STEWART-HAAS CERCA IL VANTAGGIO NASCAR CON PEDALI DEI FRENI STAMPATI IN 3D PIÙ LEGGERI DEL 32%
Il team NASCAR Stewart-Haas Racing si è rivolto alla stampa 3D nel tentativo di migliorare le prestazioni dei freni montati su uno dei suoi sfidanti per il campionato di quest’anno.
In collaborazione con Autodesk , Stewart-Haas è riuscita a utilizzare il software di progettazione generativa Fusion 360 per rendere i pedali dei freni più leggeri del 32%, aumentandone al contempo la rigidità e la sicurezza complessiva. Stampato in 3D tramite il sistema RenAM 500Q di Renishaw , il pedale rinnovato è stato ora installato sulla Ford Mustang da 750 CV di Cole Custer, con l’obiettivo di far crollare i suoi tempi sul giro e aiutarlo a scalare la classifica della Cup Series .
“Essere in grado di utilizzare sia il design generativo di Autodesk che le capacità di stampa su metallo di Renishaw sbloccherà porte non disponibili in precedenza utilizzando i metodi di produzione tradizionali”, ha affermato Walter Mitchell, Engineering Integration Manager presso Stewart-Haas Racing, “portando a prestazioni migliorate, velocità più elevate e giri ridotti volte.”
Mettere i freni sul peso
Come ogni sport automobilistico, la NASCAR si basa su margini sottili e squadre che spingono i loro progetti ai limiti assoluti dei regolamenti dello sport, per ottenere un vantaggio competitivo. Con le sue vetture attualmente al 10°, 23°, 24° e 28° posto in campionato, Stewart-Haas non è diverso e il team ha adottato la stampa 3D all’inizio della stagione con l’obiettivo di sviluppare aggiornamenti che mettano in risalto i suoi piloti.
Prima di passare alla produzione additiva, Stewart-Haas ha collaborato con Autodesk, utilizzando le funzionalità di progettazione iterativa di Fusion 360 per perfezionare e simulare le prestazioni del suo nuovo pedale del freno. Rispetto alla parte convenzionale, il team è stato in grado di rivedere il suo design per presentare complesse strutture interne reticolari e le proiezioni hanno mostrato che era molto più rigido e leggero di prima.
Secondo Mike Grau, che guida il team di ricerca di Autodesk, Fusion 360 si è rivelato fondamentale per l’ottimizzazione del pedale. “In passato, con le tecnologie additive, avevi il problema di ‘Come si crea il progetto di simulazione?'”, ha detto a DesignNews . “Hai tutte queste complesse strutture reticolari e strutture cave. Come si crea un progetto di assieme, ma si fornisce anche un progetto di simulazione?”
Per ottenere ciò, Grau afferma che Autodesk e Stewart-Haas hanno deciso di ridurre al minimo il numero di singoli elementi all’interno del loro design del pedale, per rendere le cose più gestibili. In tal modo, gli ingegneri delle aziende sono stati in grado di creare un reticolo con decine di migliaia di elementi anziché milioni, il che è stato fondamentale per consentire loro di eseguire i processi di simulazione di cui avevano bisogno.
Dopo aver rinnovato il design del pedale del freno, Stewart-Haas lo ha inviato a Renishaw, dove è stato stampato in 3D in titanio e sabbiato per dargli una finitura finale. Tuttavia, data la natura critica per la sicurezza del componente, il team ha dovuto sottoporlo a stress test in condizioni di gara prima dell’uso, quindi lo ha sottoposto all’intero limite di carico di 3.000 libbre del suo dispositivo di prova personalizzato.
Sotto sforzo, il pedale aggiornato non solo è riuscito a resistere ai guasti, ma ha mostrato una rigidità superiore del 50% rispetto al suo predecessore. Per Autodesk, il progetto ha infine dimostrato il potenziale del suo software nell’ambito dell’ottimizzazione delle parti del motorsport e, anche se il processo ha richiesto due mesi per essere completato, l’azienda sostiene che questo lasso di tempo potrebbe essere ridotto drasticamente in futuro.
