INTERVISTA: IL CEO DI HEADMADE CHRISTIAN STAUDIGEL SOLLEVA IL COPERCHIO SULLA STAMPA 3D COLD METAL FUSION
Da quando ha raccolto 1,9 milioni di euro di finanziamenti tramite la società di venture capital btov Partners nel luglio 2020, l’ufficio di stampa 3D tedesco Headmade ha sollevato le sopracciglia nel settore della produzione additiva.
In particolare, la tecnologia di stampa 3D Cold Metal Fusion (CMF) dell’azienda solleva molte domande. Headmade incoraggia i clienti a rivalutare il metodo di produzione della sinterizzazione laser selettiva (SLS) tramite un nuovo set di parametri di sistema e una polvere infusa con polimeri. Allora, cos’è esattamente CMF? e cosa sta cercando di ottenere Headmade con la sua nuova versione di SLS?
Qui per rispondere a tutte queste domande è il co-fondatore e CEO di Headmade Christian Staudigel. Parlando con l’industria della stampa 3D, Staudigel ha spiegato il potenziale di CMF e ha elaborato gli obiettivi e gli obiettivi più ampi dell’azienda.
“La nostra tecnologia Cold Metal Fusion basata sulla sinterizzazione è stata sviluppata per la produzione in serie di un massimo di 100.000 parti metalliche all’anno, il tutto utilizzando un ecosistema esistente di macchine e processi”, ha affermato Staudigel. “Ciò consente ai clienti di scalare da un punto di ingresso molto efficiente in termini di capitale, fino a una produzione di produzione molto elevata.”
“ABBIAMO L’AMBIZIONE DI SVOLGERE UN RUOLO CHIAVE NELLA REINVENZIONE DEL MERCATO MANIFATTURIERO”.
Headmade è stata fondata a Würzburg, in Germania, nel 2019 dopo essere stata scorporata dall’istituto di ricerca sui polimeri locale Das Kunststoff-Zentrum (SKZ). Staudigel ha iniziato a sviluppare la tecnologia alla base di CMF cinque anni fa, mentre lavorava a fianco del collega co-fondatore Christian Fischer presso SKZ.
Catturati dall’idea che fosse possibile una forma più efficiente di stampa 3D seriale, i due iniziarono a progettare un processo che avrebbe reso la produzione additiva più economica e più accessibile di prima. Il risultato del loro duro lavoro e innovazione è stata la stampa 3D CMF, un metodo che combina ampiamente la sinterizzazione del metallo con SLS in una nuova tecnica di produzione.
Dopo aver raccolto 1,9 milioni di euro di investimenti, la start-up si sta allontanando da SKZ per creare una propria struttura e diventare completamente indipendente. Sfruttando il finanziamento aggiuntivo, i due intendono “ampliare” la loro tecnologia, sviluppando i servizi di marketing e clienti dell’azienda in una rete più ampia. Con ulteriori round di finanziamento in futuro, Staudigel ritiene che Headmade potrebbe espandersi ulteriormente in una serie di nuovi mercati e territori.
“Lavoriamo sulla tecnologia da cinque anni e la partnership con btov Partners ci offre ora l’opportunità di accelerare lo sviluppo dell’azienda e realizzare la nostra visione della produzione in serie 3D”, ha affermato Staudigel. “Ma la partnership con btov Partners è solo il primo passo e prevediamo di raccogliere ulteriori fondi nel 2021 per commercializzare la nostra tecnologia e i nostri prodotti nei mercati più importanti”.
La principale differenza tra la tecnologia CMF di Headmade e la produzione SLS convenzionale è il materiale di stampa 3D proprietario dell’azienda. La materia prima in polvere di metallo Headmade è integrata con una matrice di legante plastico che ne migliora la scorrevolezza e aumenta il numero di macchine con cui è compatibile.
L’intero processo CMF in quattro fasi inizia con l’upscaling del file CAD di un oggetto di destinazione, un passaggio necessario per tenere conto del restringimento causato dal legante plastico della resina. In un approccio simile alla stampa 3D SLS, la parte viene quindi prodotta in modo strato per strato, ma a una temperatura inferiore a 80 o C. Il funzionamento a una temperatura inferiore riduce al minimo i tempi di riscaldamento e raffreddamento in modo significativo e previene la necessità di dispositivi di raffreddamento.
“NONOSTANTE LA COMPOSIZIONE DELLA POLVERE E I PARAMETRI DI ELABORAZIONE REGOLATI, NON È DIVERSO DAL FUNZIONAMENTO DI UNA NORMALE STAMPANTE 3D SLS PER GLI UTENTI.”
“Temperature più basse offrono vantaggi come risparmio di energia e tempo, nonché usura ridotta e requisiti inferiori al sistema SLS per quanto riguarda i componenti e l’isolamento”, ha affermato Staudigel. “Quindi abbiamo progettato la nostra materia prima per l’elaborazione SLS a bassa temperatura, ma ovviamente continuiamo a introdurre la temperatura nel nostro processo nelle fasi successive della sinterizzazione”.
Dopo la fase di stampa iniziale, le parti fabbricate vengono quindi disincrostate, post-elaborate, decerate e sinterizzate. Il legante plastico contenuto nella resina in polvere proprietaria di Headmade viene utilizzato solo come struttura di supporto e non fa differenza per la composizione del componente finale. Di conseguenza, il polimero viene completamente sciolto durante la stampa, lasciando parti che secondo quanto riferito sono paragonabili a quelle prodotte utilizzando lo stampaggio a iniezione.
