Tecnologia di stampa 3D e materiali funzionali
Un gruppo di ricerca del Korea Advanced Institute of Science and Technology (KAIST) ha elaborato una piattaforma di e-tessuti ottenuta tramite stampa 3D a diretto getto d’inchiostro (Direct Ink Writing). Il procedimento sfrutta inchiostri conduttivi contenenti nanotubi di carbonio multi-parete (MWCNT) e polimeri a base di stirene-butadiene-stirene (SBS), forniti da Kraton Polymers, per disporre elettrodi e sensori direttamente sul tessuto. La scelta di questo copolimero garantisce al materiale una flessibilità meccanica elevata, essenziale per l’adattamento ai movimenti del corpo durante le esercitazioni in ambienti operativi reali.
Integrazione di sensori e interconnessioni elettriche
Gli inchiostri a base di MWCNT, prodotti da aziende specializzate come Cabot Corporation, assicurano una conducibilità stabile anche dopo migliaia di cicli di deformazione. Oltre ai sensori di deformazione, il team ha sviluppato inchiostri a base di polveri d’argento e polistirene per creare interconnessioni verticali tra strati di tessuto, consentendo sistemi multistrato ad alta densità funzionale. Tale configurazione rende possibile la stampa diretta di componenti elettrici in più strati, integrando sia la rilevazione di dati biomeccanici sia la trasmissione dei segnali senza il ricorso a cablaggi tradizionali.
Prove sperimentali sul campo
Durante i test, i ricercatori hanno applicato i sensori su zone strategiche delle uniformi – spalle, gomiti e ginocchia – monitorando in tempo reale posture e movimenti durante esercizi come corsa, flessioni e rotazioni del busto. I sensori di deformazione hanno riportato valori di estensione fino al 102 % senza subire degradazione, mantenendo precisione dopo oltre 10.000 cicli di sollecitazione. In un’ulteriore fase, è stata testata una maschera intelligente in grado di analizzare il ritmo respiratorio del soldato, mentre dei guanti dotati di sensori e circuiti integrati hanno riconosciuto oggetti tramite algoritmi di machine learning, riconducendo superfici particolari attraverso variazioni di conducibilità e pattern tattili.
Obiettivi applicativi e sostenibilità produttiva
Major Park Gyu-soon, che ha coordinato il progetto nella veste di dottorando presso KAIST, ha sottolineato come il sistema miri a offrire addestramenti personalizzati in base al ruolo, all’arma e alle condizioni del contesto operativo. L’utilizzo di tecniche additive permette di ridurre i costi di produzione mantenendo scalabilità per una distribuzione su larga scala alle forze armate. Dal punto di vista economico, la stampa 3D di componenti elettronici direttamente sui tessuti elimina fasi di assemblaggio e cablaggi esterni, aprendo la strada a uniformi “intelligenti” prodotte in serie con investimenti contenuti.
Prospettive nel settore della difesa
Il lavoro è descritto nei dettagli su npj Flexible Electronics, rivista che copre i progressi nell’elettronica indossabile. Il progetto ha visto la collaborazione di esperti in nanotecnologie, ingegneria dei materiali e informatica, con l’obiettivo di trasferire rapidamente i risultati in applicazioni operative. In futuro, lo sviluppo potrà estendersi a sensori biometrici per il monitoraggio dello stress fisiologico e a tessuti in grado di generare energia dai movimenti grazie a nanogeneratori piezoelettrici.
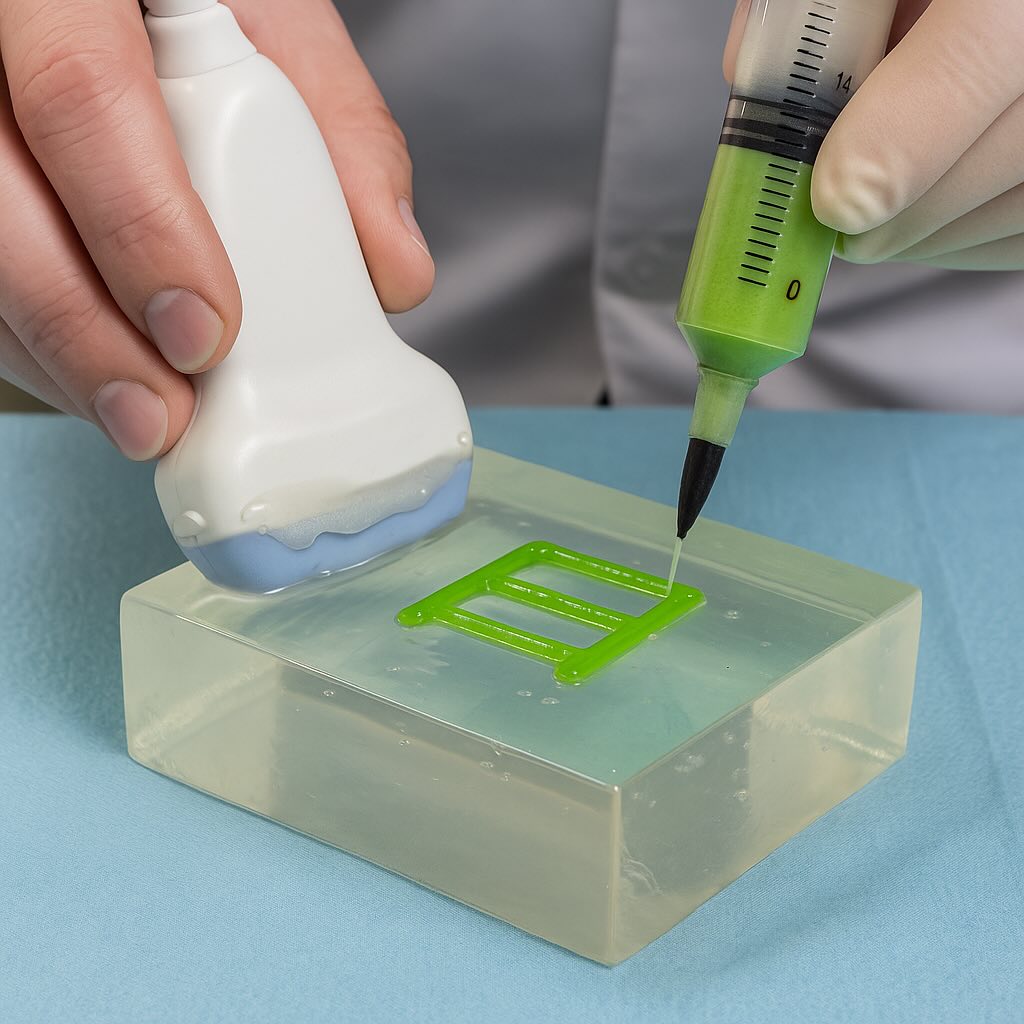