Sviluppo di un sistema di trasmissione magnetica modulabile: una nuova frontiera per l’industria
Un gruppo di ricercatori dell’Università di Kaiserslautern, in collaborazione con l’azienda EGH, ha progettato un nuovo tipo di sistema di trasmissione basato su principi magnetici, pensato per applicazioni industriali ad alta efficienza. Il lavoro si è svolto all’interno del progetto MagGear, sostenuto economicamente dal Ministero federale tedesco per gli Affari Economici e la Protezione del Clima (BMWK), con l’obiettivo di esplorare nuove possibilità nella trasmissione meccanica di potenza.
Il fulcro di questo studio è la creazione di un ingranaggio planetario a giunto magnetico permanente, una configurazione che rappresenta un’alternativa concreta ai tradizionali sistemi meccanici, spesso soggetti a usura, manutenzione costante e perdite di efficienza dovute all’attrito.
Trasmissione di potenza senza contatto meccanico
Una delle innovazioni più rilevanti di questo sistema riguarda la modalità di trasferimento della potenza. A differenza delle trasmissioni convenzionali, che si basano sul contatto diretto tra dentature metalliche, questo meccanismo impiega magneti permanenti per creare un collegamento funzionale tra l’albero motore e l’albero condotto.
Questa scelta progettuale elimina il contatto fisico diretto tra i componenti in rotazione, riducendo in modo significativo le sollecitazioni meccaniche e l’attrito. Di conseguenza, viene quasi annullata la necessità di lubrificanti, con vantaggi sia in termini di manutenzione sia sul piano ambientale, riducendo la gestione e lo smaltimento di oli e grassi industriali.
Controllo elettronico del rapporto di trasmissione
A rendere il sistema ancora più flessibile è la presenza di un modulo di regolazione elettronica del rapporto di trasmissione, che consente di adattare in tempo reale le prestazioni del meccanismo alle condizioni operative. A seconda delle esigenze, è possibile variare il rapporto tra la velocità dell’albero di ingresso e quello di uscita, migliorando l’efficienza energetica e la risposta dinamica della macchina.
Questa capacità di adattamento risulta particolarmente utile in ambienti produttivi dove i carichi e le velocità variano frequentemente, come nelle linee automatizzate, nei robot industriali o nei sistemi di trasporto avanzati.
Il contributo della stampa 3D nella progettazione del modulatore
Uno degli elementi tecnici più sofisticati del progetto è il cosiddetto modulatore, una parte fondamentale del sistema di trasmissione, prodotta interamente tramite tecnologie di stampa 3D. Grazie alla produzione additiva è stato possibile sviluppare geometrie interne complesse, che difficilmente sarebbero ottenibili con metodi convenzionali come la fresatura o la fusione.
L’uso di materiali compositi leggeri, ottimizzati per le caratteristiche elettromagnetiche del sistema, ha permesso di ridurre in modo sostanziale il peso del componente e di migliorare la densità di potenza del dispositivo, ovvero la quantità di energia trasmessa per unità di massa.
Inoltre, il disegno ottimizzato del modulatore ha consentito di aumentare la stabilità termica del sistema, un fattore essenziale nelle applicazioni industriali in cui le temperature possono variare sensibilmente o raggiungere livelli elevati durante il funzionamento prolungato.
Vantaggi pratici in contesti industriali
Il sistema sviluppato si propone come una soluzione interessante per diversi settori industriali, in particolare quelli che richiedono sistemi di trasmissione ad alta efficienza, affidabili nel tempo e capaci di adattarsi rapidamente alle variazioni operative.
La possibilità di funzionare senza lubrificazione costante e la presenza di una regolazione attiva del rapporto di trasmissione rendono questa tecnologia adatta a contesti quali l’automazione avanzata, la robotica collaborativa, il settore ferroviario e quello aerospaziale. In tutte queste applicazioni, la combinazione tra robustezza, efficienza e flessibilità rappresenta un valore aggiunto concreto.
