Innovazioni nella stampa 3D dei metalli con tecnologia CMT
La stampa 3D dei metalli tramite arco elettrico sta acquisendo un ruolo sempre più significativo nella produzione di componenti metallici. In particolare, il processo additivo Near-Net Shape, che utilizza il filo di saldatura, permette di costruire oggetti tridimensionali complessi strato dopo strato. Questo metodo trova applicazione principalmente nei settori dell’ingegneria impiantistica, dell’aeronautica, della costruzione di utensili e nella progettazione leggera, dove sono richieste geometrie complesse e un’elevata quantità di materiale asportato.
Controllo avanzato con CMT Additive Pro
Leonhard Reiter, ingegnere nel reparto ricerca e sviluppo di Fronius, spiega: “Con le nostre funzioni CMT Additive Pro, sviluppate specificamente per la produzione additiva—come la correzione della potenza e lo stabilizzatore di deposizione che mantiene costante la velocità di deposizione—possiamo controllare con precisione la potenza erogata. Questo ci consente di regolare l’altezza e la larghezza del cordone di saldatura secondo le necessità”.
Vantaggi nella produzione e nella logistica
Uno dei principali benefici della stampa 3D in metallo è la riduzione dei cicli produttivi. I processi additivi non solo facilitano una rapida prototipazione, ma permettono anche una produzione just-in-time. Ciò riduce la dipendenza da fornitori esterni e diminuisce i costi legati allo stoccaggio.
Sviluppo di standard europei per la stampa 3D metallica
Fronius, insieme a partner come MIGAL.CO e TÜV SÜD Industrie Service GmbH, sta lavorando attivamente allo sviluppo e alla qualificazione di standard per la stampa 3D dei metalli in Europa. Partecipando alla qualificazione di un prototipo di recipiente a pressione realizzato additivamente, viene verificata l’applicabilità della norma prEN 13445-14.
Importanza delle normative nella sicurezza
Il Dr. Ing. Kati Schatz di Linde Engineering sottolinea: “Nella bozza della norma prEN 13445-14 e nella già pubblicata DIN/TS 17026, viene considerata l’intera catena del valore, inclusi tutti i dettagli del monitoraggio. Questo garantisce che i requisiti di sicurezza fondamentali definiti nella Direttiva sulle attrezzature a pressione 2014/68/UE siano soddisfatti”. Schatz aggiunge che tutti i dettagli sono inclusi, in particolare quelli relativi ai materiali, alla progettazione, alla qualificazione del processo additivo, alla produzione, al collaudo, all’accettazione e alla documentazione. “La procedura non differisce molto da quella dei recipienti a pressione prodotti convenzionalmente. Anche senza l’effetto presuntivo di una norma armonizzata, la specifica può comunque servire da guida per tutti coloro che partecipano al processo di produzione additiva delle attrezzature a pressione”.
Sostenibilità ambientale nella produzione additiva
L’ingegnere Robert Lahnsteiner, CEO di MIGAL.CO, evidenzia un aspetto ambientale significativo: “Un tema importante, con rilevanza per il clima, è l’impronta di CO₂ del filo di saldatura. La nostra è di 3,8 kg di CO₂ per chilogrammo di alluminio, meno di un quarto della media internazionale”.
Monitoraggio e controllo dei processi con tecnologie avanzate
L’integrazione di sensori avanzati e soluzioni software, come Fronius WireSense e WeldCube, consente di monitorare e regolare con precisione i processi di saldatura. Questo garantisce alta qualità e ripetibilità nei componenti prodotti.
Qualità garantita attraverso certificazioni
Manfred Schörghuber, direttore R&D di Fronius, afferma: “Oltre alle specifiche di saldatura, la qualità costante dei componenti realizzati con la produzione additiva è assicurata da certificati dei materiali e qualifiche degli operatori”.
Verifiche tecniche sui materiali prodotti
Martin Boche, ingegnere presso TÜV SÜD, dichiara: “Abbiamo dimostrato che i requisiti meccanico-tecnologici per il materiale prodotto con la produzione additiva e le connessioni ibride sono soddisfatti attraverso test sulla composizione chimica, prove di trazione e flessione eseguite perpendicolarmente alla direzione di deposizione. Inoltre, abbiamo effettuato esami metallografici sui punti di inizio e fine, così come sulle connessioni ibride”.