Supportare i clienti con le stampanti 3D esistenti
Il passaggio a CMF non richiede agli utenti di introdurre ulteriori piastre di costruzione o strutture di supporto, il che significa che il processo può essere applicato all’interno di qualsiasi macchina SLS. Di conseguenza, il servizio di supporto dell’azienda è rivolto ai clienti che cercano di risparmiare denaro aggiornando anziché sostituire le loro stampanti 3D esistenti.
“Dal momento che il nucleo del processo risiede nelle materie prime prodotte dalla nostra testata, l’obiettivo è quello di consentire ai nostri clienti di produrre autonomamente le loro parti”, ha affermato Staudigel. “Abbiamo il know-how e la catena di processo per supportarli nella costruzione, lavorazione e produzione di parti di prova e produzione di piccole serie”.
Con la principale differenza tra la normale produzione SLS e CMF essendo la resina infusa con legante Headmade, l’azienda attualmente fornisce un servizio di supporto piuttosto che uno di produzione. Secondo Staudigel, Headmade è pronta a collaborare con una serie di partner industriali in futuro, al fine di fornire la suite più completa di soluzioni possibili per i suoi clienti.
“Se una produzione interna non è ciò che i nostri clienti desiderano, possiamo ampliare la nostra rete”, ha concluso Staudigel, “Quindi possiamo collegarli ai fornitori di servizi per stabilire una catena di fornitura per le loro esigenze specifiche”.
Ricerca continua per ottimizzare la stampa 3D SLS
Negli ultimi anni numerosi ricercatori e aziende di produzione additiva hanno adottato il proprio approccio per ottimizzare la stampa SLS. Sebbene i principi fondamentali strato per strato di SLS siano stati spesso mantenuti all’interno di sistemi sperimentali, hanno anche caratterizzato una maggiore compatibilità dei materiali e una gamma di funzioni aggiuntive.
I ricercatori della School of Engineering della Columbia University hanno dimostrato un nuovo processo di stampa SLS che consente la sinterizzazione di più polveri all’interno della stessa tiratura di stampa. Invertendo il laser all’interno di un sistema SLS in modo che punti verso l’alto, il team è stato in grado di creare prototipi contenenti due diversi polimeri all’interno dello stesso strato.
Il produttore di stampanti 3D Aerosint ha introdotto un’alternativa di stampa SLS multi-polvere denominata “Deposizione selettiva di polvere”. Composto da un distributore di polvere e tamburi di modellatura, il metodo dell’azienda deposita selettivamente polvere fine per realizzare parti stampate in 3D multi-metallo.
La stampante 3D tedesca OEM EOS ha sviluppato la sua suite brevettata di monitoraggio in-process EOSTATE utilizzando anni di dati, per consentire l’identificazione delle irregolarità durante il processo di stampa SLS. Sfruttando una fotocamera integrata, gli utenti possono identificare rapidamente i livelli incompleti e interrompere il processo per correggere eventuali problemi.
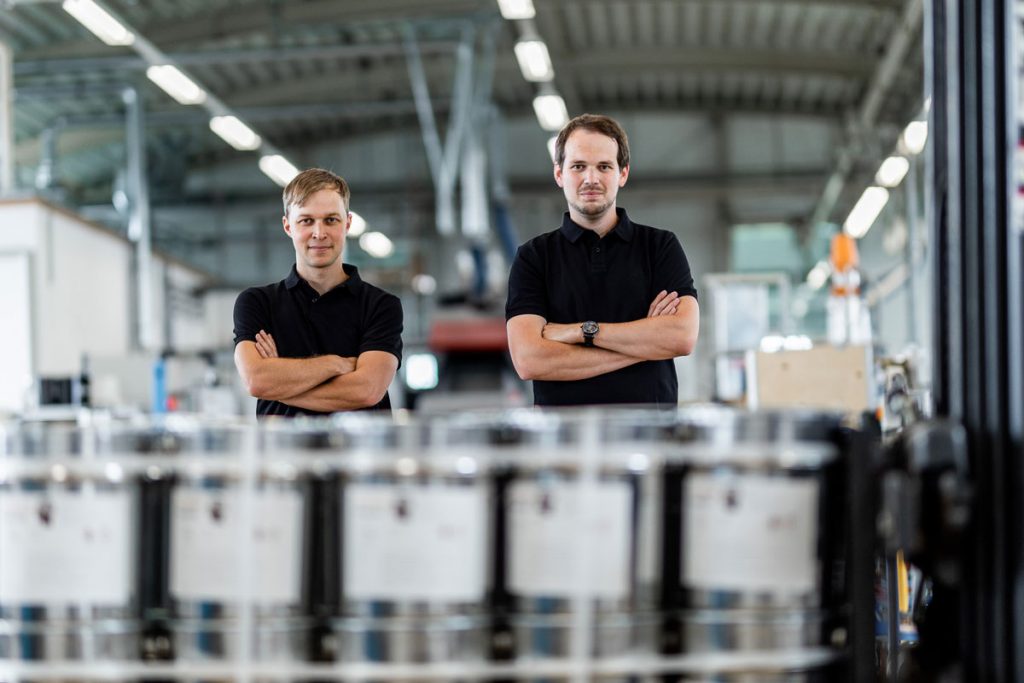