Psyonic rende accessibili le protesi avanzate utilizzando la produzione additiva
Psyonic mira ad avere un impatto nel mondo delle protesi utilizzando la tecnologia di stampa 3D di Formlabs.
Nel 2017, quasi 60 milioni di persone in tutto il mondo vivevano con l’amputazione degli arti a causa di cause traumatiche. Per i pazienti che si stanno riprendendo da un’emergenza medica, l’ingresso nel nuovo mondo delle protesi può essere doloroso. La maggior parte vuole un ritorno alla normalità e fare cose come guidare un’auto, andare in palestra o anche solo riordinare la casa.
La maggior parte delle protesi tradizionali sono costose e fragili, con circa il 10% dei pazienti che necessitano di una protesi avanzata in grado di permettersene una, secondo Psyonic , il creatore di Ability Hand.
Ability Hand è progettato e prodotto internamente presso Psyonic con metodi di produzione ibridi, tra cui stampa 3D, stampaggio a iniezione e silicone e macchine CNC. Psyonic dice che Ability Hand promette di riportare la vita e la mobilità a quelle che erano per i pazienti.
Utilizzando le stampanti 3D SLA di Formlabs , Psyonic afferma di essere stata in grado di creare da zero una protesi dell’arto superiore registrata dalla FDA, coperta da medicare e che definisce il settore. La macchina consente anche la raccolta del feedback dei clienti, seguita da una rapida prototipazione interna per migliorare il design e la funzionalità.
Psyonic ha anche affermato che l’implementazione di un vero metodo di produzione ibrida ha contribuito a fornire l’Ability Hand a un prezzo accessibile. Secondo Psyonic, l’azienda è stata in grado di aumentare l’accessibilità e l’accessibilità dal 10% al 75% dei pazienti.
L’azienda ha inoltre utilizzato nuovi materiali di stampa 3D durevoli e resistenti agli urti per creare parti di uso finale di lunga durata.
Uno dei primi utilizzatori della mano abilità è stato il sergente Garrett Anderson, che è stato schierato in Iraq nel 2005. Il suo veicolo è stato colpito da una bomba sul ciglio della strada. Di conseguenza, Anderson ha avuto lievi lesioni cerebrali traumatiche e una mascella rotta, oltre a dover amputare il braccio destro sotto il gomito.
Anderson ha tentato di tornare alla vita normale al suo arrivo a casa, ottenendo una laurea e un master presso l’Illinois State University. Anderson ha incontrato il CEO di Psyonic Aadeel Akhtar quando aveva un dottorato di ricerca. studente, ei due erano entrambi insoddisfatti dello stato attuale delle protesi in quel momento.
“Miscelare e abbinare i metodi di produzione è estremamente importante, credo, per le startup in generale, ma soprattutto per Psyonic. Non avremmo potuto competere con altre aziende di protesi delle nostre dimensioni se avessimo dovuto attenerci alla produzione puramente tradizionale”, ha affermato James Austin, ingegnere meccanico capo. “Cose come la lavorazione CNC e lo stampaggio a iniezione, i costi iniziali, in particolare per il tentativo di prototipare cose con più iterazioni, sarebbero stati troppo astronomici da fare per noi”.
Gli stampi stampati in 3D per la produzione di parti in fibra di carbonio possono ridurre i costi e ridurre i tempi di consegna. Gli ingegneri possono stampare direttamente lo stampo a costi contenuti e in poche ore senza doverlo intagliare a mano o occuparsi di apparecchiature CNC. La resina per alte temperature e la resina Rigid 10K consentono alle aziende di dispositivi medici come Psyonic di ottenere forme di stampi complicate con dettagli fini che sarebbero difficili da produrre con i metodi tradizionali.
Austin ha spiegato: “Nelle prime iterazioni dello stampo in fibra di carbonio, la stampa 3D SLA era in realtà piuttosto importante. Non avevamo le risorse per produrre stampi per la fibra di carbonio, ad esempio mediante lavorazione a macchina. Quindi, quello che abbiamo fatto invece è stato produrre stampi usando la resina ad alta temperatura. Questo era fragile, ma resistente al calore, il che ci ha permesso di premere i fogli di fibra di carbonio nella forma esatta che volevamo, metterli in un forno ad alta temperatura per farli stagionare e quindi farli aderire alla nostra mano”.
Il team ha inizialmente utilizzato la stampa 3D per ogni parte della Ability Hand, comprese le dita, nel tentativo di ridurre i costi. Dopo il feedback dei clienti sullo schiocco e la rottura delle dita, è stato effettuato il passaggio agli stampi di stampa 3D per le dita.
Per creare stampi sono state utilizzate anche stampanti 3D di modellazione a deposizione fusa (FDM).
Austin ha detto: “Abbiamo ottenuto moltissimi usi da questi stampi. Puoi usarli più e più volte, probabilmente dozzine e dozzine di volte. L’unica limitazione con la resina trasparente è che si consumano nel tempo, principalmente solo per la manipolazione. Ma anche quando ciò accade, è abbastanza facile applicare un’altra tiratura sulla stampante, e nel giro di 24 ore, grazie all’alta risoluzione con cui li stampiamo, abbiamo un altro stampo e siamo pronti per modellare altre dita .”
È stata utilizzata la risoluzione più alta possibile durante la stampa con la Form 3 sia per le parti finali che per gli stampi. In questo modo le parti si incastrano con precisione e si adattano perfettamente all’interno della mano e attorno ai motori e agli ingranaggi. Psyonic ha affermato che qualsiasi variazione o tolleranza in questo potrebbe causare la macinazione degli ingranaggi o il mancato adattamento delle parti.
La crescita di Psyonic come azienda ha spinto il CEO Aadeel Akhtar Ph.D e il suo team a richiedere moderne tecniche di produzione ibrida e soluzioni ingegneristiche innovative. Il passo successivo per l’azienda è ridimensionare e portare il prodotto agli utenti di tutto il mondo.
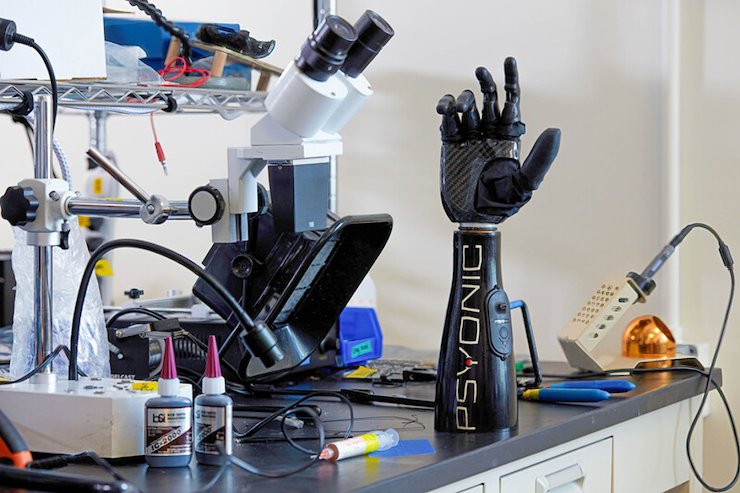