First Light Fusion, azienda britannica attiva nello sviluppo di sistemi di fusione inerziale, ha integrato componenti in tantalio prodotti tramite stampa 3D grazie alla collaborazione con Croom Medical. Il progetto fa leva sulla piattaforma TALOS di Croom Medical, concepita per la lavorazione additiva di tantalio in ambito medicale e industriale.
La piattaforma TALOS per il tantalio
Croom Medical ha realizzato TALOS in collaborazione con Global Advanced Metals, tra i principali fornitori al mondo di tantalio di grado elettronico. Il cuore del sistema è una macchina Colibrium Additive M2 basata su tecnologia laser powder bed fusion, che consente di fondere polveri di tantalio strato dopo strato. L’architettura modulare di TALOS supporta volumi di stampa fino a 200 × 200 × 200 mm, con controlli termici avanzati e filtri HEPA per garantire purezza e precisione di deposizione.
Proprietà del tantalio e sfide di stampa
Il tantalio è scelto per la sua elevata resistenza alla corrosione, punto di fusione superiore a 3 000 °C e comportamento stabile sotto shock intenso. Tuttavia la sua elevata conducibilità termica e la tendenza all’ossidazione rendono complessa la produzione additiva. TALOS affronta questi ostacoli attraverso:
-
gestione inerte del fascio laser e della camera di costruzione;
-
polveri sferiche ad alta densità di flusso;
-
strategie di ritrattamento termico integrate per ridurre le tensioni interne.
Il Pressure Amplifier: principio di funzionamento
Il dispositivo denominato Pressure Amplifier trasforma una pressione d’ingresso generata da un “driver” – che può essere un cannone elettromagnetico, un generatore di plasma o un sistema laser – in un impulso di pressione fino a diversi milioni di atmosfere. Il meccanismo interno sfrutta geometrie coniche e camere di confinamento in tantalio per comprimere un materiale di carica (tipicamente un gas leggero), innalzandone densità e temperatura fino al punto di innesco della reazione di fusione.
Confronto con le tecniche convenzionali
Fino a poco tempo fa, i componenti del Pressure Amplifier venivano ricavati da blocchi di tantalio lavorati con macchine tradizionali come trapani e frese CNC, un approccio dispendioso in termini di tempo e materiale. La stampa 3D offre:
-
produzione diretta di geometrie complesse senza necessità di attrezzaggi multipli;
-
riduzione degli scarti di materiale fino al 60 %;
-
tempi di prototipazione accorciati da settimane a pochi giorni.
Risultati dei test sperimentali
In uno studio pubblicato sul Journal of Applied Physics, modelli additivi del Pressure Amplifier hanno resistito a shock meccanici fino a cinque milioni di atmosfere, mostrando prestazioni equivalenti a quelle ottenute con componenti lavorati tradizionalmente. I test, condotti nello stabilimento di First Light Fusion a Yarnton (Oxford), hanno incluso prove con cannone a gas leggero in due stadi, dimostrando la ripetibilità dei picchi di pressione e la stabilità strutturale del tantalio stampato.
Prospettive di impiego e sviluppi futuri
L’adozione di componenti in tantalio prodotti additivamente apre scenari in vari settori:
-
Ricerca sui materiali, per sperimentare nuovi target di fusione con costi contenuti;
-
Difesa, dove sono richiesti dispositivi capaci di generare onde d’urto controllate;
-
Energia, incentrata su reattori di piccola scala per applicazioni remote.
Entro il prossimo anno First Light Fusion prevede di affinare i processi di post-lavorazione termica e di collaborare con altri fornitori di leghe avanzate per ampliare il range di materiali utilizzabili sulla piattaforma TALOS.
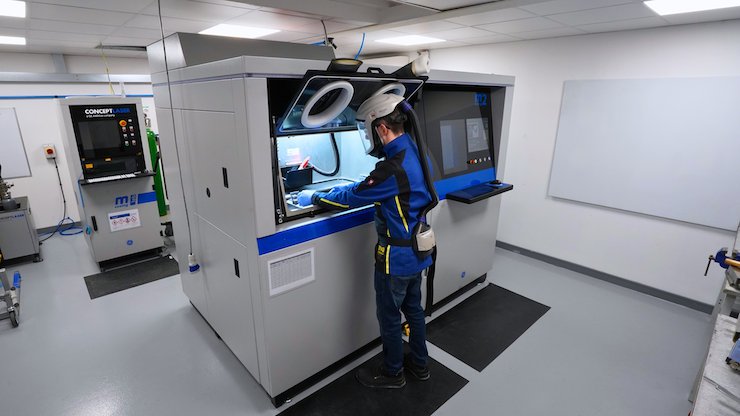