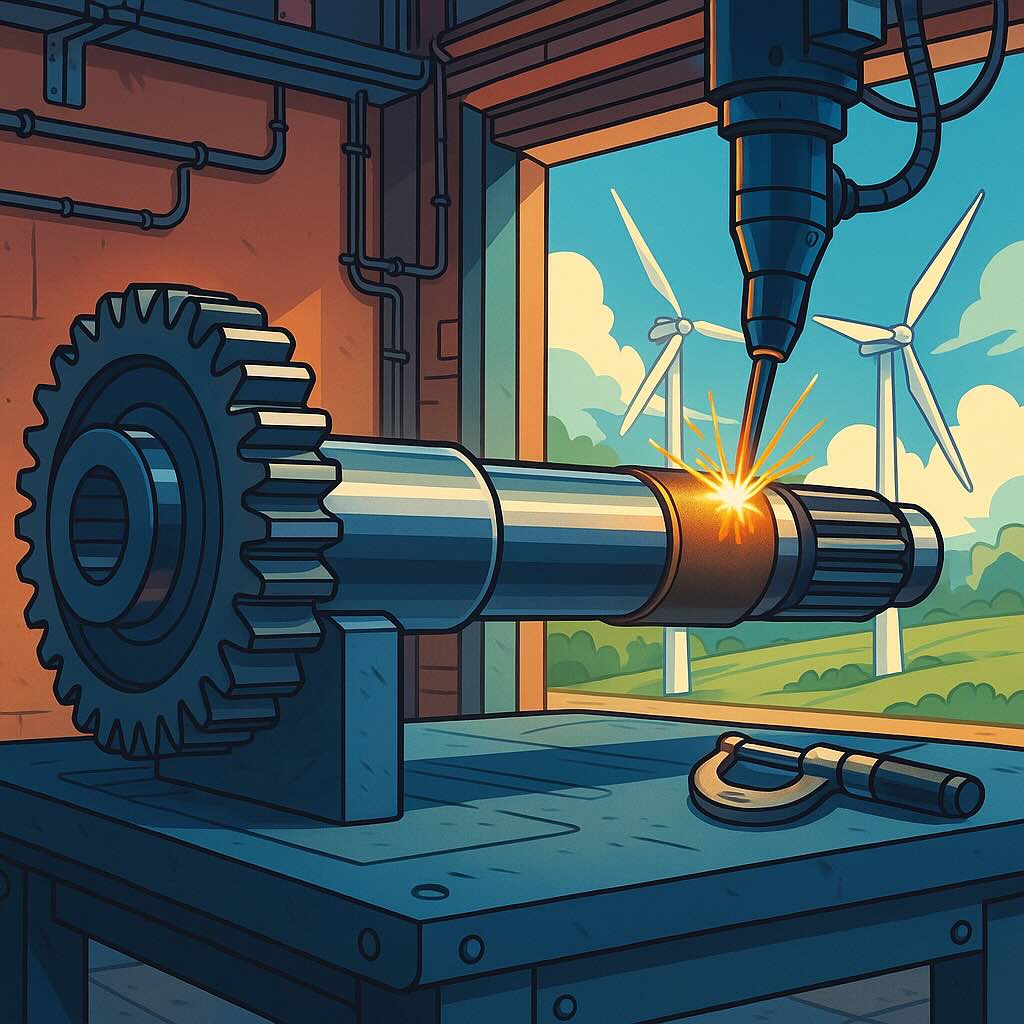