Anche nel campo delle macchine utensili e delle apparecchiature da officina, dove spesso i sistemi sono soggetti a stress prolungati e richiedono manutenzioni frequenti, una trasmissione a giunto magnetico può garantire maggiore continuità operativa, riducendo i costi totali di esercizio.
Protezione contro i sovraccarichi: un meccanismo intrinseco
Un ulteriore vantaggio di questo sistema è legato alla capacità intrinseca di assorbire sovraccarichi senza subire danni strutturali. In caso di carichi superiori alla soglia prevista, l’accoppiamento magnetico può “slittare” temporaneamente, evitando che l’energia in eccesso si traduca in rotture o deformazioni dei componenti interni.
Questa caratteristica introduce una forma di protezione passiva del sistema, particolarmente utile in applicazioni dove sono possibili picchi improvvisi di carico, e contribuisce ad aumentare la durata dei componenti meccanici collegati.
Presentazione pubblica e prospettive future
Il sistema MagGear è stato mostrato al pubblico durante la Fiera di Hannover, in uno spazio espositivo condiviso con altre realtà industriali della Renania-Palatinato. L’interesse manifestato dai visitatori e dagli operatori del settore suggerisce che questo approccio potrebbe trovare sbocchi applicativi concreti già nel medio termine.
L’obiettivo dei promotori è ora quello di trasferire il prototipo in una fase di pre-produzione, analizzando la scalabilità dei processi e la possibilità di integrazione nei sistemi industriali esistenti. La collaborazione tra ricerca universitaria e impresa rappresenta, in questo contesto, un modello efficace per portare l’innovazione tecnologica dal laboratorio al mercato.
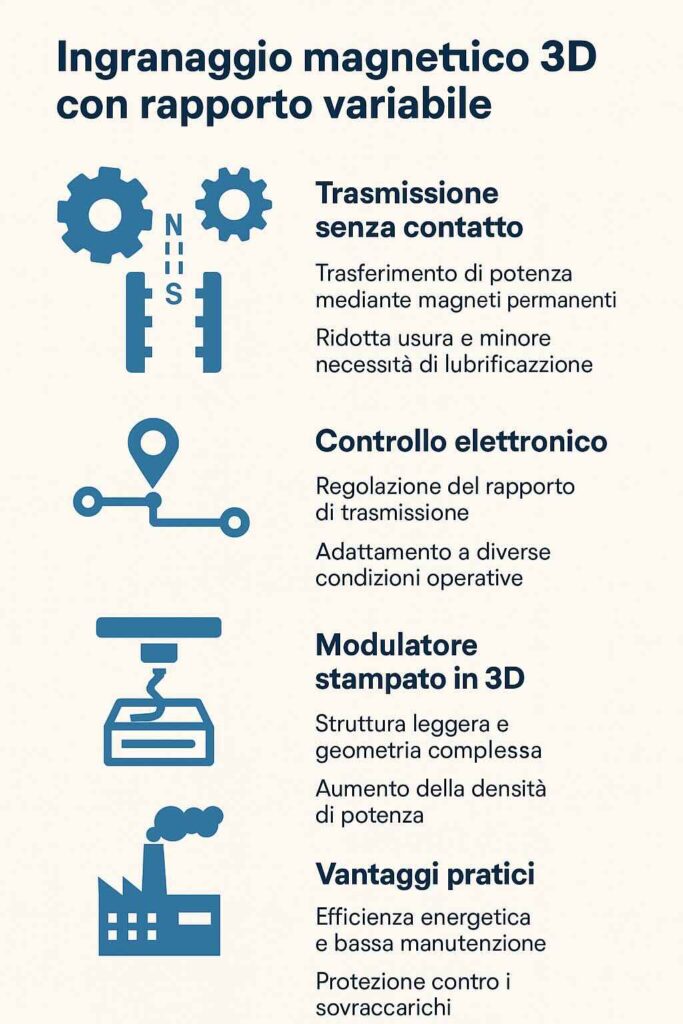