Monitoraggio in tempo reale della stampa L-PBF: come il sistema Fringe Inspection ha migliorato qualità ed efficienza
Un fornitore statunitense attivo nel settore aerospaziale ha affrontato una serie di problemi ricorrenti legati alla qualità dei pezzi prodotti mediante Laser Powder Bed Fusion (L-PBF), una tecnica di stampa 3D che utilizza un letto di polvere metallica fusa strato per strato tramite laser. I difetti riscontrati durante la produzione, effettuata con una macchina EOS M270, comprendevano porosità irregolari e geometrie interne compromesse. Queste anomalie costringevano l’azienda a scartare intere serie di componenti stampati, con un impatto diretto sui costi e sulla continuità operativa.
Le analisi eseguite secondo i protocolli standard, comprese le immagini dei singoli strati raccolte durante la stampa, non fornivano informazioni sufficienti per identificare la causa dei problemi. La complessità dei difetti, unita alla loro variabilità, rendeva difficile individuare un pattern chiaro. Soluzioni convenzionali di controllo non erano in grado di rilevare deviazioni microscopiche ma significative, che influenzavano in modo diretto la riuscita del processo.
Un nuovo approccio con la metrologia ottica: il ruolo del sistema Fringe Inspection
La svolta è avvenuta con l’adozione del sistema di ispezione ottica Fringe Inspection, sviluppato da Phase3D. A differenza delle tecniche tradizionali, questa tecnologia si basa su una misurazione precisa della topografia superficiale tramite luce strutturata, acquisendo in tempo reale la distribuzione dell’altezza di ogni singolo strato durante la stampa. I dati raccolti consentono di evidenziare immediatamente qualsiasi variazione anomala nella deposizione della polvere.
Grazie a questo approccio, è stato possibile individuare il vero motivo dei difetti: l’accumulo di polvere metallica sulla struttura del rastrello, l’elemento meccanico che distribuisce il materiale sul piano di stampa. In alcune situazioni, specialmente quando le geometrie stampate sporgevano leggermente, il rastrello entrava in contatto con queste superfici, provocando vibrazioni che facevano cadere sul pezzo polvere in eccesso. Questa ricaduta generava difetti nella stratificazione, con variazioni di altezza fino a 200 micrometri – un valore quattro volte superiore allo spessore previsto per ciascun layer.
Reazione correttiva e impostazione di soglie di sicurezza nel processo produttivo
L’informazione ottenuta tramite il sistema di ispezione ha permesso di definire una soglia di controllo interna al processo. È stato così stabilito un limite massimo di accettabilità per la polvere depositata: se uno strato risultava avere un’altezza superiore a 200 micrometri, il sistema interrompeva automaticamente la produzione per evitare sprechi di materiale e tempo.
Parallelamente, è stata introdotta una modifica meccanica al sistema: l’aggiunta di una lama fissa posizionata nel punto di riposo del rastrello. Questo elemento ha il compito di trattenere o rimuovere eventuali residui di polvere accumulati, impedendone la ricaduta non controllata nelle fasi successive del processo.
Impatto economico e cambiamento nel modello di controllo qualità
I benefici derivanti dall’implementazione di Fringe Inspection sono stati immediati e significativi. Nella produzione di una serie da 50 pezzi, la percentuale di componenti scartati prima dell’intervento era pari al 5%, con una perdita economica stimata intorno ai 63.000 dollari l’anno. L’introduzione del sistema di monitoraggio ottico ha ridotto questa percentuale di oltre il 90%, portando a un drastico contenimento delle perdite.
Ma il cambiamento più rilevante riguarda il passaggio da un approccio di analisi reattiva a un controllo proattivo del processo. Invece di analizzare i pezzi a posteriori per identificare eventuali difetti, l’azienda è ora in grado di monitorare costantemente ogni fase della produzione, intervenendo in tempo reale al primo segnale di anomalia. Questo approccio ha aumentato la stabilità del processo, migliorato la qualità complessiva dei componenti stampati e rafforzato la prevedibilità operativa.
Una nuova prospettiva sulla produzione additiva con polveri metalliche
L’esperienza di questo fornitore evidenzia l’importanza di dotarsi di sistemi di ispezione avanzati all’interno dei flussi produttivi basati su tecnologie additive come la L-PBF. Le deviazioni microscopiche che possono sembrare trascurabili durante la deposizione di polvere, in realtà, incidono in modo rilevante sulla qualità finale del pezzo. Rilevarle nel momento in cui si verificano e disporre degli strumenti per intervenire immediatamente si rivela una strategia vincente, sia in termini di affidabilità tecnica sia di efficienza economica.
Fringe Inspection si conferma come uno strumento in grado di aumentare la trasparenza e la tracciabilità del processo, integrandosi in un percorso più ampio di evoluzione verso una manifattura additiva industriale più matura, consapevole e orientata al miglioramento continuo.
