La cattedra di produzione additiva digitale (DAP) presso RWTH Aachen sta portando avanti miglioramenti innovativi nella pressofusione a camera fredda con il progetto HoTKaSt. Lo scopo del progetto è ridurre significativamente l’uso delle risorse e le emissioni di CO2 nel processo di pressofusione grazie a un nuovo design della camera di riempimento e a superfici resistenti all’usura. Il progetto è finanziato dal Ministero federale dell’Istruzione e della Ricerca (BMBF) con oltre 750.000 euro per un periodo di due anni.
Innovazioni nel design della camera di riempimento
La pressofusione a camera fredda è ampiamente utilizzata in settori come quello automobilistico, in particolare per la produzione di componenti leggeri in alluminio. Tuttavia, la durata della camera di riempimento e del pistone nel processo di pressofusione orizzontale è compromessa da distorsioni e usure legate al processo. Ciò porta a tempi di fermo della produzione, a un elevato utilizzo di risorse e a un aumento del tasso di scarto, rappresentando una sfida significativa dato l’inasprimento delle normative ambientali e le pressioni sui costi.
Nell’ambito del progetto HoTKaSt, il team sta sviluppando un nuovo design della camera di riempimento per garantire una distribuzione omogenea della temperatura e ridurre al minimo la distorsione. L’uso della saldatura a deposizione laser (DED-LB/M) consente di creare superfici interne resistenti all’usura che prolungano la durata dei componenti.
Riduzione dello stress meccanico e miglioramento del rivestimento
Un elemento centrale del progetto è la creazione di una distribuzione uniforme della temperatura all’interno della camera di riempimento, al fine di ridurre lo stress meccanico e l’affaticamento del materiale. Inoltre, la nuova tecnologia di rivestimento permette una migliore resistenza alle alte pressioni e temperature del processo di pressofusione. Queste misure mirano a ridurre al minimo l’uso di lubrificanti, contribuendo ulteriormente a ridurre l’impatto ambientale.
Risultati attesi e sostenibilità
I risparmi attesi dal progetto HoTKaSt sono considerevoli: riducendo i rifiuti dell’8%, si potrebbero risparmiare circa 50.000 tonnellate di alluminio e oltre 480.000 tonnellate di CO2 all’anno. Il progetto rappresenta un passo importante verso processi di produzione più sostenibili ed efficienti nella stampa 3D dei metalli. I risultati ottenuti apporteranno benefici non solo al processo di pressofusione, ma anche ad altre aree della produzione additiva.
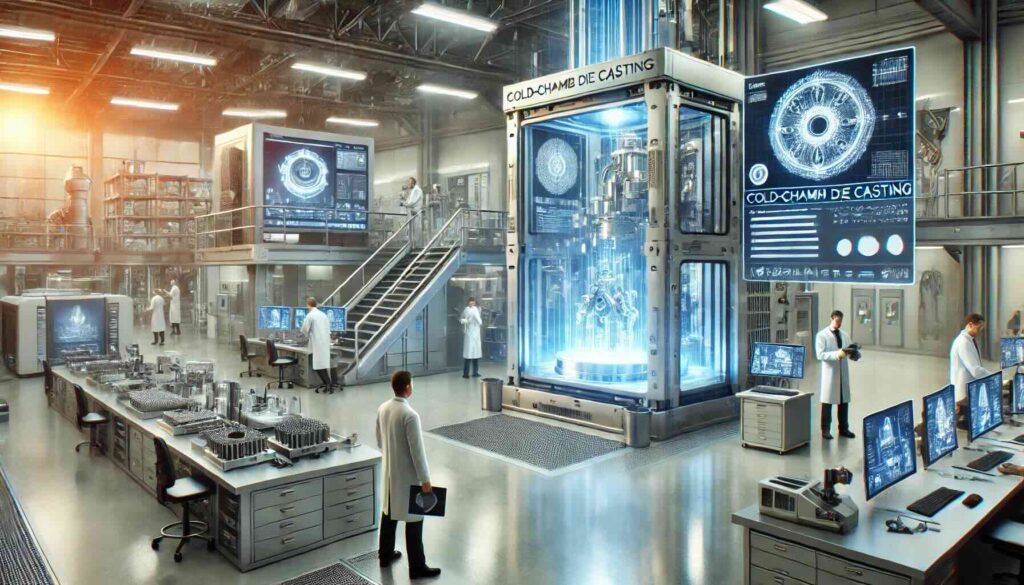