La crescente domanda di componenti in scala micro e nanometrica sta mettendo sotto pressione le tecnologie di produzione tradizionali. L’evoluzione in ambiti come la microelettronica, i sensori miniaturizzati e la strumentazione biomedica richiede soluzioni produttive più avanzate, in grado di realizzare strutture complesse, compatte e altamente precise. In questo contesto, la produzione additiva – in particolare la stampa 3D ad alta risoluzione – si sta affermando come un’opzione tecnicamente interessante per superare i limiti dei metodi convenzionali.
Limiti delle tecnologie tradizionali e necessità di innovazione
I processi produttivi classici, spesso basati su tecniche di sottrazione di materiale o su fasi di assemblaggio sequenziali, non riescono a garantire sempre la precisione richiesta né a gestire geometrie intricate su scala micrometrica. Inoltre, l’integrazione di più funzioni in un singolo componente, come ad esempio canali fluidici, elementi sensibili e connessioni elettriche, comporta difficoltà di progettazione e realizzazione.
Proprio in risposta a queste sfide, si stanno sviluppando soluzioni basate sulla stampa 3D micro e nano-strutturale, che consentono di ottenere componenti integrati, funzionali e tridimensionali con un solo passaggio produttivo.
Sette tecnologie additive in fase di valutazione
Lo studio analizzato prende in esame sette tecniche di stampa 3D adatte alla realizzazione di componenti su scala micro e nano. Tra queste vi sono il binder jetting, indicato per la produzione di volumi consistenti grazie alla sua efficienza nella deposizione selettiva di leganti su polveri, e la fotopolimerizzazione da vapore, che permette di ottenere una risoluzione estremamente fine, anche al di sotto del micrometro.
Quest’ultima, in particolare, si presta alla fabbricazione di microstrutture funzionali tipiche di applicazioni in dispositivi microfluidici e nei sistemi MEMS (Micro-Electro-Mechanical Systems), che richiedono una definizione geometrica precisa e compatta.
Integrazione funzionale in un singolo processo
Uno dei vantaggi più rilevanti della manifattura additiva in questo ambito è la possibilità di integrare più funzioni all’interno dello stesso componente. Questo approccio consente, ad esempio, di produrre microdispositivi con percorsi fluidici incorporati, elementi piezoelettrici o interfacce elettriche, eliminando le fasi di assemblaggio successive.
Questa capacità integrativa rappresenta un punto di discontinuità rispetto alle tecnologie precedenti, dove le funzioni meccaniche, elettriche e fluidiche erano necessariamente gestite tramite moduli separati da collegare in seguito.
Nuove classi di materiali per applicazioni funzionali
L’analisi si concentra anche sui materiali che possono essere impiegati con queste tecnologie additive. Tra le novità più rilevanti vi sono i polimeri conduttivi, utili per realizzare piste elettriche o sensori integrati, e i compositi piezoelettrici, che permettono di fabbricare attuatori e dispositivi di rilevamento sensibili alla pressione o alla vibrazione.
L’ampliamento della gamma di materiali stampabili rende possibile lo sviluppo di dispositivi multifunzionali in scala ridotta, mantenendo un controllo preciso sulle proprietà meccaniche, elettriche e strutturali.
Possibili applicazioni e prospettive future
Lo studio suggerisce che la stampa 3D su scala micro e nano potrà avere un impatto concreto nello sviluppo di sistemi avanzati in vari settori, tra cui:
-
Sensori indossabili, che richiedono geometrie adattabili e materiali leggeri
-
Dispositivi lab-on-a-chip, per analisi mediche decentralizzate e compatte
-
Sistemi MEMS personalizzati, progettati per esigenze specifiche in ambito aerospaziale, biomedicale o ambientale
L’equilibrio tra libertà di progettazione, versatilità dei materiali e possibilità di integrazione funzionale potrebbe rendere la stampa 3D una delle tecniche più adatte alla produzione della prossima generazione di microdispositivi.
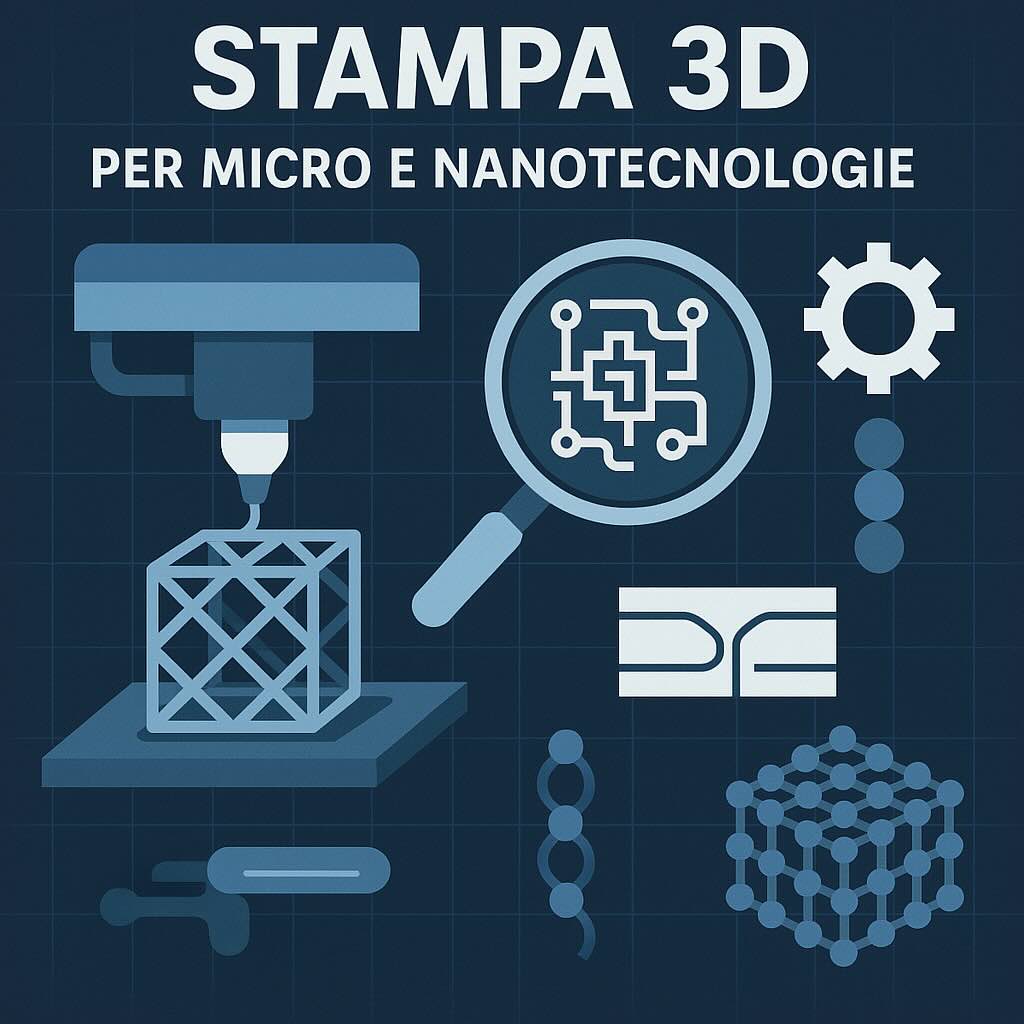