Desktop Metal lancia Studio System 2, eliminando la fase di debind del solvente
Desktop Metal ha annunciato il lancio di una versione aggiornata della sua piattaforma di stampa 3D in metallo Studio System adatta all’ufficio.
Si dice che Studio System 2 mantenga tutte le caratteristiche critiche della macchina che è stata inizialmente resa disponibile nel 2018, ma vanta anche diversi progressi progettati per rendere la tecnologia più affidabile e accessibile. Impostato per la spedizione entro la fine dell’anno, rappresenta il secondo aggiornamento del sistema Studio dopo i miglioramenti apportati a settembre 2018 . Segue gli aggiornamenti alla linea del sistema di produzione dell’azienda nel dicembre 2020.
Nel lancio di Studio System 2, si dice che Desktop Metal abbia abilitato un flusso di lavoro di stampa e sinterizzazione in due fasi, eliminando la necessità della fase di debind del solvente inizialmente richiesta con la piattaforma originale. L’azienda è riuscita a farlo con “formulazioni di materiali completamente nuove” che facilitano il trasferimento di parti direttamente dalla stampante al forno, ottenendo “esperienze quasi a mani libere” che possono ridurre l’uso di materiali di consumo e l’ingombro complessivo del sistema.
Si dice che i nuovi profili di stampa e un materiale dello strato di interfaccia riprogettato riducano al minimo i tentativi e gli errori garantendo un ritiro più uniforme nel processo di sinterizzazione e un maggiore successo delle parti su una serie di geometrie. I nuovi profili di stampa si combinano anche con la camera di costruzione riscaldata della macchina per aiutare a migliorare la finitura superficiale sulle pareti laterali e sulle superfici rivolte verso il supporto. La capacità di sfruttare il nuovo riempimento isotropico TMPS consente di creare parti più resistenti, mentre la sinterizzazione sottovuoto a temperature fino a 1400 ° C consente a Studio System 2 di produrre parti che vantano proprietà meccaniche simili agli standard MPIF (Metal Powder Industrial Federation), secondo a Desktop Metal.
C’è anche l’immediata aggiunta della possibilità di stampare con acciaio inossidabile 316L, con un “ampio portafoglio” di metalli aggiuntivi che verrà rilasciato entro la fine dell’anno. Lo Studio System 2 è anche “retrocompatibile” grazie all’uso dell’unità debinder con tutti i materiali precedentemente supportati dallo Studio System originale, inclusi acciaio inossidabile 17-4PH, acciaio per utensili H13 e rame. Sul lato software, si dice che Fabricate semplifichi la preparazione della costruzione con i nuovi profili di stampa, generi strutture di supporto separabili con spaccature strategiche per evitare il bloccaggio durante la post-elaborazione e automatizzi completamente i cicli di debind termico e sinterizzazione.
“Con l’avanzare dell’adozione della produzione additiva in tutto il mondo, Desktop Metal continua a promuovere innovazioni che consentono alla tecnologia di competere in modo più efficace con i processi di produzione convenzionali”, ha commentato Ric Fulop, CEO e co-fondatore di Desktop Metal. “La nostra prossima generazione di Studio System 2 prende le migliori caratteristiche dell’originale Studio System + e le migliora significativamente, offrendo parti metalliche di uso finale di qualità superiore attraverso un processo più snello e accessibile e con un ingombro ancora più piccolo.”
Studio System 2 sarà disponibile a livello globale nel primo trimestre del 2021 e sarà disponibile tramite un aggiornamento a tutti gli utenti esistenti della macchina originale. Desktop Metal afferma di avere centinaia di clienti in 30 paesi che attualmente utilizzano lo Studio System, tra cui Ford Motor Company, BMW Group, Google ATAP , Stanley Black & Decker, Lockheed Martin e Goodyear Tire & Rubber Company. Con il rilascio del sistema nuovo e migliorato, Desktop Metal si aspetta che questi utenti aprano nuove applicazioni nei rispettivi settori.
“Sulla base del successo del nostro Studio System originale, sappiamo che le aziende di tutto il mondo sono ansiose di adottare il nostro nuovo e più snello processo Studio System 2 per produrre parti difficili da lavorare con geometrie complesse come sottosquadri e canali interni”, ha aggiunto Fulop . “In tutta la produzione, la strumentazione, l’automotive, i prodotti di consumo, l’elettronica e le applicazioni mediche, le aziende condividono come la produzione additiva stia sfidando i loro team di progettazione e ingegneria a pensare in modo diverso su come ottimizzare i progetti per il miglior successo delle parti”.
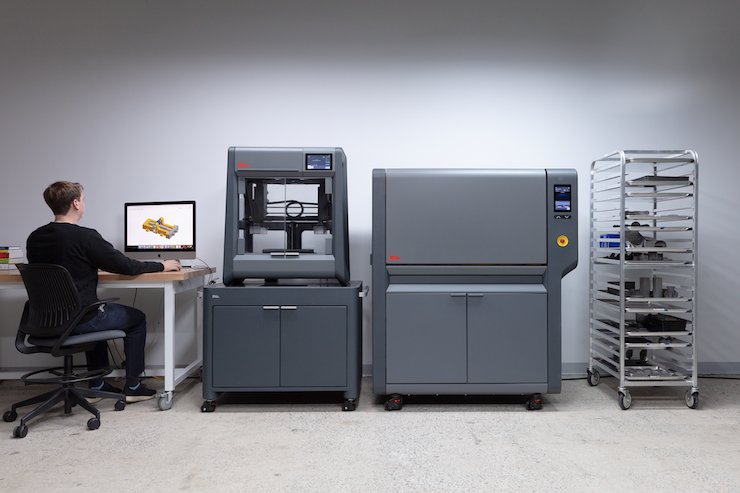