“[Inizialmente] Ci è voluto un giorno per creare una cella unitaria”, ha concluso Grau. “Due settimane dopo, siamo stati in grado di creare 30 celle unitarie in 30 minuti, ma il computer si è bloccato alcune volte. Sei mesi dopo potremmo realizzare un intero reticolo di un progetto in pochi minuti. I progressi che stiamo facendo sono quasi esponenziali se guardi da dove veniamo e cosa facciamo”.
I produttori di automobili si stanno rivolgendo sempre più all’ottimizzazione della topologia e alla progettazione generativa come mezzo per sviluppare parti stampabili in 3D con applicazioni per uso finale. Proprio l’anno scorso, Fraunhofer IAPT ha collaborato con gli ingegneri di Fiat Chrysler Automobiles per consolidare dodici componenti di una delle sue auto sportive in un’unica parte di sospensione stampata in 3D , che pesava il 36% in meno rispetto all’originale.
Allo stesso modo, Porsche ha anche collaborato con TRUMPF e MAHLE per la produzione additiva di pistoni del motore aggiornati per la sua supercar 911 di punta. Utilizzando un processo di stampa 3D guidato dall’intelligenza artificiale, il produttore è stato in grado di integrare un condotto di raffreddamento nella “corona” dei pistoni sperimentali, che una volta montati, hanno effettivamente aggiunto 30 CV al motore del veicolo.
In termini di freni in particolare, diverse aziende automobilistiche hanno giocato con l’idea di componenti relativi alla stampa 3D negli ultimi due anni. A luglio 2019, Carbon Performance ha utilizzato la sua piattaforma proprietaria SK3L370N per stampare le pinze dei freni in 3D , poco dopo che Bugatti è riuscita a ottenere qualcosa di simile, producendo pinze in titanio con un sistema SLM 500 .
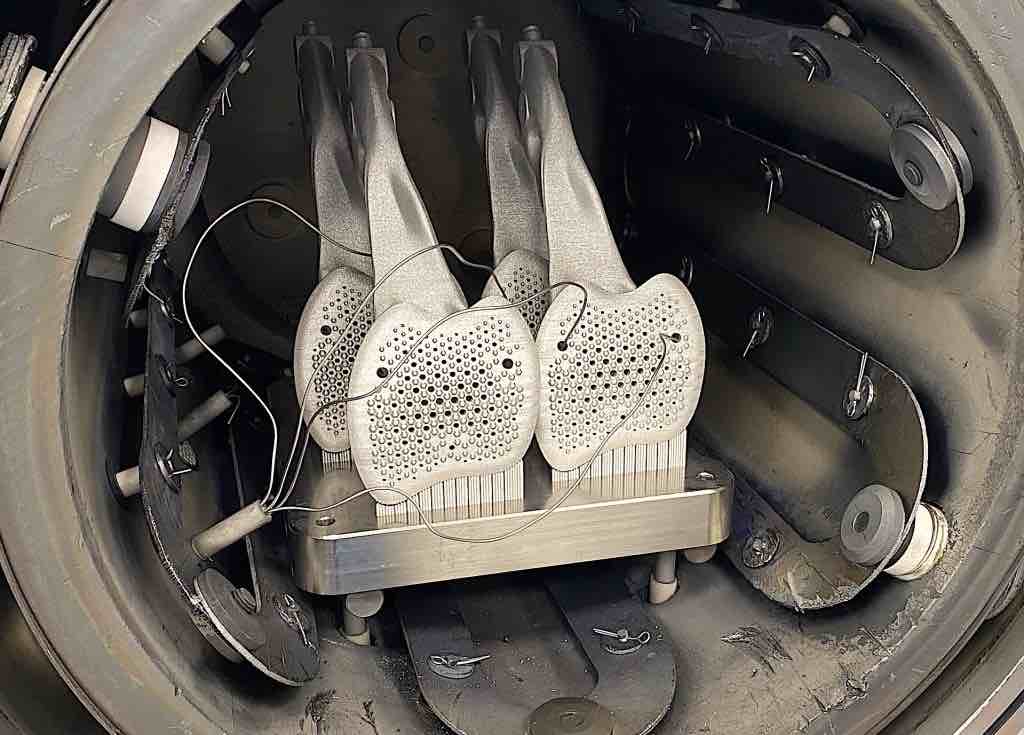