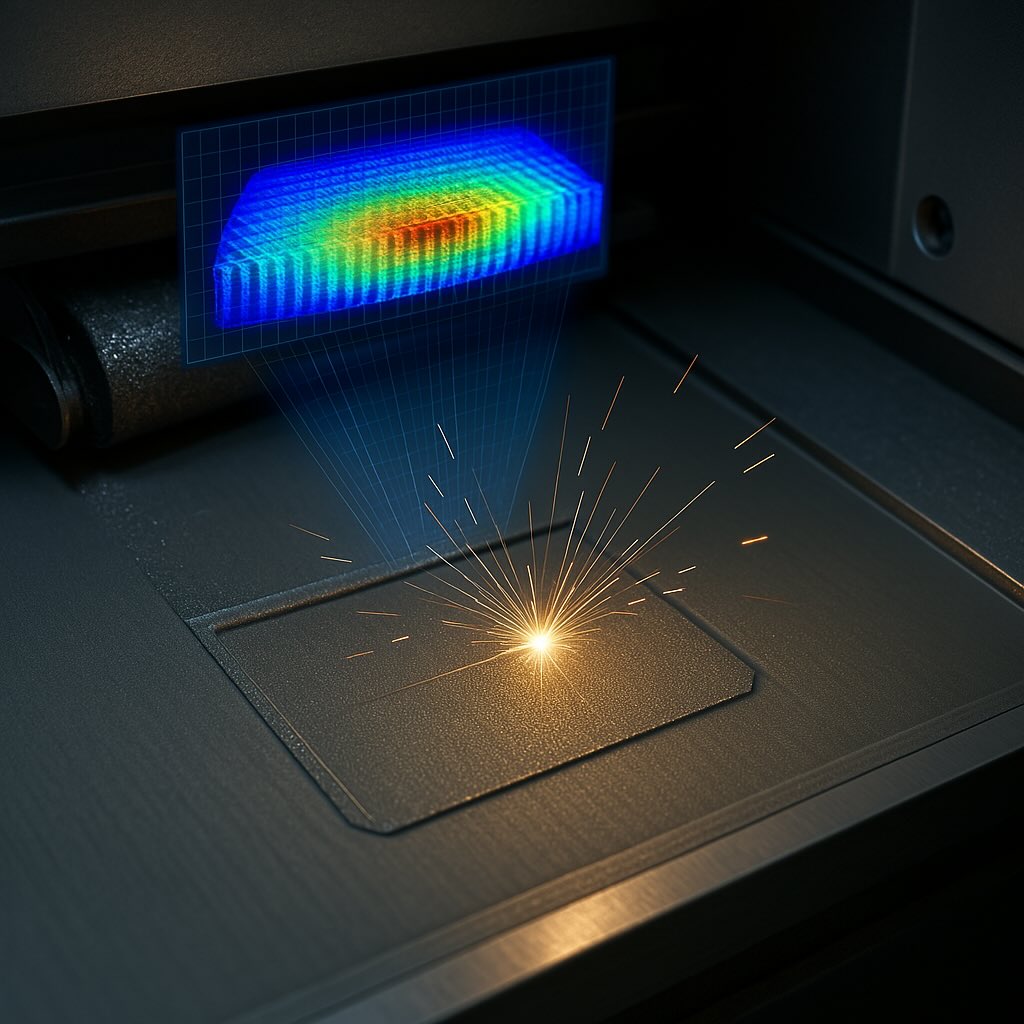
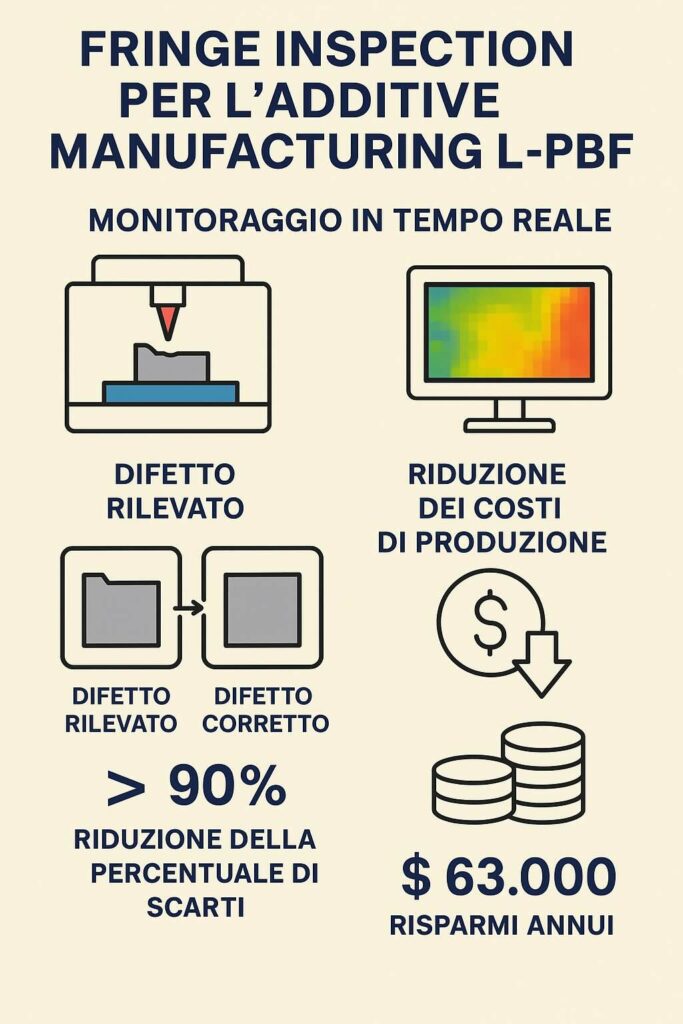