L’azienda californiana di lancio spaziale Rocket Lab sta utilizzando una stampante 3D da 90 tonnellate per costruire quelle che vengono definite le ‘strutture in composito di carbonio più grandi della storia’. La stampante 3D, una macchina per la deposizione automatica delle fibre (AFP) su misura, è considerata il sistema più grande del suo genere al mondo. Costruita negli Stati Uniti da Electroimpact, il robot è alto 12 metri e può posare fino a 100 metri di fibra di carbonio continua al minuto.
Rocket Lab ha implementato la macchina AFP su larga scala nel suo Space Structures Complex a Middle River, nel Maryland. Il sistema è progettato per automatizzare la produzione delle principali strutture composite del veicolo di lancio riutilizzabile Neutron, comprese le sezioni interstadio da 28 metri, i pannelli di carenatura, i serbatoi del primo stadio da 7 metri di diametro e quelli del secondo stadio da 5 metri di diametro.
Secondo Rocket Lab, mentre la costruzione manuale convenzionale di una cupola del secondo stadio richiede diverse settimane, la macchina AFP è in grado di produrne una in sole 24 ore. L’azienda prevede di risparmiare oltre 150.000 ore nella costruzione delle strutture del razzo grazie alla tecnologia AFP.
Tecnologia avanzata per una produzione più efficiente
“Stiamo costruendo il più grande razzo in composito di carbonio al mondo, quindi è naturale che ci serva una macchina di deposizione di fibra di carbonio unica al mondo,” ha commentato Sir Peter Beck, fondatore e CEO di Rocket Lab. “Stiamo combinando la nostra tecnologia proprietaria di composito di carbonio collaudata in volo, la manifattura additiva e la robotica autonoma per progettare e costruire componenti aerospaziali su larga scala a un ritmo che non solo supporta il lancio del Neutron, ma anche le strutture in composito di carbonio per i nostri clienti nel settore spaziale.”
La macchina AFP da 90 tonnellate può muoversi lateralmente fino a 30 metri, depositando strati di fibra di carbonio in direzioni diverse fino alla completa fabbricazione della struttura. La velocità del sistema è essenziale per la produzione di componenti del lanciatore Neutron, che misurano migliaia di metri quadrati e comprendono centinaia di strati di fibra di carbonio.
Il sistema è dotato anche di un sistema di ispezione automatizzato in tempo reale, che monitora il processo produttivo e rileva eventuali difetti durante la deposizione del composito. In caso di difetti, il sistema avvisa automaticamente l’operatore prima che venga aggiunto il successivo strato, garantendo la qualità del lanciatore Neutron e soddisfacendo gli elevati standard richiesti dall’industria aerospaziale.
Applicazioni su larga scala e non solo
Nonostante le sue dimensioni imponenti, la macchina AFP non è limitata a sole applicazioni di grande scala. Viene infatti utilizzata anche per stampare in 3D strutture più piccole per il razzo Neutron, progettato per trasportare fino a 13.000 kg in orbita bassa terrestre e per il lancio di costellazioni di satelliti. Neutron, il primo razzo a medio carico in composito di carbonio, è previsto per il suo lancio inaugurale il prossimo anno e sarà alimentato dal nuovo motore riutilizzabile Archimedes, prodotto in 3D, che sostituisce il precedente motore Rutherford, realizzato con la tecnologia Electron Beam Melting (EBM).
Rocket Lab utilizza il sistema AFP anche per produrre le parti del primo stadio del razzo Electron, alimentato da motori stampati in 3D, e altre strutture in composito di carbonio per applicazioni spaziali. Queste includono pannelli e assemblaggi per veicoli spaziali, substrati per pannelli solari, strutture primarie in composito di carbonio e serbatoi, oltre ad altri progetti per clienti nel settore aerospaziale.
Manifattura additiva e produzione di razzi spaziali
La manifattura additiva sta assistendo a un crescente utilizzo nella produzione di razzi spaziali. All’inizio di quest’anno, Paul Gradl della NASA ha dichiarato che la stampa 3D in metallo gioca un “ruolo enorme nello sviluppo e nella produzione di motori a razzo”. Recentemente è stato annunciato che SpaceX ha stipulato un accordo di licenza da 5 milioni di dollari per stampanti 3D di Velo3D, utilizzate per la produzione dei motori Raptor.
Anche LandSpace, rivale cinese di SpaceX, ha completato con successo il lancio e l’atterraggio del suo razzo riutilizzabile Zhuque-3 VTVL-1, che include numerosi componenti realizzati con tecnologie di stampa 3D di Bright Laser Technologies (BLT). Questi componenti stampati in 3D hanno permesso una significativa riduzione del tempo di produzione e supportato iterazioni rapide nello sviluppo. Inoltre, BLT ha fornito stampanti 3D per fabbricare parti del razzo Gravity-1 della società cinese Orienspace, superando le difficoltà tipiche della produzione convenzionale, come i lunghi cicli produttivi e il basso utilizzo dei materiali.
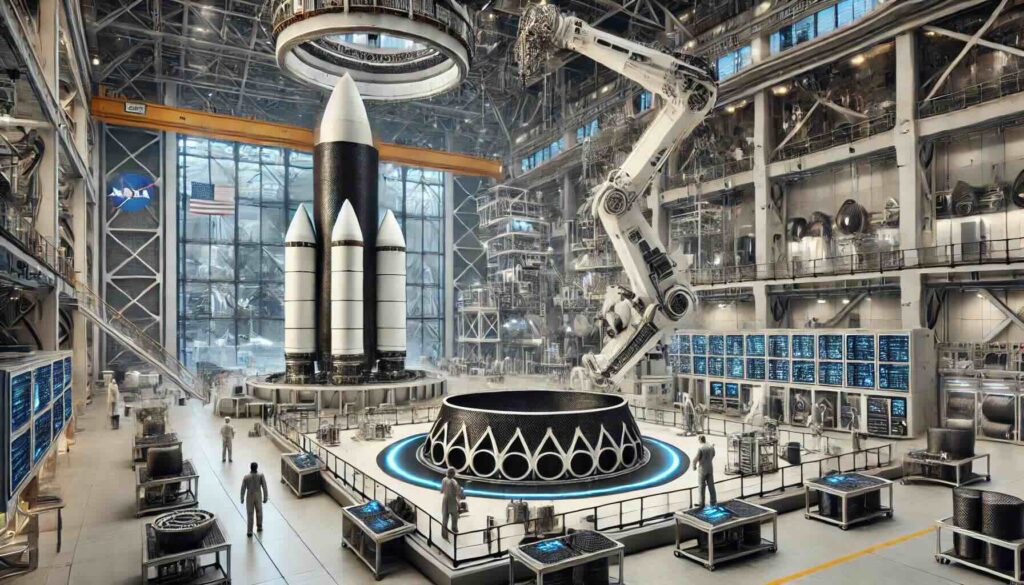