Prospettive future della stampa 3D in metallo ad arco
Con il continuo avanzamento tecnologico e la crescente standardizzazione, la stampa 3D in metallo ad arco è destinata a svolgere un ruolo centrale nel settore manifatturiero moderno.
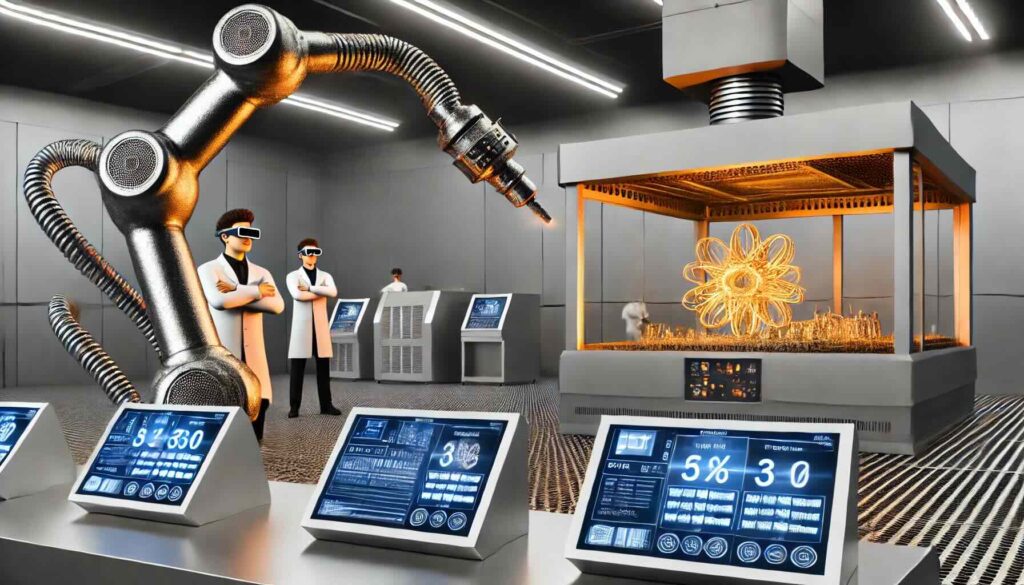
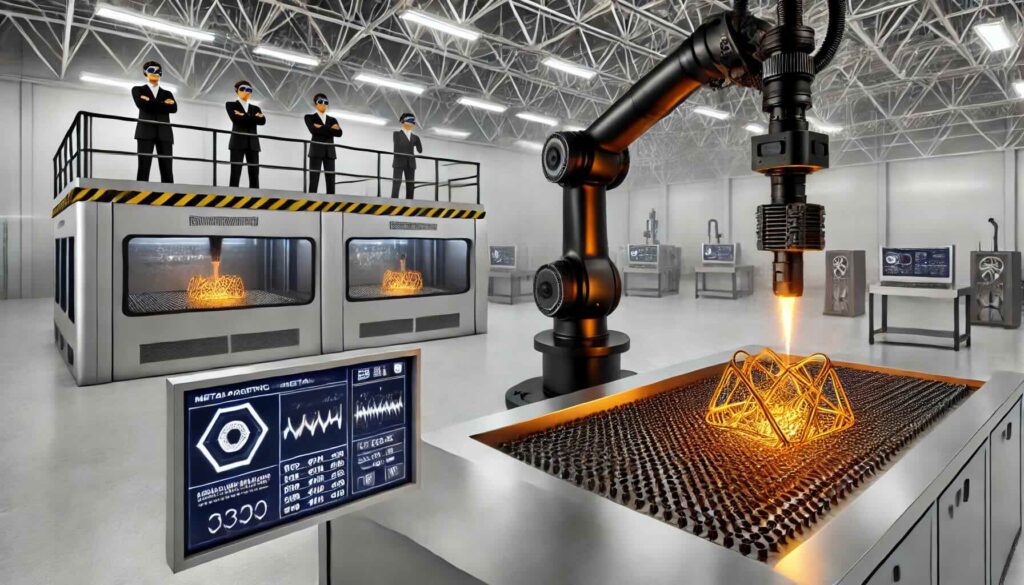