Sviluppo di Laser-Assisted Cold Spray al Centre for Industrial Photonics
Il Centre for Industrial Photonics (CIP) dell’Institute for Manufacturing (IfM) dell’Università di Cambridge ha messo a punto la tecnica chiamata Laser-Assisted Cold Spray (LACS), un processo di deposizione a stato solido che impiega un raggio laser per scaldare in modo localizzato un flusso supersonico di polveri metalliche o cermet. Questo approccio consente di applicare rivestimenti ad alta precisione e riparare componenti in leghe leggere o ad alta resistenza senza raggiungere il punto di fusione del materiale di base. Tra i settori interessati figurano aerospaziale, energia, biomedicale e impianti industriali.
I limiti dello spray a freddo convenzionale
Nelle fasi iniziali, il gruppo guidato dal Professore Bill O’Neill utilizzava sistemi di cold spray tradizionali con azoto come gas vettore per la proiezione delle polveri. Per rivestimenti su titanio e leghe di alluminio impiegate in aerostrutture, si era passati all’uso dell’elio, indispensabile per garantire adesione e densità del deposito. Il suo costo di esercizio — circa 80 sterline al minuto — e i vincoli imposti dagli impianti di riciclo del gas hanno reso insostenibile l’utilizzo per pezzi di grandi dimensioni, come sezioni di rivestimento fusoliera.
Nascita di LACS: fusione tra laser e cold spray
Per superare questi vincoli, gli scienziati del CIP hanno progettato un sistema che combina un laser a fibra con l’ugello di cold spray. Il laser pre‐riscalda la superficie del pezzo e le particelle in volo, abbassando la tensione di snervamento del substrato al passaggio del getto di polveri. Il materiale aderisce a freddo, preservando la microstruttura originale delle particelle e riducendo le sollecitazioni residue. Il processo opera a temperature complessive comprese tra 400 °C e 700 °C, rispetto al picco di 1 200 °C tipico del cold spray convenzionale, e raggiunge velocità di deposizione fino a 10 kg/h.
Vantaggi per materiali speciali e riduzione degli sprechi
LACS estende la gamma di materiali stampabili in cold spray, comprendendo cermet, metalli refrattari e leghe antiossidanti che difficilmente si saldano con il metodo tradizionale. Il minore attrito termico consente di rivestire magneti con nanostruttura o polveri sensibili al calore, oltre a introdurre gradazioni di composizione e rivestimenti funzionali—per esempio, lubrificazione a secco o caratteristiche magnetiche—direttamente in fase di deposizione. L’assenza di fusione limita le perdite di materia e richiede minor energia, contribuendo alla riduzione delle emissioni industriali.
Applicazioni nell’aerospazio: manutenzione in situ e rigenerazione
Nell’industria aeronautica, P&W e Rolls-Royce impiegano saldature tradizionali per il recupero di pale turbine, ma questo approccio può comprometterne la tenacità. La tecnica LACS permette di intervenire direttamente sul componente, aggiungendo materiale senza alterarne la microstruttura originale e senza deformazioni termiche estese. Il team Cambridge ha già dimostrato la riparazione di pannelli al 6000-series Alluminio, ripristinando la planarità e la resistenza meccanica in un unico passaggio, a partire da un modello digitale e riducendo il lead time da settimane a poche ore.
Concorrenza e soluzioni commerciali
Tra le aziende che hanno introdotto soluzioni di cold spray a scopi industriali, SPEE3D (Australia) ha sviluppato il TitanSPEE3D, un sistema containerizzato in grado di produrre parti metalliche di grandi dimensioni con gas compressi e senza laser. L’XSPEE3D, anch’esso fornito da SPEE3D, opera in condizioni estreme—dalle temperature glaciali ad ambienti desertici—per interventi di riparazione sul campo o produzione di componenti nel teatro operativo. A differenza di LACS, questi sistemi non impiegano apporto termico da laser; la loro forza risiede nella semplicità di allestimento e nella velocità di consegna.
