La collaborazione tra URWAHN, TRUMPF e H+E Product Development ha portato allo sviluppo di un nuovo telaio per biciclette in acciaio, chiamato SOFTRIDE, realizzato tramite stampa 3D con tecnologia Laser Powder Bed Fusion (LPBF). Questo progetto rappresenta un’evoluzione concreta nella progettazione e produzione di componenti ciclistici, sfruttando le potenzialità della manifattura additiva.
Una nuova tecnica per costruire telai più leggeri e resistenti
La tecnologia LPBF prevede la fusione di polveri metalliche attraverso un laser ad alta potenza, che consente di ottenere strutture metalliche ad alta densità e precisione. Rispetto alle tecniche tradizionali, questa modalità di produzione permette di creare forme complesse, comprese cavità interne, che riducono il peso complessivo del telaio e ne migliorano le caratteristiche meccaniche.
Grazie a questa soluzione, è stato possibile ottenere un telaio più leggero fino al 30%, mantenendo al tempo stesso un’elevata robustezza. Il processo di stampa additiva consente inoltre una maggiore libertà progettuale, superando i limiti imposti dalle tecniche di lavorazione convenzionali.
Collaborazione e integrazione tra progettazione e produzione
All’interno del progetto, TRUMPF ha messo a disposizione le proprie competenze nella stampa 3D, fornendo i sistemi di produzione e definendo i parametri di lavorazione del materiale. H+E Product Development si è occupata di adattare i processi per la produzione su scala industriale, mentre URWAHN ha rielaborato la progettazione del telaio, aggiornando la geometria per sfruttare al meglio le caratteristiche offerte dalla nuova tecnologia.
Un aspetto rilevante è la possibilità di gestire con precisione la struttura interna del telaio, intervenendo su resistenza ed elasticità a seconda delle esigenze. L’uso di acciai ad alta lega e materiali ottimizzati consente di ottenere solidità strutturale con una quantità minore di materia prima, semplificando al tempo stesso il processo produttivo. Operazioni come la saldatura, spesso necessarie nella produzione tradizionale, non sono più richieste.
Un telaio con nuove caratteristiche funzionali ed estetiche
Il risultato del progetto è un telaio in acciaio che combina caratteristiche funzionali tipiche dell’alluminio con una linea estetica vicina a quella dei telai monoscocca in carbonio. La struttura è stata ulteriormente perfezionata attraverso tecniche di ottimizzazione topologica, con l’obiettivo di migliorare la distribuzione delle sollecitazioni e aumentare l’efficienza complessiva del telaio.
Sono previste tre misure differenti, pensate per soddisfare le esigenze sia del ciclismo urbano che delle bici gravel. L’attenzione alla geometria del telaio mira a garantire un equilibrio tra comfort e prestazioni.
Dallo sviluppo alla produzione in tempi contenuti
L’intero ciclo di sviluppo, dalla progettazione iniziale alla realizzazione in serie, si è completato in meno di otto mesi. I telai vengono prodotti utilizzando il sistema TruPrint 2000 di TRUMPF, installato presso lo stabilimento H+E Product Development a Moritzburg.
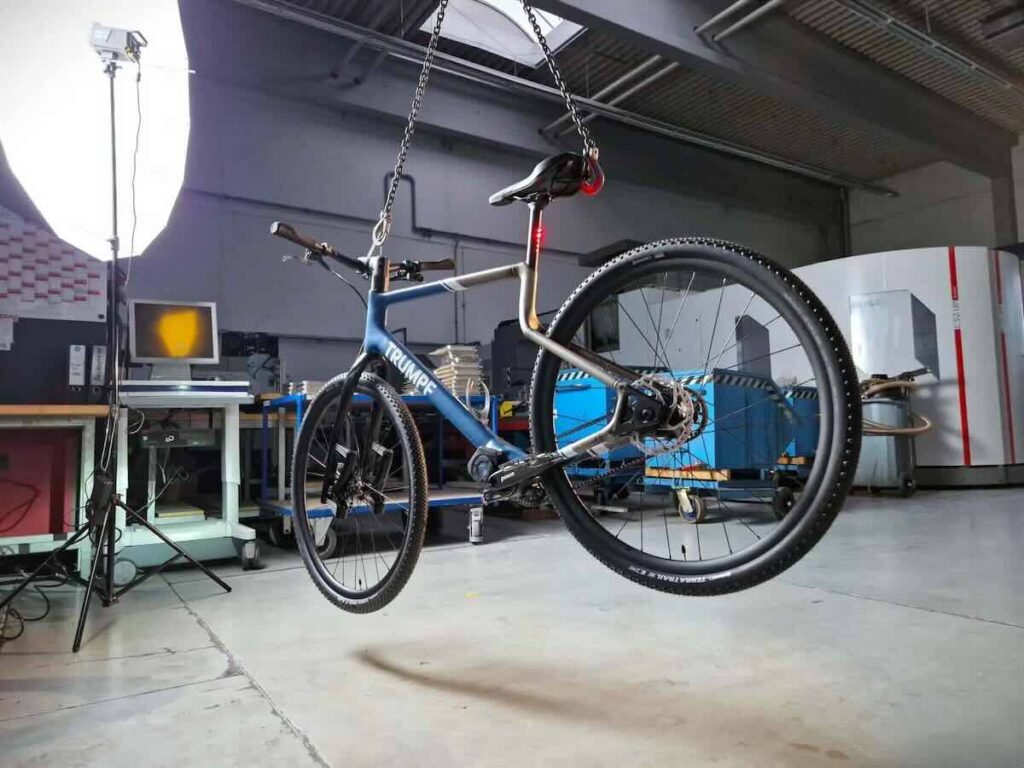