Dopo aver lavorato sotto il radar per molti anni, VELO3D , con sede in California, è finalmente emersa come una delle startup più promettenti nell’agosto 2018 con il rilascio della sua stampante 3D in metallo Sapphire. La società ha sviluppato un processo di stampa in metallo con maggiore libertà di progettazione nel metallo, in grado di stampare geometrie complesse al di sotto di 45 gradi e ridurre i costi delle parti dal 30 al 70 percento, il che renderebbe possibili più parti stampate in 3D. Basato sulla tecnologia Intelligent Fusion dell’azienda , il sistema presenta meno vincoli rispetto ad altre stampanti, diventando l’unico sistema laser in metallo con capacità priva di supporto e un flusso di lavoro integrato end-to-end, che molti considerano cambieranno per sempre la stampa 3D in metallo.
Ora, grazie a un webinar gratuito ospitato questo mese dal responsabile tecnico delle applicazioni della società, Brian Spink, l’azienda sta portando ingegneri e specialisti della stampa 3D in metallo attraverso il processo di progettazione del sistema Sapphire di VELO3D , discutendo le considerazioni da tenere a mente nella scelta dei pezzi per la loro stampante, compresa una profonda conoscenza delle linee guida di geometria angolare e flottante, nonché il loro meccanismo avanzato di ricopertura senza contatto (un’invenzione davvero rivoluzionaria).
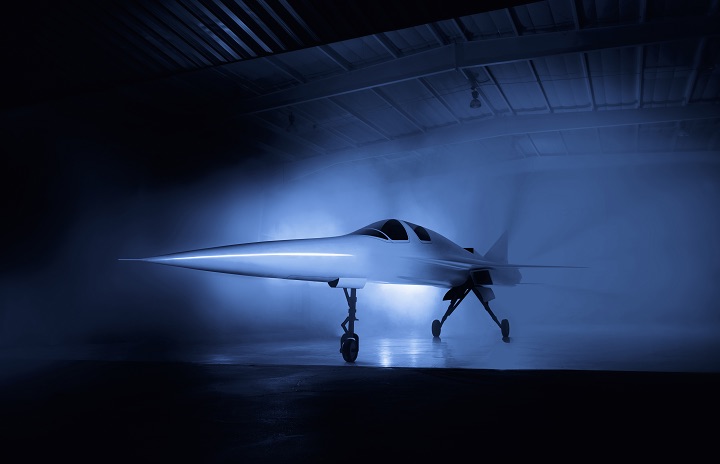
“La progettazione di componenti per la stampante Sapphire di VELO 3D ha meno restrizioni rispetto ad altri sistemi. In effetti, potrebbe non essere necessario riprogettare le parti in quanto la tecnologia può stampare senza supporto in una gamma più ampia di geometrie e ha superato la regola dei 45 gradi, con un tasso di successo della prima stampa del 90 percento e parti che soddisfano e superare i requisiti di densità di produzione del metallo oltre il 99,9 percento “, suggerisce Spink.
La stampante Sapphire di VELO3D è un sistema AM di nuova generazione in metallo a fusione laser progettato per la stampa 3D in metallo avanzata . Mentre i tradizionali sistemi di stampa 3D richiedono spesso supporti per qualsiasi geometria inferiore a 45 gradi, Sapphire di VELO3D consente in modo univoco agli ingegneri di realizzare progetti con sporgenze inferiori a 10 gradi e grandi camere d’aria fino a 40 mm senza supporti. Alcune applicazioni possono anche essere stampate flottanti nel letto di polvere, costruite strato per strato in Inconel 718 (IN718) o in lega di titanio(Ti6Al4V), utilizzando due potenti laser da kW e un rivestimento brevettato senza contatto. La tecnologia è stata progettata da zero pensando alla produzione di grandi volumi con un involucro di costruzione di 315 mm di diametro per 400 mm di altezza. Inoltre, e per massimizzare la produttività, Sapphire offre anche una metrologia di processo in situ integrata che consente il controllo del pool di melt loop a circuito chiuso di prim’ordine.
Sistema di fusione laser zaffiro
Lo sviluppo è davvero un punto di svolta. In genere, gli utenti dovevano sottoporsi a un processo di riprogettazione iterativo al fine di realizzare parti adatte alla produzione additiva, il che significa uno sforzo di progettazione aggiuntivo. Durante il webinar, l’ esperto ha spiegato che non è necessario alcun supporto per sporgenze superiori a 15 gradi per entrambi i materiali: Inconel e Titanio. Di solito, i supporti devono essere progettati in anticipo per evitare che le parti si deformino e quindi, una volta che la parte è stata costruita, devono essere rimosse, il che porta a costose post-elaborazioni.
“In generale, il modo in cui le persone affrontano lo stress residuo lungo la parte è semplicemente aggiungere materiale di supporto. Supporta l’aiuto, ma non sono l’unico modo per costruire e introducono anche altri problemi, come limitare o ancorare la parte verso il basso per evitare che si deformi e funga anche da sincronizzazione energetica “, ha detto Spink. “Ci sono alcuni svantaggi di questi supporti, motivo per cui VELO3D non vuole includerli, consentendo l’esecuzione di alcuni processi unici.”
VELO 3D controlla il comportamento termico / meccanico della geometria attraverso hardware proprietario e controlli di processo avanzati. Il sistema riconosce molte più geometrie uniche, in particolare utilizzando regole basate sull’angolo per applicare processi unici alle geometrie, per evitare un maggiore controllo e avere un’esperienza più completa senza abbattere.