Prospettive di evoluzione verso la stampa 3D diretta
Il passo successivo del CIP è trasformare LACS in una vera e propria tecnologia di additive manufacturing per parti complesse, non soltanto rivestimenti. Si valuta l’impiego di robot antropomorfi per muovere il pezzo in tre assi e migliorare la definizione del deposito, ottenendo bordi netti e geometrie fuori asse. I primi test indicano la possibilità di costruire profili “a sbalzo” sovrapponendo passate laser‐assistite, con tolleranze entro poche decine di micrometri.
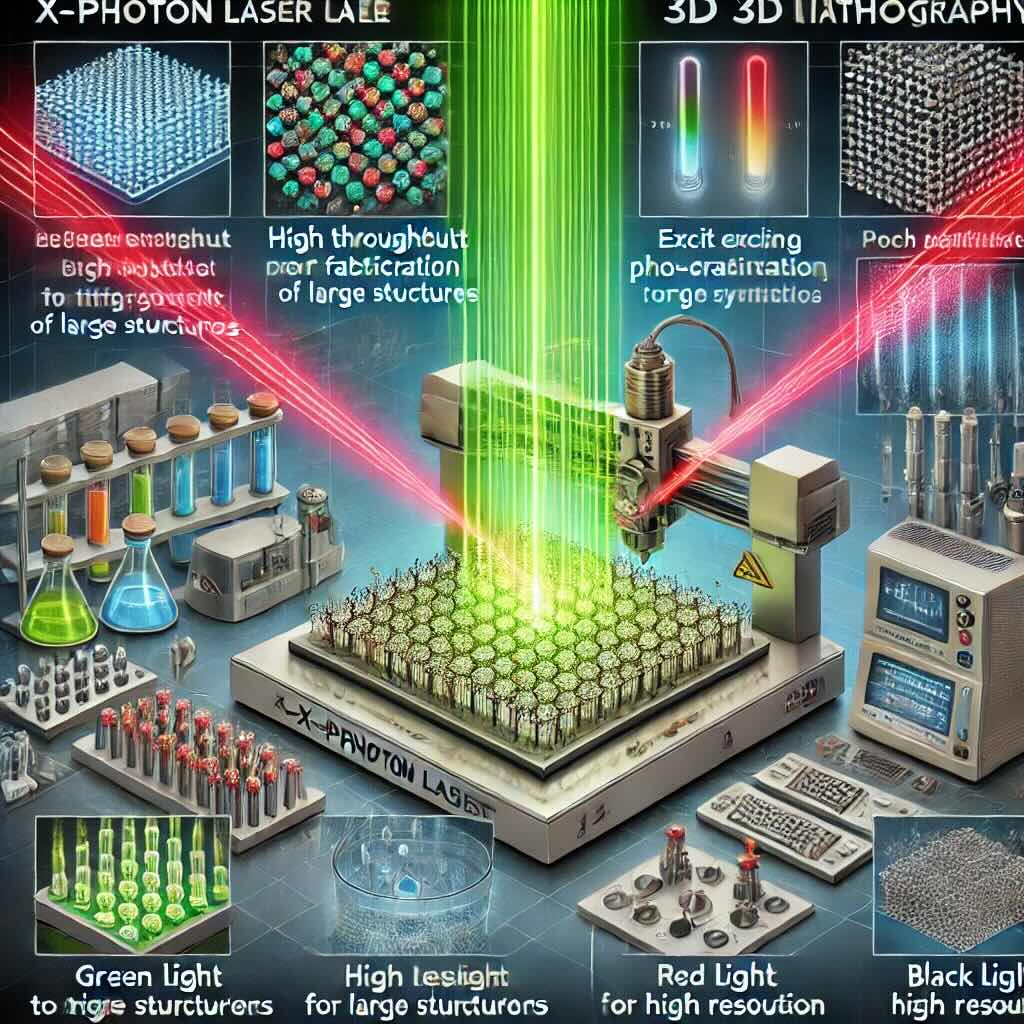