Il sistema MiniFix per la fissazione biologica in microgravità
Il Centro Aerospaziale Tedesco (DLR) ha realizzato MiniFix, un dispositivo per la fissazione di campioni biologici interamente prodotto con stampa 3D, pensato per missioni su razzo suborbitale. L’apparato è stato testato con successo in cinque voli del programma MAPHEUS, confermando la solidità di un approccio che coniuga rapidità di prototipazione, modularità e performance in condizioni di microgravità.
Produzione con Fused Deposition Modeling e iterazioni rapide
Diversamente dai sistemi convenzionali in metallo o in polimeri stampati in stereolitografia, MiniFix è stato realizzato esclusivamente tramite Fused Deposition Modeling (FDM). Componenti fondamentali come i supporti per le siringhe, la piastra di base e l’involucro esterno sono stati prodotti con stampanti desktop Prusa MK3+, impiegando ugelli da 0,4 mm e layer di 0,3 mm. Questo ha permesso di modificare i disegni CAD in tempi contenuti e di arrivare a prototipi funzionali a costi contenuti, ottimizzando ogni elemento in funzione delle esigenze di volo.
Evoluzione dei materiali
MiniFix è stato sottoposto a tre cicli di sperimentazione su filamenti differenti. Per le missioni MAPHEUS-09 e MAPHEUS-12 si è utilizzato PLA (Polylactic Acid), sufficiente per le prove iniziali. MAPHEUS-14 ha visto l’adozione di PETG (Polyethylene Terephthalate Glycol), caratterizzato da resistenza meccanica superiore. In MAPHEUS-15 il sistema è stato stampato in GreenTEC Pro, un bioplastico compostabile in grado di mantenere stabilità termica anche a temperature elevate. Grazie a queste fasi, il dispositivo è diventato il primo involucro sperimentale compostabile ad affrontare un lancio suborbitale.
Architettura modulare e precisione di dosaggio
Il cuore operativo di MiniFix consiste in due siringhe impilate verticalmente, una contenente il fissativo e l’altra il campione biologico. Il movimento è gestito da motori passo-passo NEMA11 accoppiati a guide lineari, che garantiscono erogazioni di volume precise. L’intero meccanismo è inserito in un telaio sterilizzabile in cui le unità di siringhe preassemblate possono essere inserite in condizioni asettiche. Ogni funzione accessoria, ad esempio l’illuminazione interna per colture vegetali, è integrata in modo puntuale senza richiedere revisioni strutturali al sistema portante.
Gestione termica tramite calore di scarto
MiniFix sfrutta il calore generato dai motori per mantenere una temperatura interna costante, eliminando la necessità di elementi riscaldanti aggiuntivi. I dati raccolti durante MAPHEUS-15 mostrano un mantenimento della temperatura a 21,98 °C (± 0,12 °C), con un consumo energetico pari a 4,6 Wh, anche quando l’ambiente esterno scende a 4 °C. Questo approccio riduce il peso complessivo del payload e semplifica il cablaggio termico.
Resistenza ai rigori del volo suborbitale
Nel corso delle campagne MAPHEUS, MiniFix ha superato sollecitazioni di vibrazione oltre 20 g e variazioni termiche che vanno dall’ipergravità al vuoto spaziale e al rientro atmosferico. I controlli post-volo non hanno evidenziato deformazioni o cedimenti dei componenti stampati, confermando l’affidabilità del progetto e dei materiali FDM impiegati.
Prospettive di impiego e sviluppo
A valle delle fasi di fissazione, MiniFix potrà evolversi in un sistema versatile per la gestione di liquidi in missioni spaziali. La piattaforma è già predisposta per operazioni di miscelazione programmata e potrebbe ospitare reagenti per test farmacologici o moduli microfluidici per la produzione in orbita di biomateriali. Il design open-source del microcontrollore e la struttura modulare rendono il progetto estendibile a numerosi scenari di ricerca in scienze della vita e ingegneria spaziale.
Additive manufacturing nello spazio
Il lavoro del DLR si inserisce in un contesto più ampio in cui la stampa 3D sta diventando ponte tra sviluppo in laboratorio e realizzazione on-orbit di componenti. L’Agenzia Spaziale Europea (ESA) ha impiegato la stampante Metal3D a bordo della Stazione Spaziale Internazionale (ISS) per produrre in microgravità il primo pezzo metallico, ora analizzato a Terra. Parallelamente, Nikon e JAXA stanno collaudando processi di stampa di grandi dimensioni per strutture in metallo destinate ad applicazioni spaziali, con l’obiettivo di ridurre i tempi di consegna e i costi di lancio. In questo panorama, MiniFix rappresenta un esempio di come un payload completamente basato su piattaforme desktop FDM e bioplastiche possa affrontare senza compromessi i requisiti di missioni suborbitali.
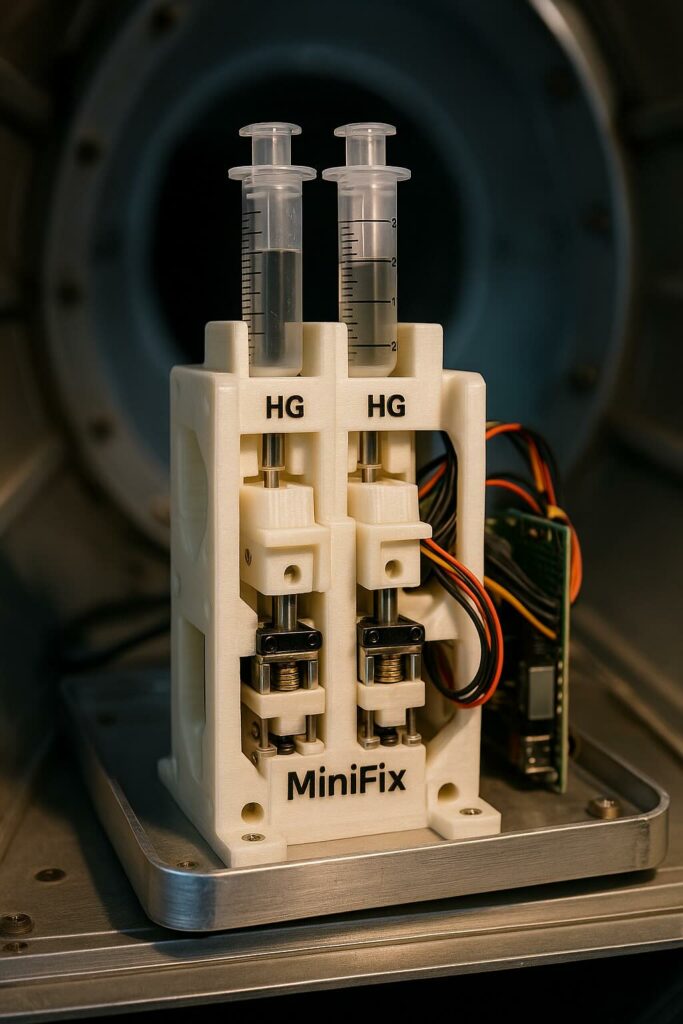