“Un altro ulteriore livello di controllo introdotto da VELO3D è un controllo più attento per determinati parametri di processo”, ha continuato Spink. “Abbiamo un paio di sensori che monitorano il pool di melt in tempo reale e utilizzando questi dati possiamo ricreare un circuito chiuso in grado di regolare i parametri laser, anche in tempo reale, per aiutare a controllare la coerenza del pool di melt ed evitare rotture “.
Uno scambiatore di calore realizzato in Inconel
“In alcuni di questi casi, stiamo prendendo qualcosa che non potrebbe essere fatto con nessun altro processo AM e lo stiamo abilitando sul sistema VELO3D, ad esempio con chiusure a cupola in cui le cavità interne hanno geometrie di tipo molteplice che possono essere stampate utilizzando la tecnologia dell’azienda senza aggiungere supporto.”
Secondo Spink, essere in grado di stampare la funzione senza supporti dipende fortemente dall’angolo normale alla superficie, ma anche da altri fattori avversi che determinano le regole basate sull’angolo, compresa la crescita del margine di crescita del in parte, l’ ombra di strati propagati dalla caratteristica geometrica, l’ angolo di incidenza maggiore rispetto all’angolo di crescita e altre caratteristiche geometriche oculari che influenzano il modo in cui l’energia viene assorbita e il comportamento del pool di fusione localmente.
“Ogni geometria è unica, quindi è difficile generalizzare una regola esatta per un numero infinito di parti, ecco perché stiamo provando a fornire agli utenti un paio di proxy e una manciata di regole su geometrie semplici in modo che possano interpolarle su altre geometrie con cui stanno vivendo. “
Lo specialista ha spiegato come gestire le forme geometriche piane e coniche, suggerendo, tramite un grafico di “Probabilità di rottura”, se e quando la geometria deve essere vincolata. Le linee guida angolari per le forme coniche – che sono semplici proxy – rivelano che una superficie conica in crescita verso l’esterno (convessa) ha una maggiore probabilità di rottura una volta che supera un’altezza piena di 5 mm, il che significa che è abbastanza rischiosa e a 10 mm si comporta a un rischio molto elevato. Spink suggerisce che in questi casi le forze di base stanno lavorando insieme e possono portare a rotture: stress residuo globale che sta riducendo ogni strato tirando la geometria verso l’interno verso la massa locale, e l’altro è un processo cutaneo che forma un anello attorno al geometria che si contrae e vuole tirarla verso l’interno.
Altrimenti, una geometria di superficie conica (concava) crescente verso l’interno con un angolo di 10 gradi è molto stabile e non richiede supporto perché la probabilità di rottura è molto bassa.
Esempio: puntone e girante mock up
Per capire meglio come funzionano le geometrie coniche in VELO3D, Spink suggerisce di esaminare un esempio di puntone e girante, che ha un percorso di flusso interno critico quando è orientato in una forma conica in crescita verso l’esterno (convessa) e se non è supportato, c’è un alto rischio di guasto. Questa forma conica si comporterà in modo piuttosto sfavorevole e metterà l’utente a un rischio maggiore quando evita di aggiungere supporti. Quindi, lanciandolo in una forma conica concava, la superficie di downfacing relativamente ad alto rischio mantiene lo stesso intervallo angolare ma la forma generale è una conica a crescita interna che può mantenere la stabilità ed evitare rotture nel processo senza dover aggiungere supporti.
I sistemi VELO3D hanno anche la possibilità di stampare parti fluttuanti, il che significa che non sono fissate alla piastra di costruzione su qualsiasi altra superficie nel volume di costruzione, il che significa che non è stato aggiunto materiale di supporto.
“La costruzione inizia in polvere e qui il principale attivatore, oltre al controllo di processo, è l’esclusivo meccanismo di ricopertura senza contatto (che applica un nuovo strato di polvere sul letto di stampa, rendendolo pronto per un passaggio dai laser per fusione). Poiché non vi sono interferenze tra la parte, che ora fluttua nella polvere, troverai molto gratificante aprire una camera di costruzione e raggiungere semplicemente per estrarre la parte, senza dover rimuovere alcun materiale di supporto ad essa collegato, “Spink ha spiegato.
Ci sono alcune regole per le geometrie fluttuanti. Devono provenire da una sezione trasversale piccola o da un punto della geometria, il che significa che non è possibile stampare un piano piano di grandi dimensioni perché ci saranno ancora sollecitazioni residue anche con i processi unici di VELO3D. E la seconda regola principale è che ci deve essere un inizio polvere e nessun collegamento con la piastra di costruzione.
VELO3D ha ancora un forte team di sviluppo dei processi che lavora alla ricerca e allo sviluppo in corso, in particolare per quanto riguarda la stabilità sui processi esistenti e promuove altri sforzi, ma la maggior parte degli esperti concorda sul fatto che la potente tecnologia di stampa 3D in metallo che hanno sviluppato è piuttosto innovativa.
Come puoi vedere nelle immagini e nei video VELO3D, le geometrie presentano molti dettagli e precisione. Queste capacità significano che il sistema Sapphire può ora stampare oggetti impossibili su altri sistemi di stampa 3D. VELO3D afferma che possono persino ottenere un rapporto di 500: 1 sulle strutture, al contrario del più tipico rapporto di 10: 1 sui sistemi concorrenti (o anche meno 4: 1 o 5: 1 su altre macchine di fusione a letto di polvere), ma dovresti probabilmente provalo tu stesso e vedi di cosa si tratta.