Introduzione alla Stampa 3D a Unico Sistema
I ricercatori del Lawrence Livermore National Laboratory (LLNL), in collaborazione con l’Università della California a Santa Barbara, hanno progettato un processo di stampa 3D capace di realizzare in un solo ciclo sia la struttura portante principale sia i supporti temporanei necessari per geometrie complesse. Invece di passare da un materiale all’altro o di montare e smontare manualmente i supporti, l’intero componente viene fabbricato “one-pot” a partire da un’unica miscela di resina.
Tecnologia Dual-Wavelength DLP
Al centro del sistema c’è una stampante DLP dotata di sorgenti luminose a due lunghezze d’onda: luce ultravioletta per indurire la resina a base di epossidica e luce visibile per polimerizzare un termoplastico degradabile. Il controllo selettivo di ciascuna sorgente consente di posizionare con precisione parti destinatarie a diventare permanenti e zone pensate per svolgere solo funzioni di supporto temporaneo.
Funzione dei Materiali e Procedura Chimica
La formulazione sviluppata comprende un componente epossidico dalle elevate proprietà meccaniche e un polimero termoplastico solubile, che rimane integro durante la fase di costruzione. A processo ultimato, il pezzo viene immerso in una soluzione basica che scioglie i supporti senza lasciare residui, preservando le superfici più delicate e mantenendo intatti gli elementi strutturali.
Vantaggi rispetto ai Supporti Meccanici Tradizionali
Con questo approccio si eliminano i tempi di post-lavorazione dedicati alla rimozione meccanica dei sostegni, spesso causa di imperfezioni o rottura di dettagli sottili. La fase di dissoluzione selettiva rende compatibile la stampa di strutture sospese, aggettanti o a sbalzo, senza ricorrere a impostazioni complicate o a materiali di supporto esterni.
Applicazioni per Elementi Mobili
Una peculiarità della tecnica è la capacità di inserire interfacce solubili in corrispondenza di cerniere e giunti. In tal modo, dispositivi articolati possono essere prodotti già assemblati, con perni e snodi integrati, pronti all’uso dopo il lavaggio finale. Questo apre nuove strade per la stampa di meccanismi compatti e funzionali, come chiusure lampo o dispositivi a scatto.
Efficienza e Sostenibilità
Il metodo riduce il consumo complessivo di materiale, poiché non richiede volumi supplementari di supporto estraneo, e accorcia i tempi di produzione eliminando le operazioni di rifinitura manuale. La dissoluzione in soluzione basica è un processo facilmente automatizzabile e ripetibile in linea di produzione.
Contributo della Partnership Accademica
Il lavoro, presentato su ACS Central Science, ha beneficiato dell’expertise chimica di LLNL e delle competenze in fotonica e modellazione di Santa Barbara. Il confronto tra gruppi di ricerca ha permesso di ottimizzare formulazioni, tempi di esposizione e qualità delle superfici finali.
Contesto nella Manifattura Additiva Multi-Materiale
Nel panorama delle tecnologie per materiali multipli, diverse università e aziende – tra cui MIT, ETH Zurich e aziende come Carbon e 3D Systems – esplorano soluzioni con vasche multiple o getti distinti. La proposta di LLNL si distingue per la semplicità di un solo serbatoio resina e per l’assenza di fasi di cambio materiale.
Prospettive Future
Oltre agli usi industriali in aerospazio, robotica e medicale, il metodo potrà trovare spazio nella produzione di prototipi dotati di dettagli mobili o in settori in cui la precisione delle superfici è critica, ad esempio nella microfluidica o nei dispositivi ottici integrati.
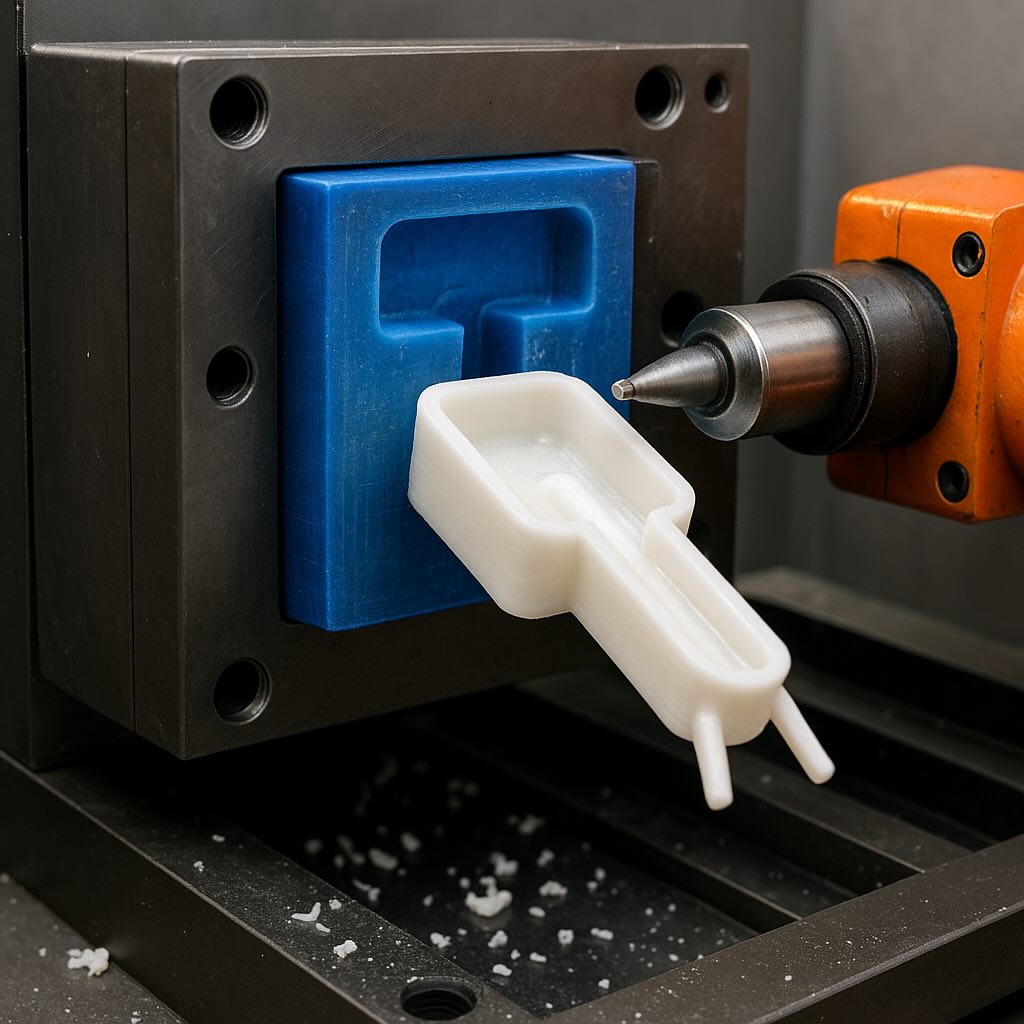